Pulsed DC sputtering is a specialized thin-film deposition technique that combines the principles of direct current (DC) sputtering with pulsed power delivery. Unlike traditional DC sputtering, which applies a continuous voltage, pulsed DC sputtering uses short, high-voltage pulses to bombard the target material. This method is particularly effective for depositing insulating or dielectric materials, as it prevents charge buildup on the target surface, which can otherwise disrupt the sputtering process. The technique operates at frequencies typically ranging from 40 to 200 kHz, ensuring efficient target cleaning and improved deposition quality. Pulsed DC sputtering is widely used in applications requiring high-quality, uniform coatings, such as in the semiconductor, optics, and display industries.
Key Points Explained:
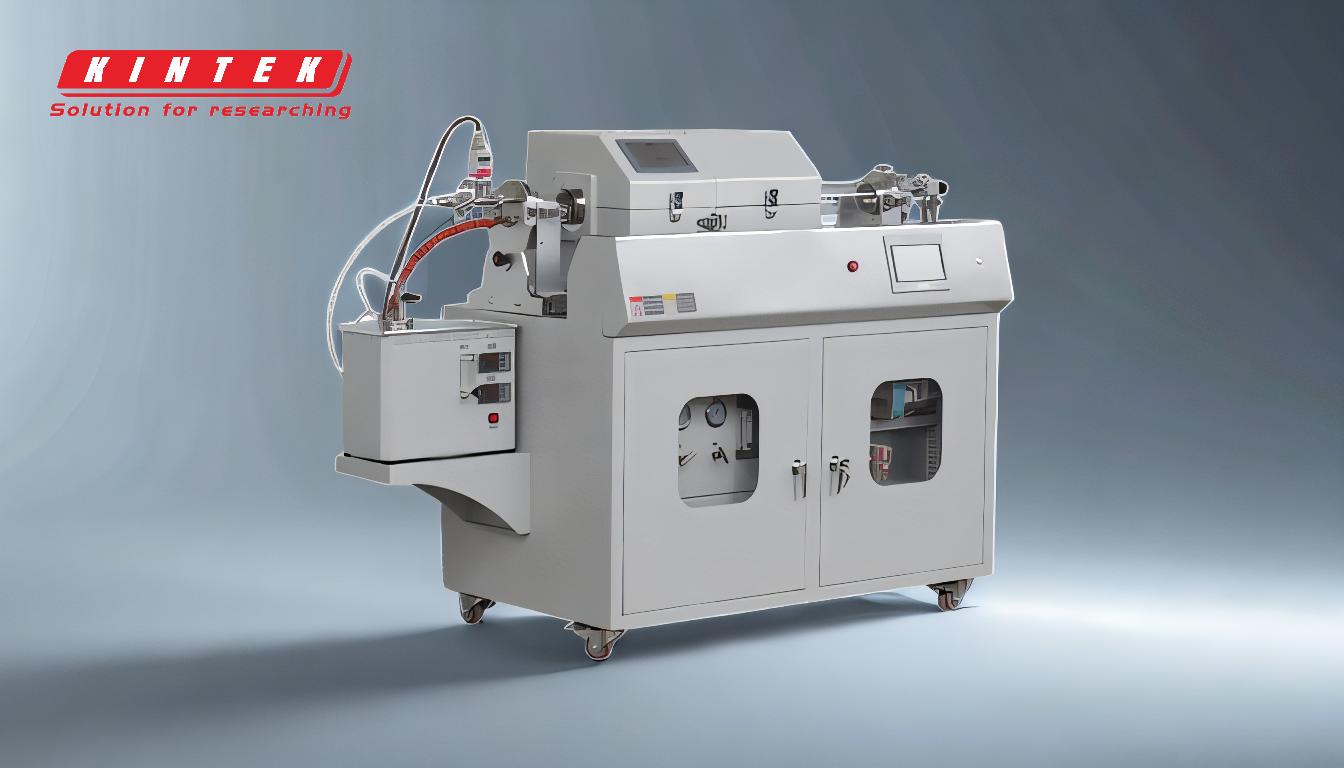
-
Definition and Mechanism of Pulsed DC Sputtering:
- Pulsed DC sputtering is a variant of DC sputtering where the power supply delivers high-voltage pulses instead of a continuous DC voltage.
- The pulses are short and powerful, typically operating at frequencies between 40 and 200 kHz.
- These pulses bombard the target material, causing atoms to be ejected and deposited onto the substrate.
-
Advantages Over Traditional DC Sputtering:
- Prevention of Charge Buildup: Pulsed DC sputtering is particularly effective for insulating or dielectric materials. The pulsed voltage prevents the accumulation of a dielectric charge on the target surface, which can otherwise lead to arcing and process instability.
- Improved Deposition Quality: The high-energy pulses ensure better target cleaning, leading to more uniform and high-quality thin films.
- Enhanced Process Control: The ability to control pulse frequency and duration allows for fine-tuning of the deposition process, making it suitable for a wide range of materials and applications.
-
Applications of Pulsed DC Sputtering:
- Semiconductor Industry: Used for depositing thin films of insulating materials in semiconductor devices.
- Optics: Ideal for creating high-quality optical coatings, such as anti-reflective and protective layers.
- Display Technology: Employed in the production of flat-panel displays, where uniform and defect-free coatings are crucial.
- Decorative Coatings: Used to apply durable and aesthetically pleasing coatings on various consumer products.
-
Operational Parameters:
- Frequency Range: Typically operates between 40 and 200 kHz. The exact frequency can be adjusted based on the material being sputtered and the desired film properties.
- Pulse Duration: The duration of each pulse is carefully controlled to ensure efficient sputtering without damaging the target material.
- Power Density: The power density of the pulses is higher than in continuous DC sputtering, leading to more efficient sputtering and faster deposition rates.
-
Comparison with Other Sputtering Techniques:
- DC Sputtering: Continuous DC voltage can lead to charge buildup on insulating targets, causing arcing and process instability. Pulsed DC sputtering overcomes this limitation.
- RF Sputtering: While RF sputtering is also effective for insulating materials, it operates at much higher frequencies (typically 13.56 MHz) and requires more complex equipment. Pulsed DC sputtering offers a simpler and more cost-effective alternative for many applications.
- Magnetron Sputtering: Magnetron sputtering uses magnetic fields to enhance the sputtering process, but it can still suffer from charge buildup on insulating targets. Pulsed DC sputtering can be combined with magnetron techniques to further improve performance.
-
Challenges and Considerations:
- Target Material: The choice of target material is critical, as not all materials respond well to pulsed DC sputtering. Insulating and dielectric materials are particularly well-suited.
- Equipment Complexity: While simpler than RF sputtering, pulsed DC sputtering still requires specialized power supplies and control systems to manage the pulsed power delivery.
- Process Optimization: Achieving the desired film properties may require careful optimization of pulse frequency, duration, and power density.
In summary, pulsed DC sputtering is a versatile and effective technique for depositing high-quality thin films, particularly for insulating and dielectric materials. Its ability to prevent charge buildup and provide precise control over the deposition process makes it a valuable tool in various high-tech industries.
Summary Table:
Aspect | Details |
---|---|
Definition | A DC sputtering variant using high-voltage pulses for thin-film deposition. |
Frequency Range | 40–200 kHz |
Key Advantages | Prevents charge buildup, improves deposition quality, and enhances control. |
Applications | Semiconductors, optics, displays, and decorative coatings. |
Comparison | Overcomes limitations of DC and RF sputtering. |
Challenges | Requires specialized equipment and process optimization. |
Discover how pulsed DC sputtering can elevate your thin-film processes—contact our experts today!