The PACVD (Plasma Assisted Chemical Vapor Deposition) process is a specialized coating technique that leverages plasma to deposit thin films onto substrates. It involves a vacuum chamber with two planar electrodes, one of which is radio frequency (r.f.) coupled to the power supply. This setup enables the coating of thin planar substrates up to 20 cm in diameter. The high-energy electrons in the plasma provide the necessary energy for chemical reactions, resulting in the deposition of thin films on the workpiece surfaces. While the provided references primarily discuss PVD (Physical Vapor Deposition), the PACVD process shares similarities in terms of vacuum conditions and the use of reactive gases, but it differs in its reliance on plasma to drive the chemical reactions necessary for coating.
Key Points Explained:
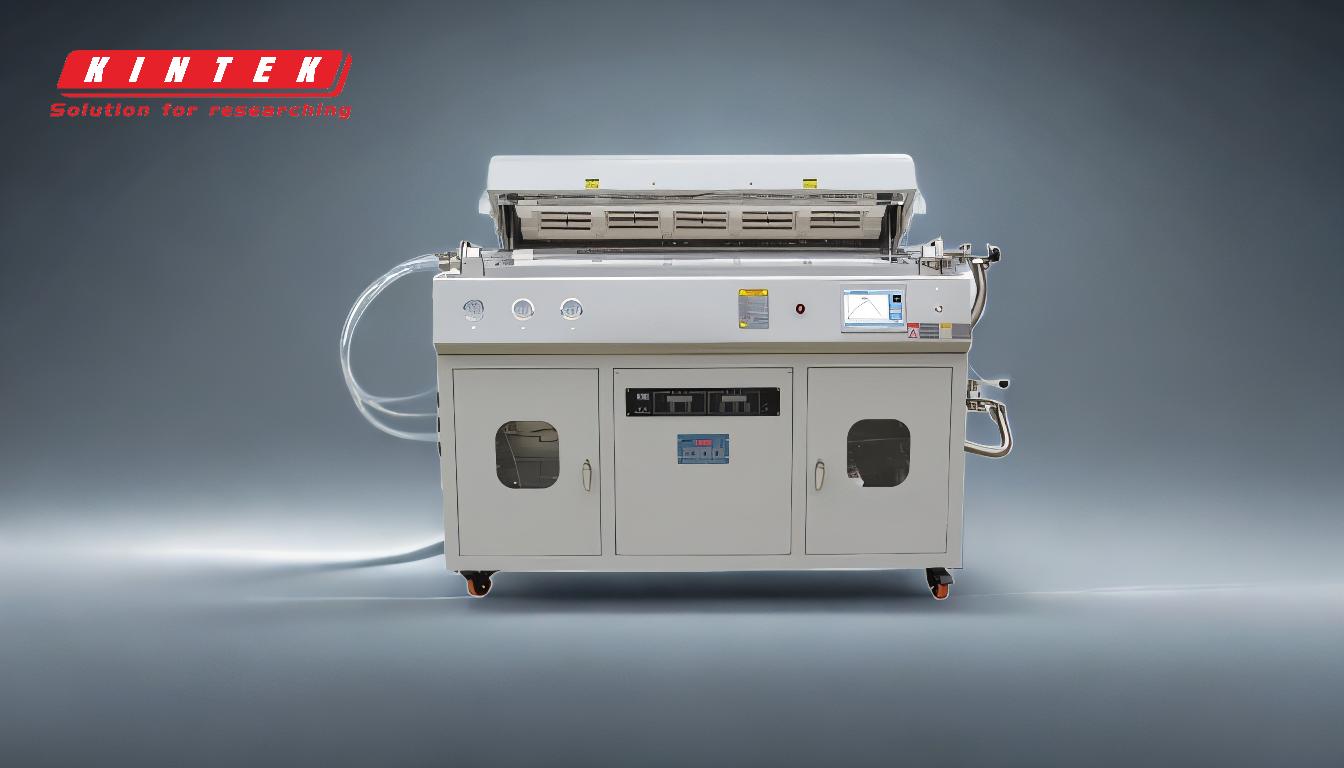
-
Vacuum Chamber Setup:
- The PACVD process occurs in a vacuum chamber equipped with two planar electrodes. One of these electrodes is radio frequency (r.f.) coupled to the power supply, which is crucial for generating the plasma.
- The vacuum environment minimizes contamination and allows for precise control over the deposition process.
-
Plasma Generation:
- The r.f. coupled electrode generates a plasma within the chamber. Plasma consists of high-energy electrons and ions that provide the energy needed to drive chemical reactions.
- This plasma is essential for breaking down precursor gases into reactive species that can form the desired thin film on the substrate.
-
Substrate Preparation:
- Substrates must be cleaned and prepared before the PACVD process to ensure proper adhesion and quality of the coating. This step is critical for achieving a uniform and durable film.
- The process can accommodate thin planar substrates up to 20 cm in diameter, making it suitable for a variety of applications.
-
Chemical Reactions:
- The high-energy electrons in the plasma facilitate the breakdown of precursor gases into reactive species. These species then react to form the desired thin film on the substrate.
- The chemical reactions are carefully controlled to achieve specific properties in the deposited film, such as hardness, adhesion, or corrosion resistance.
-
Deposition of Thin Films:
- The reactive species generated in the plasma deposit onto the substrate, forming a thin film. This deposition occurs at an atomic or molecular level, ensuring a high degree of precision and uniformity.
- The process allows for the creation of films with tailored properties, depending on the precursor gases and process parameters used.
-
Advantages of PACVD:
- The use of plasma in PACVD allows for lower process temperatures compared to traditional CVD (Chemical Vapor Deposition), making it suitable for temperature-sensitive substrates.
- The process can produce high-quality, dense, and adherent films with excellent mechanical and chemical properties.
-
Comparison with PVD:
- While both PACVD and PVD are vacuum-based coating techniques, PACVD relies on chemical reactions driven by plasma, whereas PVD involves the physical vaporization of a target material.
- PACVD is particularly advantageous for applications requiring complex chemical compositions or where lower processing temperatures are necessary.
By understanding these key points, it becomes clear that the PACVD process is a powerful tool for depositing high-quality thin films with precise control over their properties. This makes it an attractive option for various industrial applications, including electronics, optics, and surface engineering.
Summary Table:
Key Aspect | Description |
---|---|
Vacuum Chamber Setup | Uses two planar electrodes, one r.f. coupled, for plasma generation in a vacuum. |
Plasma Generation | High-energy electrons and ions drive chemical reactions for thin film deposition. |
Substrate Preparation | Substrates are cleaned and prepared for uniform and durable coatings. |
Chemical Reactions | Precursor gases break into reactive species to form tailored thin films. |
Deposition of Thin Films | Reactive species deposit at an atomic/molecular level for precise, uniform films. |
Advantages of PACVD | Lower temperatures, high-quality films, and suitability for sensitive substrates. |
Comparison with PVD | PACVD uses plasma-driven chemical reactions; PVD relies on physical vaporization. |
Discover how PACVD can enhance your coating applications—contact our experts today for more information!