Heat treatment of aluminum serves several critical purposes in metal production and manufacturing. It is a controlled process that involves heating and cooling aluminum to alter its physical and mechanical properties, making it more suitable for specific applications. The primary goals of heat treatment include improving strength, ductility, hardness, and temperature resistance, while also ensuring a balance between cost and quality. This process is particularly important in industries such as aerospace and automotive, where aluminum components must withstand extreme conditions and stresses. By carefully managing the heating and cooling cycles, manufacturers can tailor the material's properties to meet precise performance requirements, enhancing the overall durability and functionality of the final product.
Key Points Explained:
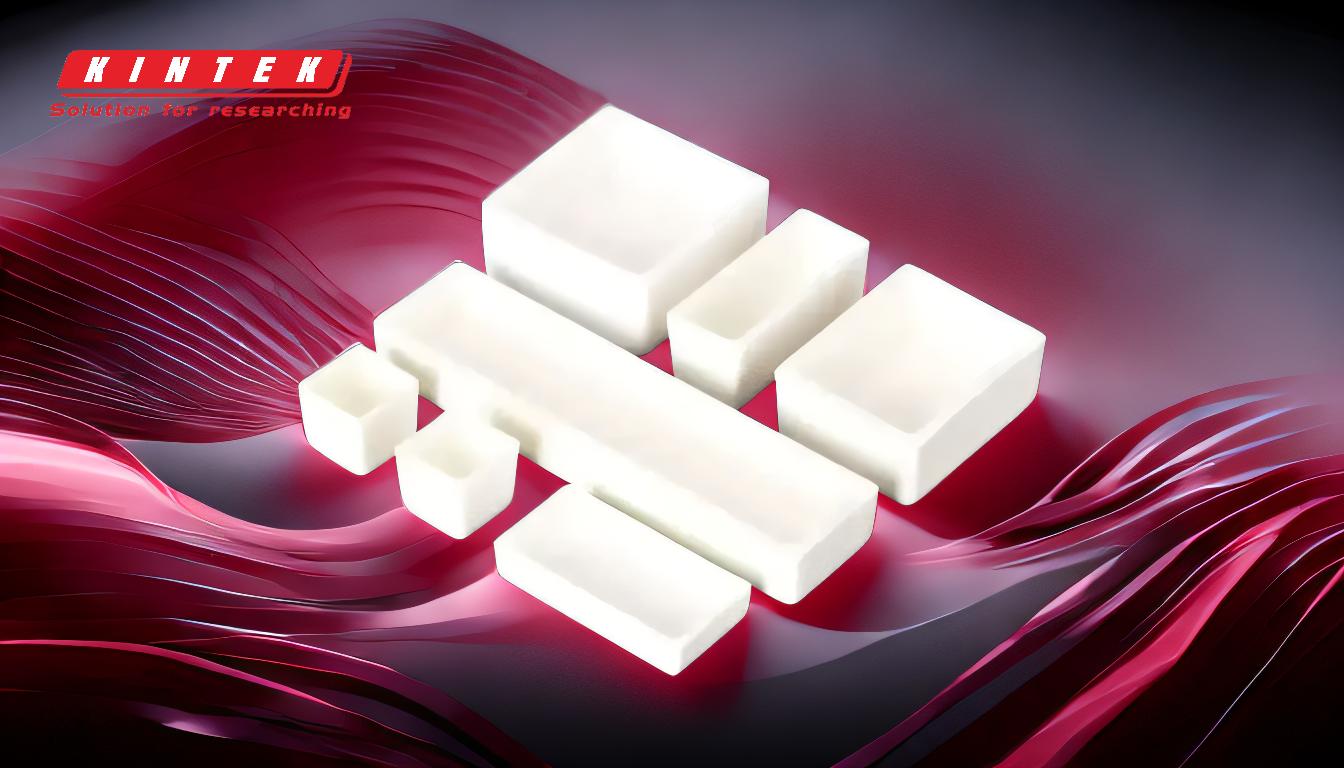
-
Alteration of Material Structure:
- Heat treatment involves controlled heating and cooling processes that modify the internal structure of aluminum. This can lead to changes in grain size and distribution, which directly impact the material's mechanical properties.
- By altering the microstructure, heat treatment can enhance the aluminum's strength, making it more resistant to deformation under stress.
-
Improvement of Physical Properties:
- Strength: Heat treatment can significantly increase the tensile strength of aluminum, making it suitable for load-bearing applications.
- Ductility: The process can also improve ductility, allowing the material to be shaped or stretched without breaking, which is crucial for forming complex parts.
- Hardness: Enhanced surface hardness can be achieved, providing better wear resistance and longevity.
- Temperature Resistance: Heat-treated aluminum can better withstand high temperatures, which is essential for components used in high-heat environments like engines or exhaust systems.
-
Application in Industry:
- Aerospace: Aluminum components in aircraft must endure extreme conditions, including high stress and temperature variations. Heat treatment ensures these parts maintain their integrity and performance.
- Automotive: In the automotive industry, heat-treated aluminum is used for parts such as engine blocks, pistons, and suspension components, where strength and durability are paramount.
- Batch Production: For manufacturers producing metal parts in large quantities, heat treatment provides a consistent method to achieve uniform properties across all components, ensuring reliability and quality.
-
Cost-Quality Balance:
- Heat treatment offers a cost-effective way to enhance the properties of aluminum without the need for expensive alloying elements. By optimizing the heat treatment process, manufacturers can achieve high-quality results while keeping production costs manageable.
- The process also reduces the need for additional machining or finishing steps, further contributing to cost savings.
-
Versatility Across Metals:
- While the focus here is on aluminum, it's worth noting that heat treatment is applicable to a wide range of metals, both ferrous and non-ferrous. This versatility makes it a valuable process in various industrial sectors, allowing for the customization of material properties to meet specific application requirements.
In summary, the heat treatment of aluminum is a vital process that enhances the material's mechanical and physical properties, making it more suitable for demanding applications in industries such as aerospace and automotive. By carefully controlling the heating and cooling cycles, manufacturers can achieve a balance between cost and quality, ensuring that aluminum components perform reliably under extreme conditions.
Summary Table:
Purpose | Benefits |
---|---|
Alter Material Structure | Enhances strength, ductility, and hardness by modifying internal structure. |
Improve Physical Properties | Increases tensile strength, wear resistance, and temperature tolerance. |
Industry Applications | Aerospace, automotive, and batch production for reliable, high-quality parts. |
Cost-Quality Balance | Cost-effective method to achieve superior material properties. |
Versatility | Applicable to various metals for customized performance needs. |
Learn how heat treatment can optimize your aluminum components—contact our experts today!