Thin film deposition in semiconductors is a critical process for creating layers of semiconductor material on a substrate, which are essential for manufacturing devices like integrated circuits, transistors, solar cells, and LEDs. The process involves selecting a material source, transporting it to a substrate, depositing it to form a thin layer, and optionally annealing or treating the film to achieve desired properties. Various deposition techniques, such as chemical vapor deposition (CVD), physical vapor deposition (PVD), spin coating, and sputtering, are employed to control the thickness and composition of the films. These methods allow for precise fabrication of thin films, enabling the miniaturization and functionality of semiconductor components.
Key Points Explained:
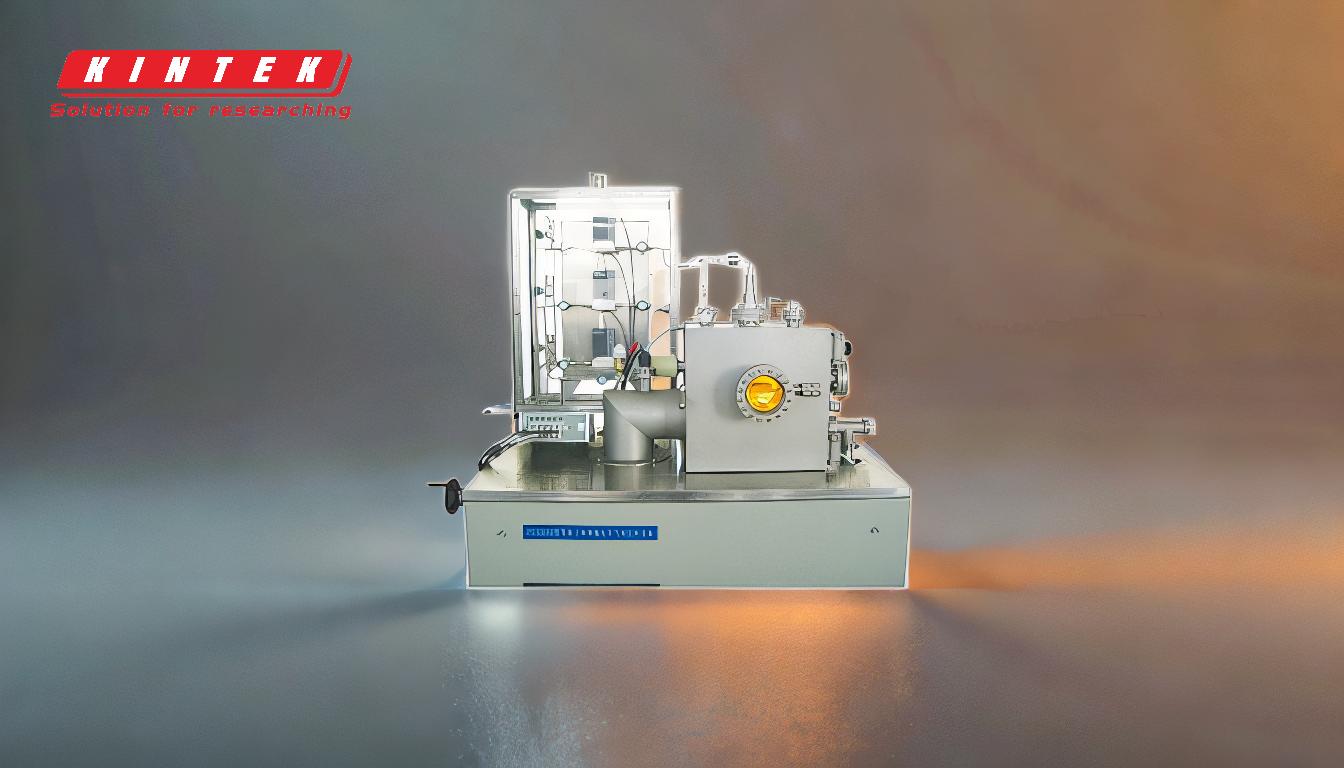
-
Definition and Importance of Thin Films in Semiconductors:
- Thin films are layers of semiconductor material deposited on a substrate, typically ranging from nanometers to microns in thickness.
- They are crucial for manufacturing semiconductor devices like integrated circuits, transistors, solar cells, and LEDs.
- Thin films enable the miniaturization of components such as BJTs, FETs, MOSFETs, and diodes.
-
Deposition Techniques:
- Chemical Vapor Deposition (CVD): A process where chemical reactions are used to deposit a thin film on a substrate. It allows for precise control over film composition and thickness.
- Physical Vapor Deposition (PVD): Involves the physical transfer of material from a source to a substrate, often using techniques like sputtering or evaporation.
- Spin Coating: A method where a liquid precursor is spread on a substrate by spinning it at high speeds, resulting in a uniform thin film.
- Sputtering: A PVD technique where atoms are ejected from a solid target material due to bombardment by energetic ions, which then deposit onto a substrate.
-
Process Steps in Thin Film Deposition:
- Selection of Material Source: Choosing a pure material (target) that will form the thin film.
- Transportation to Substrate: Moving the material from the source to the substrate, often through a vacuum or fluid medium.
- Deposition: The actual process of forming the thin film on the substrate, which can involve evaporation, sputtering, or chemical reactions.
- Annealing or Heat Treatment: Optional step to improve the film's properties by heating it to a specific temperature.
- Analysis and Modification: Evaluating the film's properties and adjusting the deposition process if necessary to achieve desired characteristics.
-
Applications of Thin Films in Semiconductors:
- Integrated Circuits: Thin films are used to create the various layers of an integrated circuit, including insulating and conductive layers.
- Transistors: Thin films form the active regions of transistors, such as the gate oxide in MOSFETs.
- Solar Cells: Thin films are used to create the light-absorbing layers in photovoltaic cells.
- LEDs: Thin films are essential for the fabrication of light-emitting diodes, particularly in the formation of the active semiconductor layers.
-
Advantages of Thin Film Deposition:
- Precision: Thin film deposition techniques allow for precise control over the thickness, composition, and uniformity of the films.
- Miniaturization: Enables the creation of smaller and more efficient semiconductor devices.
- Versatility: Can be used to deposit a wide range of materials, including metals, semiconductors, and insulators.
-
Challenges and Considerations:
- Uniformity: Achieving a uniform film thickness across the entire substrate can be challenging, especially for large areas.
- Adhesion: Ensuring that the thin film adheres well to the substrate is crucial for the durability and performance of the device.
- Contamination: Preventing contamination during the deposition process is essential to maintain the purity and performance of the thin film.
In summary, the process of thin film deposition in semiconductors is a sophisticated and multi-step procedure that is fundamental to the production of modern electronic devices. By carefully selecting the deposition technique and controlling the process parameters, manufacturers can create thin films with the precise properties needed for a wide range of applications.
Summary Table:
Aspect | Details |
---|---|
Definition | Layers of semiconductor material (nanometers to microns thick) deposited on a substrate. |
Importance | Essential for manufacturing integrated circuits, transistors, solar cells, and LEDs. |
Deposition Techniques | CVD, PVD, spin coating, sputtering. |
Process Steps | Material selection, transportation, deposition, annealing, analysis. |
Applications | Integrated circuits, transistors, solar cells, LEDs. |
Advantages | Precision, miniaturization, versatility. |
Challenges | Uniformity, adhesion, contamination. |
Discover how thin film deposition can revolutionize your semiconductor projects—contact our experts today!