Physical Vapor Deposition (PVD) plating is a sophisticated process used to deposit thin layers of material onto a substrate. It involves creating a vapor from a solid material, which then condenses onto the substrate to form a thin film. This process is carried out in a vacuum environment to ensure purity and precision. The PVD process is widely used in various industries due to its ability to produce durable, high-quality coatings with excellent mechanical, chemical, and optical properties.
Key Points Explained:
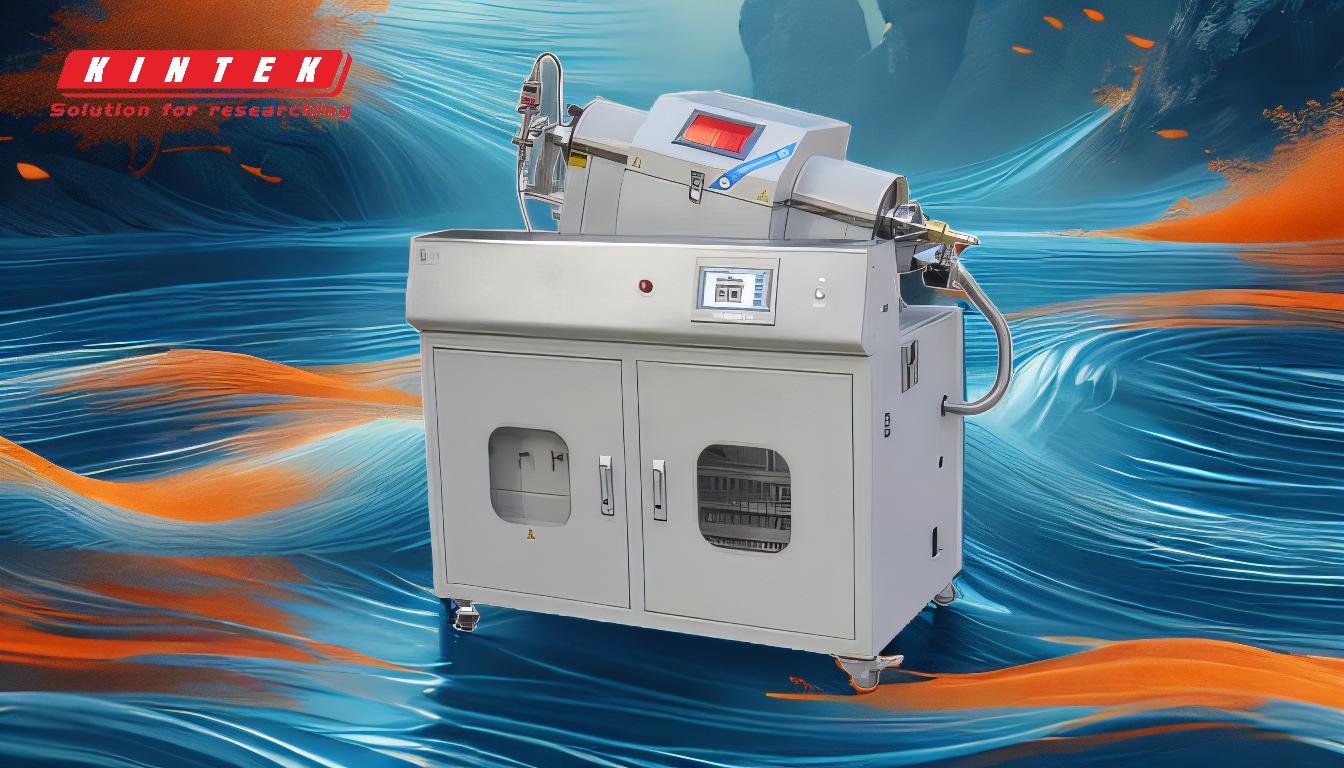
-
Cleaning the Substrate:
- Before the PVD process begins, the substrate must be thoroughly cleaned to remove any contaminants. This step is crucial because any impurities on the surface can affect the adhesion and quality of the coating. Cleaning methods may include ultrasonic cleaning, chemical cleaning, or plasma cleaning.
-
Creating a Vacuum Environment:
- The PVD process takes place in a vacuum chamber to eliminate any atmospheric gases that could interfere with the deposition. A high vacuum is essential to ensure that the vaporized material can travel unimpeded to the substrate.
-
Vaporization of the Target Material:
- The material to be deposited, known as the target, is vaporized using various techniques such as sputtering, arc evaporation, or electron beam evaporation. In sputtering, high-energy ions bombard the target, causing atoms to be ejected from its surface. In arc evaporation, an electrical arc is used to vaporize the target material.
-
Formation of Plasma:
- A plasma is created by ionizing a gas, typically argon or nitrogen, within the vacuum chamber. The plasma consists of highly energetic ions and electrons that can interact with the vaporized target material. This step is crucial for the ionization and activation of the vaporized atoms.
-
Reaction with Reactive Gases:
- Reactive gases such as nitrogen or oxygen are introduced into the chamber. These gases react with the vaporized target material to form compounds. For example, if the target material is titanium and the reactive gas is nitrogen, the resulting compound would be titanium nitride (TiN), which is known for its hardness and wear resistance.
-
Deposition onto the Substrate:
- The vaporized and ionized material, now in the form of a compound, is deposited onto the substrate. The deposition occurs atom by atom, resulting in a thin, uniform layer. The substrate is typically held at a controlled temperature to ensure proper adhesion and film quality.
-
Testing and Quality Control:
- After the deposition process, the coated components are tested to ensure consistency and quality. Techniques such as X-ray fluorescence (XRF) and spectrophotometry are used to measure the composition, thickness, and color of the coating. This step is essential to verify that the coating meets the required specifications.
-
Advantages of PVD Coating:
- PVD coatings offer several advantages, including high hardness, excellent wear resistance, and good adhesion to the substrate. They also provide excellent chemical and thermal stability, making them suitable for a wide range of applications. Additionally, PVD is an environmentally friendly process as it does not produce harmful by-products.
-
Applications of PVD Coating:
- PVD coatings are used in various industries, including automotive, aerospace, medical, and electronics. Common applications include coating cutting tools, molds, and components that require high wear resistance and durability. PVD coatings are also used in decorative applications due to their ability to produce a wide range of colors and finishes.
In summary, the PVD plating process is a highly controlled and precise method for depositing thin films onto substrates. It involves several critical steps, from cleaning the substrate to testing the final coating, ensuring that the resulting product meets the highest standards of quality and performance. The versatility and environmental benefits of PVD make it a preferred choice for many industrial applications.
Summary Table:
Step | Description |
---|---|
1. Cleaning the Substrate | Remove contaminants using ultrasonic, chemical, or plasma cleaning. |
2. Creating a Vacuum | Establish a high vacuum environment to ensure purity and precision. |
3. Vaporization | Vaporize the target material via sputtering, arc evaporation, or electron beam. |
4. Plasma Formation | Ionize gas (e.g., argon or nitrogen) to create a plasma for activation. |
5. Reaction with Gases | Introduce reactive gases to form compounds like titanium nitride (TiN). |
6. Deposition | Deposit the vaporized material onto the substrate atom by atom. |
7. Testing & Quality | Use XRF and spectrophotometry to verify coating thickness and quality. |
8. Advantages | High hardness, wear resistance, chemical stability, and eco-friendliness. |
9. Applications | Used in automotive, aerospace, medical, and electronics industries. |
Discover how PVD plating can enhance your products—contact our experts today for a consultation!