The MPCVD (Microwave Plasma Chemical Vapor Deposition) process is a sophisticated technique used to deposit high-quality diamond films and other materials. It involves the use of microwave energy to excite gas into a plasma state, which then facilitates the deposition of materials onto a substrate. This method is particularly valued for its ability to produce large-area, high-purity, and uniform films with excellent crystal morphology. The process is highly controlled, ensuring that the plasma is generated in a way that maximizes the quality and efficiency of the deposition.
Key Points Explained:
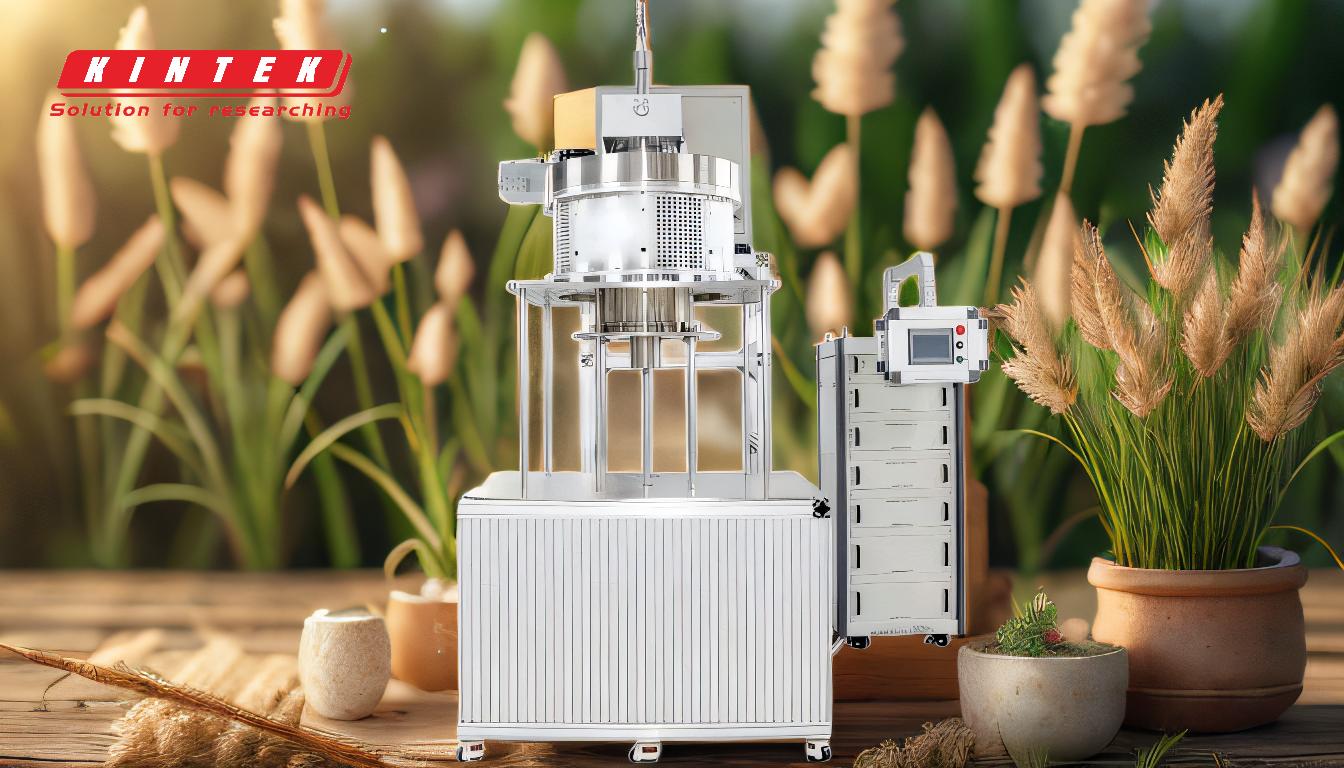
-
Microwave Energy and Plasma Generation:
- The core of the MPCVD process is the use of microwave energy to excite the gas into a plasma state. This is achieved by placing the gas in a resonant cavity where microwaves create an electromagnetic field. The electrons in the gas collide and oscillate within this field, leading to a high degree of ionization and the formation of a dense plasma. This plasma is rich in reactive species, such as atomic hydrogen and carbon-containing groups, which are crucial for the deposition process.
-
High-Density Plasma Formation:
- The intense microwave energy causes the gas to ionize to a degree that can exceed 10%. This high ionization level results in a plasma that is saturated with reactive species. The presence of supersaturated atomic hydrogen and carbon-containing groups in the plasma significantly enhances the deposition rate and the quality of the diamond film. This is because these reactive species are more likely to interact and form stable bonds on the substrate surface.
-
Deposition Process:
- The high-density plasma created in the resonant cavity is directed towards the substrate where the film is to be deposited. The reactive species in the plasma interact with the substrate surface, leading to the formation of a thin film. The process is carefully controlled to ensure that the film grows uniformly and with the desired properties. The substrate is typically kept at a specific temperature and pressure to optimize the deposition conditions.
-
Advantages of MPCVD:
- Large Preparation Area: MPCVD can be used to deposit films over large areas, making it suitable for industrial applications.
- Good Uniformity: The process ensures that the film is deposited uniformly across the substrate, which is critical for applications requiring consistent material properties.
- High Purity: The use of microwave plasma minimizes contamination, resulting in high-purity films.
- Excellent Crystal Morphology: The films produced by MPCVD have excellent crystal structures, which are essential for applications in electronics and optics.
-
Applications:
- MPCVD is widely used in the production of high-quality diamond films, which are used in various applications such as cutting tools, optical windows, and electronic devices. The ability to produce large-sized single crystal diamonds is particularly valuable in industries requiring high-performance materials.
In summary, the MPCVD process is a highly effective method for depositing high-quality films, particularly diamond films, using microwave-generated plasma. The process is characterized by its ability to produce large-area, uniform, and high-purity films with excellent crystal morphology, making it a preferred choice for many industrial and scientific applications.
Summary Table:
Key Aspect | Details |
---|---|
Microwave Energy | Excites gas into plasma state using electromagnetic fields in a resonant cavity. |
High-Density Plasma | Ionization exceeds 10%, creating reactive species for efficient deposition. |
Deposition Process | Plasma interacts with substrate to form uniform, high-quality thin films. |
Advantages | Large-area, high-purity, uniform films with excellent crystal morphology. |
Applications | Cutting tools, optical windows, electronic devices, and more. |
Interested in MPCVD technology? Contact us today to learn how it can benefit your applications!