The electric rotary kiln is a highly efficient and environmentally friendly heating furnace used in various industrial processes. It operates by rotating a cylinder (retort) to uniformly heat and stir raw materials, which are fed into the kiln using a feeding device. The kiln is slightly inclined to facilitate the movement of materials during heat treatment. Electric rotary kilns are particularly advantageous as they use electricity for indirect heating, eliminating the need for fossil fuels and enabling the capture and reuse of CO2 emissions. They are customizable in terms of size, heating zones, and materials, making them suitable for applications like sintering, iron ore pelletizing, and proppant production. Key features include precise temperature control, even heat distribution, and airtightness to prevent material contamination.
Key Points Explained:
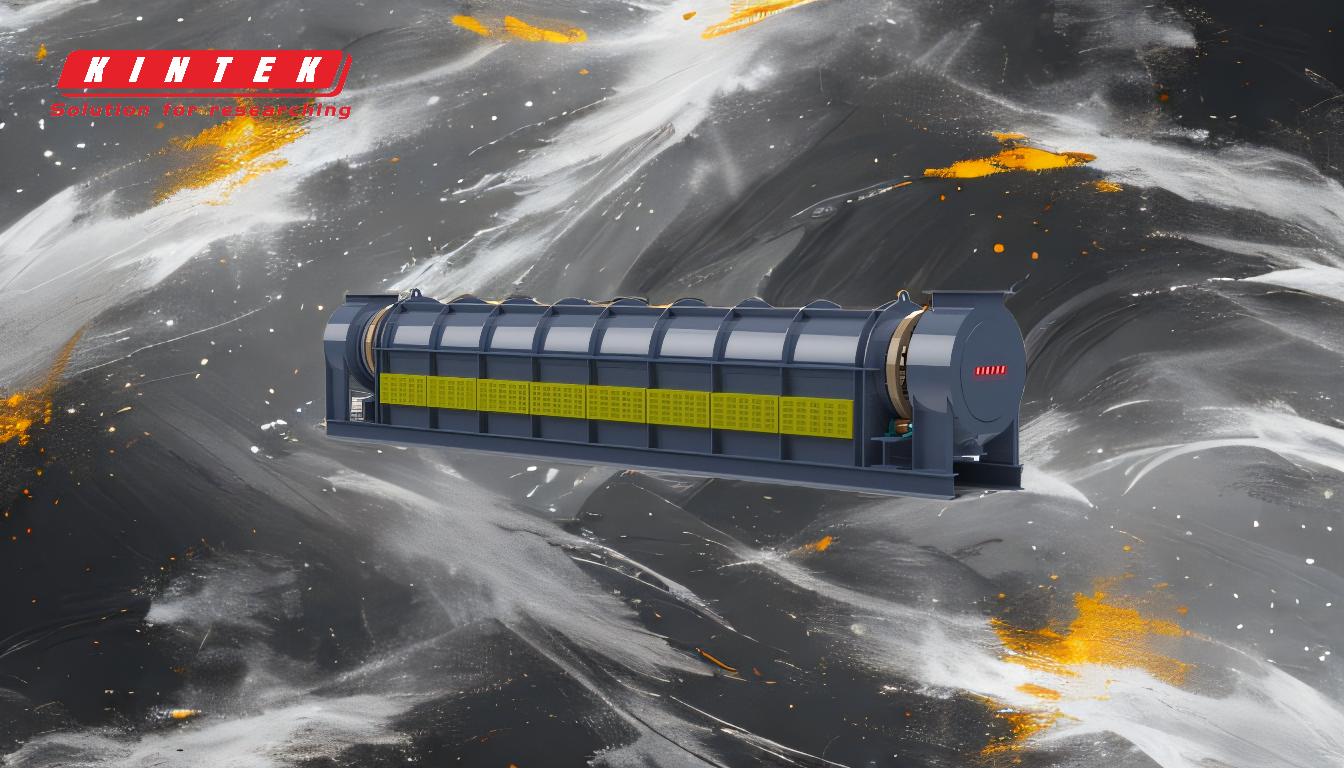
-
Basic Operation of a Rotary Kiln:
- A rotary kiln is a cylindrical furnace that rotates to heat and stir raw materials. It is slightly inclined to allow the material to move through the kiln during the heating process.
- The rotation ensures uniform heating, which is critical for processes like sintering or calcination.
- The feeding system, often a screw feeder, introduces raw materials into the kiln for processing.
-
Electric Rotary Kiln Overview:
- An electric rotary kiln uses electricity as the heating source, making it a cleaner alternative to traditional fossil fuel-based kilns.
- The heating elements are located outside the furnace tube, indirectly heating the materials inside to the required temperature.
- This design allows for precise temperature control and reduces greenhouse gas emissions.
-
Customization and Design:
- The kiln's drum is typically made of nickel-based alloys, capable of withstanding temperatures up to 1100℃.
- The diameter and length of the kiln can be customized based on the material handling capacity and production requirements.
- Multiple independent heating zones can be designed to optimize the thermal profile for specific materials.
-
Sizing and Engineering Considerations:
- Designing a rotary kiln involves thermal and chemical analyses to determine factors like capacity, heat generation, feed rate, retention time, and bed profile.
- These factors influence the kiln's dimensions and ensure it meets the processing goals efficiently.
-
Applications of Rotary Kilns:
- Rotary kilns are widely used in processes like sintering, where materials are heated just below their melting point to increase strength.
- Common applications include iron ore pelletizing and the production of high-strength proppants used in the oil and gas industry.
-
Key Features and Advantages:
- Precise heat patterns can be set to match the firing needs of the product.
- Air cooling mechanisms ensure stable temperature control.
- 360° heater placement provides even heat distribution and high efficiency.
- Customization options, such as suppressing metal contamination and ensuring airtightness, enhance performance and product quality.
-
Construction and Alignment:
- The kiln's construction, position, and alignment are critical for smooth operation.
- A slight inclination with the horizontal axis helps move the solid bed toward the discharge head, ensuring consistent material flow.
-
Environmental Benefits:
- Electric rotary kilns eliminate the need for fossil fuels, reducing carbon emissions.
- The CO2 produced during the process can be captured and reused or sold, adding economic value to the operation.
By combining advanced engineering principles with customizable features, electric rotary kilns offer a versatile and sustainable solution for high-temperature industrial processes. Their ability to provide precise temperature control, even heat distribution, and environmental benefits makes them a preferred choice in modern manufacturing.
Summary Table:
Aspect | Details |
---|---|
Operation | Rotates to uniformly heat and stir materials; slightly inclined for flow. |
Heating Source | Electricity for indirect heating, reducing fossil fuel use. |
Customization | Size, heating zones, and materials tailored to specific industrial needs. |
Applications | Sintering, iron ore pelletizing, proppant production, and more. |
Key Features | Precise temperature control, even heat distribution, airtight design. |
Environmental Benefits | Eliminates fossil fuels, captures CO2 for reuse, reduces emissions. |
Ready to optimize your industrial processes with an electric rotary kiln? Contact us today for expert guidance!