RF sputtering is a specialized thin-film deposition technique widely used in industries such as semiconductors and electronics. It involves the use of radio frequency (RF) power, typically at 13.56 MHz, to create a plasma in a vacuum chamber filled with inert gas. The process alternates the electrical potential between the target material and the substrate holder, preventing charge buildup on insulating materials. During the positive cycle, electrons are attracted to the target, creating a negative bias, while in the negative cycle, ions bombard the target, ejecting atoms that deposit onto the substrate to form a thin film. This method is particularly effective for depositing insulating materials, ensuring high-quality coatings without arcing or process interruptions.
Key Points Explained:
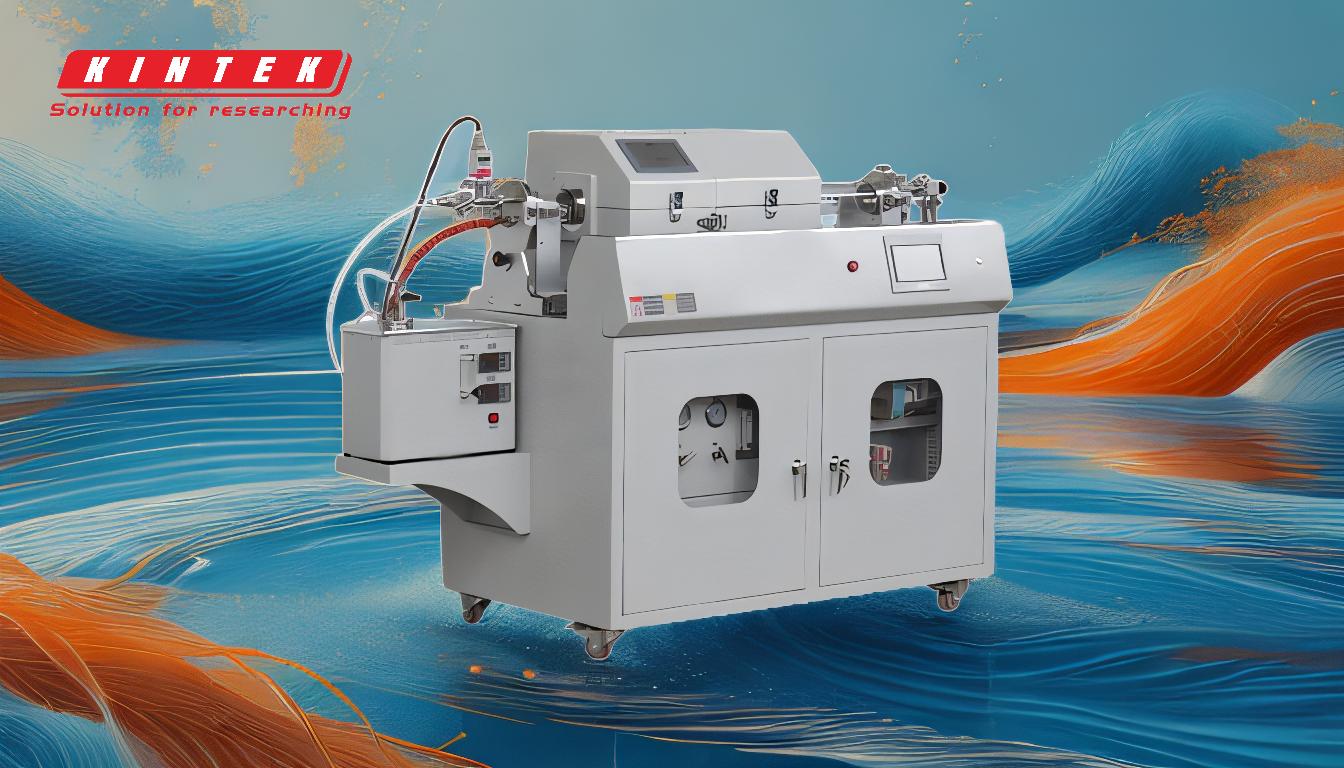
-
Basic Setup of RF Sputtering:
- The process takes place in a vacuum chamber containing the target material, substrate, and RF electrodes.
- An inert gas (e.g., argon, neon, or krypton) is introduced into the chamber to create a plasma environment.
-
Role of RF Power:
- RF power is delivered at a fixed frequency of 13.56 MHz, which is chosen to avoid interference with communication frequencies.
- The alternating electrical potential prevents charge buildup on insulating target materials, a common issue in DC sputtering.
-
Plasma Formation and Ionization:
- The RF power source ionizes the inert gas atoms, creating a plasma of positively charged ions and free electrons.
- The plasma is essential for the sputtering process, as it provides the energetic ions needed to dislodge atoms from the target material.
-
Positive and Negative Cycles:
- Positive Cycle: The target material acts as an anode, attracting electrons and creating a negative bias. This helps to neutralize any positive charge buildup on insulating targets.
- Negative Cycle: The target material acts as a cathode, attracting positively charged ions from the plasma. These ions bombard the target, ejecting atoms that travel to the substrate.
-
Sputtering of Target Material:
- The bombarding ions transfer their energy to the target material, causing atoms to be ejected in a process known as sputtering.
- These ejected atoms form a fine spray that deposits onto the substrate, creating a thin film.
-
Advantages for Insulating Materials:
- RF sputtering is particularly effective for depositing insulating (non-conductive) materials, as the alternating potential prevents charge buildup and arcing.
- This makes RF sputtering a preferred method for applications requiring high-quality thin films of insulating materials.
-
Applications of RF Sputtering:
- RF sputtering is widely used in the semiconductor and electronics industries for depositing thin films of materials such as oxides, nitrides, and other insulators.
- It is also used in the production of optical coatings, solar cells, and magnetic storage media.
-
Process Control and Quality:
- The use of RF power and the alternating potential ensures consistent and high-quality thin films.
- The process can be finely tuned by adjusting parameters such as RF power, gas pressure, and target-substrate distance to achieve the desired film properties.
By understanding these key points, one can appreciate the precision and versatility of RF sputtering, making it an essential technique in modern manufacturing and research.
Summary Table:
Aspect | Details |
---|---|
Process | Thin-film deposition using RF power (13.56 MHz) in a vacuum chamber. |
Key Components | Target material, substrate, RF electrodes, inert gas (e.g., argon). |
Plasma Formation | RF power ionizes inert gas, creating positively charged ions and electrons. |
Positive Cycle | Target attracts electrons, creating a negative bias. |
Negative Cycle | Ions bombard the target, ejecting atoms for thin-film deposition. |
Advantages | Ideal for insulating materials; prevents charge buildup and arcing. |
Applications | Semiconductors, electronics, optical coatings, solar cells, storage media. |
Process Control | Adjust RF power, gas pressure, and target-substrate distance for precision. |
Discover how RF sputtering can elevate your manufacturing process—contact our experts today!