Thermal evaporation deposition is a widely used thin-film deposition technique in which a material is heated to its evaporation point in a high-vacuum environment. The vaporized material then travels through the vacuum and condenses onto a substrate, forming a thin, uniform film. This process relies on thermal energy to evaporate the target material, typically using resistive heating elements such as tungsten boats or coils. The vacuum environment ensures minimal contamination and allows the vaporized particles to travel freely to the substrate without interference. This method is particularly valued for its simplicity, cost-effectiveness, and ability to produce high-purity films.
Key Points Explained:
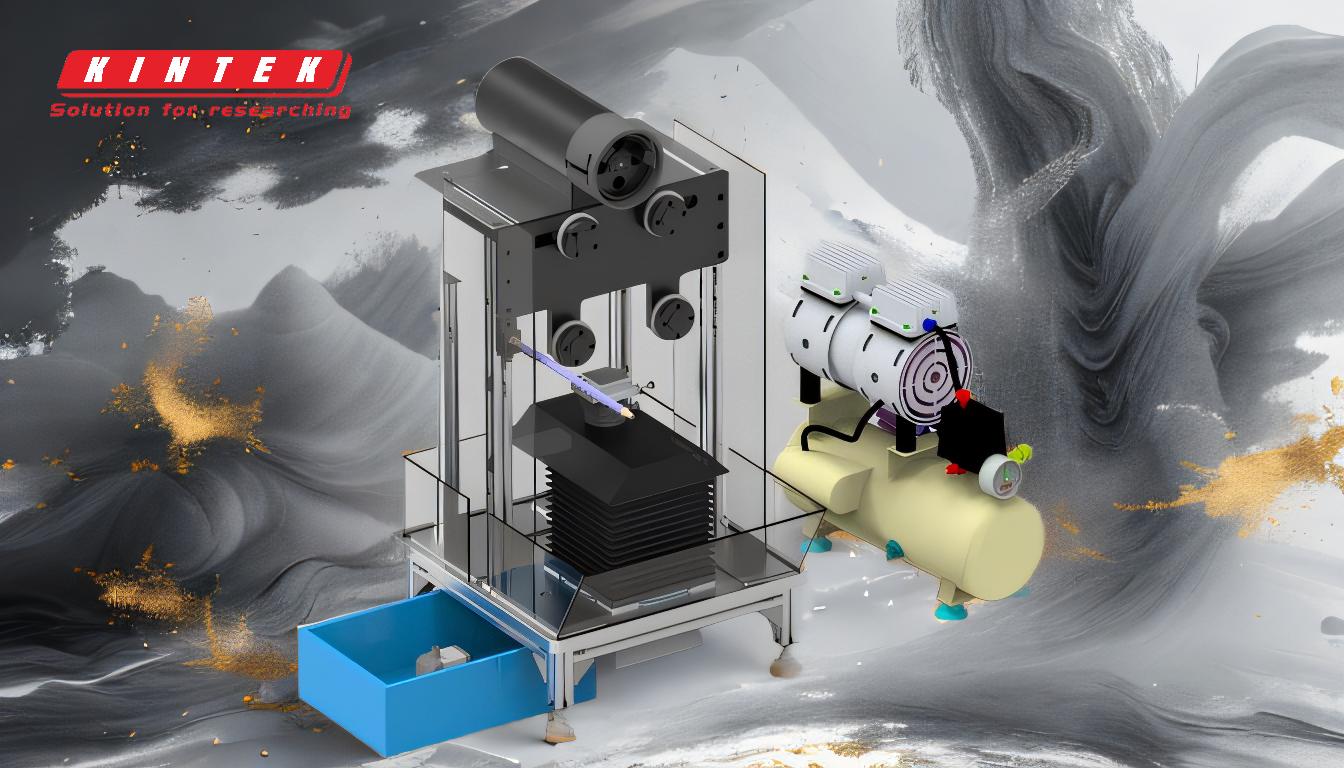
-
Overview of Thermal Evaporation Deposition:
- Thermal evaporation deposition is a physical vapor deposition (PVD) technique used to create thin films on substrates.
- The process involves heating a target material until it evaporates, and the resulting vapor condenses onto a substrate to form a film.
- It is widely used in industries such as electronics, optics, and coatings due to its simplicity and effectiveness.
-
Key Components of the Process:
- Vacuum Chamber: The process takes place in a high-vacuum environment to minimize contamination and ensure a free path for vaporized particles.
- Evaporation Source: The target material is placed in a resistive heating element, such as a tungsten boat, coil, or basket.
- Heating Mechanism: Electric current is passed through the heating element, generating thermal energy that heats the material to its evaporation point.
- Substrate: The surface onto which the vaporized material condenses to form a thin film.
-
Step-by-Step Process:
-
Step 1: Preparation:
- The target material is loaded into the evaporation source (e.g., a tungsten boat or coil).
- The substrate is cleaned and positioned above the evaporation source inside the vacuum chamber.
-
Step 2: Evacuation:
- The vacuum pump removes air and other gases from the chamber, creating a high-vacuum environment.
-
Step 3: Heating:
- Electric current is applied to the heating element, causing it to heat up and transfer thermal energy to the target material.
- The material is heated to its melting point and then to its evaporation point, where it transitions from a solid to a vapor.
-
Step 4: Vaporization and Deposition:
- The vaporized material forms a vapor cloud inside the chamber.
- The vapor particles travel through the vacuum and condense onto the substrate, forming a thin film.
-
Step 5: Cooling and Removal:
- After deposition, the substrate is allowed to cool, and the vacuum chamber is vented to remove the coated substrate.
-
Step 1: Preparation:
-
Advantages of Thermal Evaporation Deposition:
- High Purity: The vacuum environment minimizes contamination, resulting in high-purity films.
- Simplicity: The process is straightforward and does not require complex equipment.
- Cost-Effectiveness: It is relatively inexpensive compared to other thin-film deposition techniques.
- Versatility: It can be used with a wide range of materials, including metals, alloys, and some compounds.
-
Limitations of Thermal Evaporation Deposition:
- Material Limitations: Some materials, such as refractory metals and ceramics, are difficult to evaporate due to their high melting points.
- Uniformity: Achieving uniform film thickness can be challenging, especially for large or complex substrates.
- Adhesion: The adhesion of the deposited film to the substrate may be weaker compared to other deposition methods.
-
Applications of Thermal Evaporation Deposition:
- Electronics: Used to deposit conductive layers, such as aluminum or gold, in semiconductor devices.
- Optics: Applied in the production of reflective coatings, anti-reflective coatings, and optical filters.
- Coatings: Used for decorative and protective coatings on various materials, including plastics and metals.
-
Comparison with Other Deposition Techniques:
- Thermal Evaporation vs. Sputtering: Thermal evaporation is simpler and more cost-effective but may struggle with high-melting-point materials, whereas sputtering can handle a wider range of materials but is more complex and expensive.
- Thermal Evaporation vs. Chemical Vapor Deposition (CVD): Thermal evaporation is a physical process, while CVD involves chemical reactions. CVD can produce more complex films but requires higher temperatures and more complex equipment.
By understanding the process, components, advantages, and limitations of thermal evaporation deposition, purchasers of equipment and consumables can make informed decisions about its suitability for their specific applications.
Summary Table:
Aspect | Details |
---|---|
Process Overview | Heats material to evaporation point in a vacuum, forming thin films. |
Key Components | Vacuum chamber, evaporation source (e.g., tungsten boat), heating mechanism. |
Advantages | High purity, simplicity, cost-effectiveness, and versatility. |
Limitations | Material limitations, uniformity challenges, weaker adhesion. |
Applications | Electronics (conductive layers), optics (coatings), decorative/protective films. |
Comparison | Simpler and cheaper than sputtering and CVD, but limited for high-melting-point materials. |
Discover how thermal evaporation deposition can enhance your projects—contact our experts today!