The process of a pyrolysis furnace involves the thermal decomposition of organic materials, such as plastic waste, in the absence of oxygen, leading to the production of oil gas, non-condensable gas, and other byproducts. This process is carried out under high-temperature conditions, where the oil gas is condensed into liquid form and collected, while non-condensable gas is recycled as fuel. The process is complex and involves several steps, including waste preparation, pyrolysis, and product purification. Operating a pyrolysis furnace requires careful handling due to the high temperatures, pressures, and potential hazards involved.
Key Points Explained:
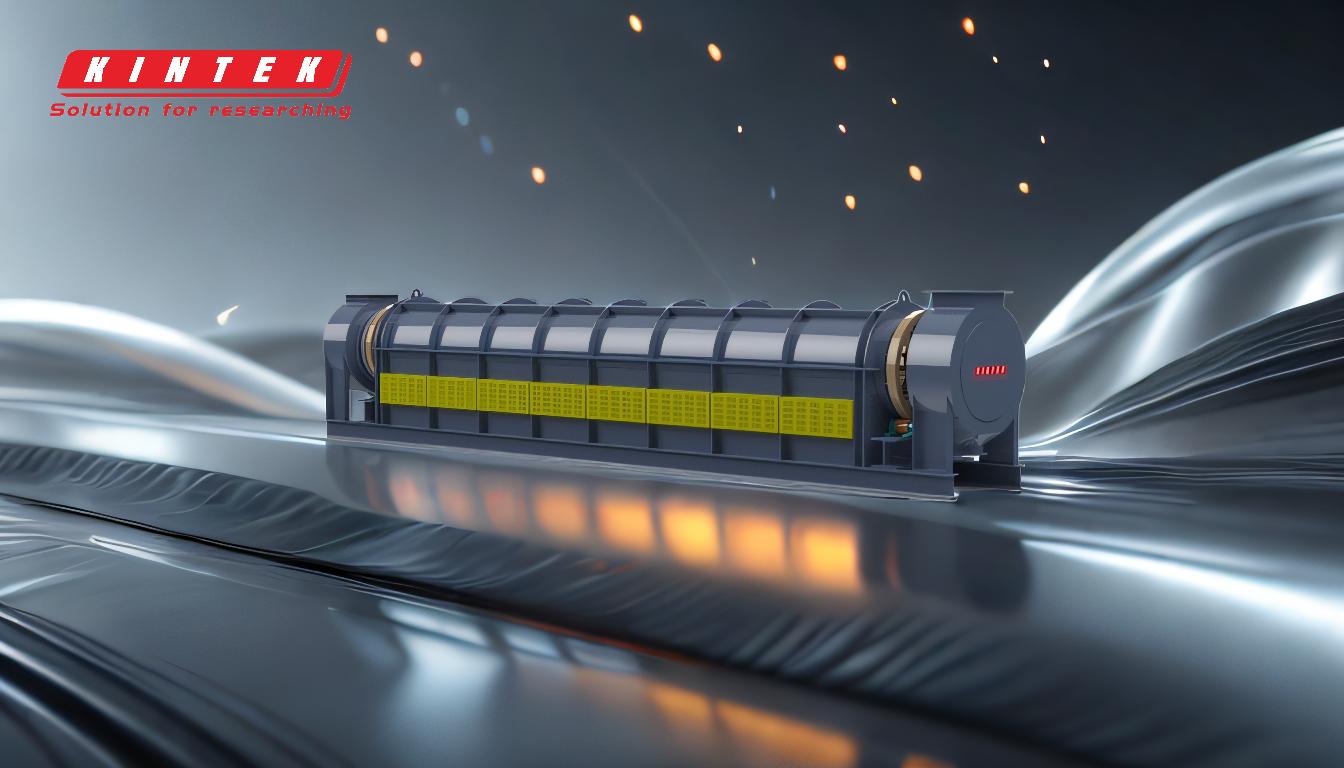
-
Preparation of Waste Material:
- Shredding and Drying: Before pyrolysis, plastic waste is shredded into smaller pieces to increase the surface area for more efficient thermal decomposition. The shredded material is then dried to remove any moisture, which can interfere with the pyrolysis process.
- Preprocessing: Non-plastic materials are separated from the plastic waste to ensure that only suitable materials are fed into the pyrolysis furnace. This step is crucial to prevent contamination and ensure the quality of the end products.
-
Pyrolysis Process:
- Thermal Decomposition: The dried and preprocessed plastic waste is fed into the pyrolysis furnace, where it is heated to high temperatures (typically between 300°C to 900°C) in the absence of oxygen. This causes the plastic to break down into smaller molecules, producing oil gas, non-condensable gas, and solid residues.
- Condensation: The oil gas produced during pyrolysis is passed through a condenser, where it is cooled and liquefied. The resulting liquid, known as pyrolysis oil, is collected in an oil tank for further processing or storage.
- Recycling of Non-Condensable Gas: The non-condensable gas generated during pyrolysis, which cannot be liquefied, is recycled back into the furnace as a heating fuel. This recycling process enhances the energy efficiency of the system and reduces the need for external fuel sources.
-
Distillation and Purification:
- Distillation: The collected pyrolysis oil undergoes a distillation process to separate it into different fractions based on their boiling points. This step is essential for refining the oil into usable products such as diesel, gasoline, or other chemicals.
- Purification: The distilled oil may undergo further purification to remove any remaining impurities, ensuring that the final product meets the required quality standards.
-
Storage and Dispatch:
- After purification, the pyrolysis oil is stored in tanks until it is ready to be dispatched for use or sale. Proper storage conditions are maintained to prevent degradation or contamination of the oil.
-
Safety and Maintenance:
- Hazard Management: Operating a pyrolysis furnace involves high temperatures and pressures, which can pose significant safety risks. Proper safety protocols, including the use of protective equipment and regular maintenance, are essential to prevent accidents and ensure the longevity of the equipment.
- Corrosion and Maintenance: The high temperatures and chemical reactions involved in pyrolysis can lead to corrosion and other maintenance issues. Regular inspections and maintenance are necessary to keep the furnace operating efficiently and safely.
-
Environmental Considerations:
- Contained Pyrolysis: The process of contained pyrolysis ensures that the thermal destruction of organic matter is carried out in a controlled environment, minimizing the release of harmful emissions. This process also hardens inorganic waste, making it easier to handle and dispose of safely.
In summary, the process of a pyrolysis furnace is a complex but highly effective method for converting plastic waste into valuable products such as oil and gas. The process involves several steps, including waste preparation, pyrolysis, condensation, distillation, and purification, all of which require careful management to ensure safety and efficiency. For more information on related equipment, you can explore pyrolysis plant.
Summary Table:
Step | Description |
---|---|
Waste Preparation | Shredding, drying, and separating non-plastic materials for efficient pyrolysis. |
Pyrolysis Process | Thermal decomposition at 300°C–900°C, producing oil gas and non-condensable gas. |
Condensation | Cooling oil gas into liquid form (pyrolysis oil) for collection. |
Distillation | Separating pyrolysis oil into usable fractions like diesel or gasoline. |
Purification | Removing impurities to meet quality standards. |
Storage & Dispatch | Storing purified oil in tanks for future use or sale. |
Safety & Maintenance | Managing hazards, corrosion, and ensuring regular maintenance. |
Environmental Impact | Minimizing emissions and safely handling inorganic waste. |
Discover how a pyrolysis furnace can revolutionize waste management—contact us today for expert guidance!