Sintering in powder metallurgy is a critical heat treatment process that transforms compacted metal powders into dense, strong, and functional components. By heating the "green" compacted parts at temperatures below the melting point of the primary metal, sintering bonds the particles together, reduces porosity, and enhances mechanical properties. This process ensures the final product achieves the desired strength, dimensional accuracy, and structural integrity. Sintering is widely used in industries to produce components like gears, bearings, and electrical contacts, offering a cost-effective and efficient manufacturing method for complex parts.
Key Points Explained:
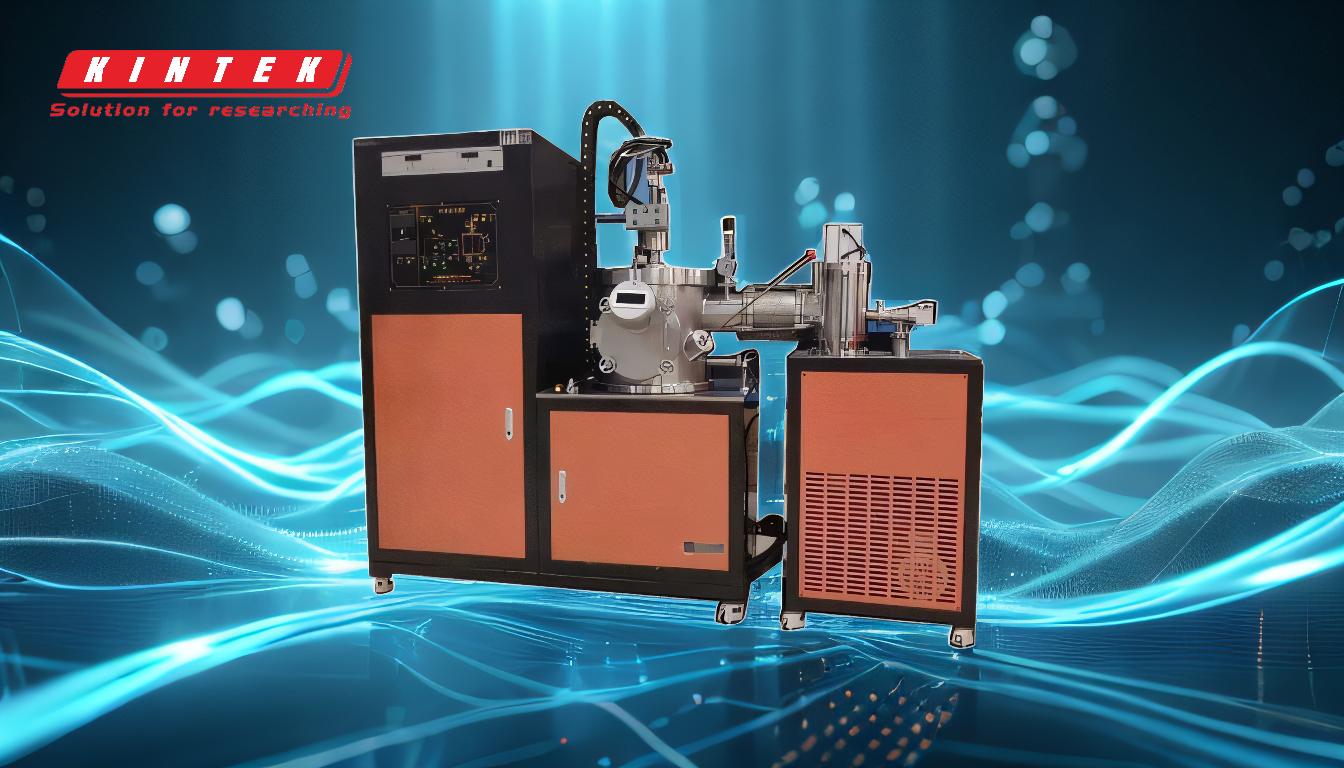
-
Definition and Purpose of Sintering
- Sintering is a heat treatment process in powder metallurgy that bonds metal powder particles into a cohesive, dense structure without melting the material.
- The primary purpose is to enhance the mechanical properties, such as strength and durability, while reducing porosity and achieving final dimensions.
- It transforms the "green" compact (a loosely bonded powder structure) into a solid, functional part suitable for end-use applications.
-
How Sintering Works
- The process involves heating the green compact in a controlled atmosphere furnace at temperatures slightly below the melting point of the primary metal.
- During sintering, the particles bond through diffusion, which eliminates pores and increases density.
- The controlled cooling rate after sintering further fine-tunes the material's properties, such as hardness and toughness.
-
Key Benefits of Sintering
- Improved Mechanical Properties: Sintering significantly enhances the strength, wear resistance, and structural integrity of the material.
- Dimensional Accuracy: The process accounts for minor shrinkage, ensuring the final part meets precise dimensional requirements.
- Cost-Effectiveness: Sintering is a versatile and efficient method for producing complex shapes and components, reducing material waste and machining costs.
- Versatility: It is applicable to a wide range of materials, including metals, ceramics, and composites, making it suitable for various industries.
-
Applications of Sintered Parts
- Sintering is used to manufacture components like gears, bearings, pulleys, rotors, sprockets, and electrical contacts.
- It is particularly valuable in industries requiring high-performance parts, such as automotive, aerospace, and electronics.
- The ability to produce near-net-shape components reduces the need for additional machining, saving time and resources.
-
Process Parameters and Control
- Temperature: Sintering temperatures are carefully controlled to remain below the melting point of the primary metal, ensuring bonding without liquefaction.
- Atmosphere: The furnace atmosphere (e.g., hydrogen, nitrogen, or vacuum) is controlled to prevent oxidation and ensure proper particle bonding.
- Cooling Rate: Adjusting the cooling rate allows manufacturers to tailor the material's microstructure and mechanical properties.
-
Comparison to Other Manufacturing Processes
- Unlike casting or forging, sintering does not involve melting the metal, which reduces energy consumption and minimizes material waste.
- It allows for the production of complex geometries that are difficult to achieve with traditional methods.
- Sintering is particularly advantageous for materials with high melting points, as it avoids the challenges associated with melting and solidification.
-
Role in Powder Metallurgy
- Sintering is the final and most critical step in powder metallurgy, transforming the compacted powder into a functional part.
- It ensures the part achieves the required physical and mechanical properties, such as density, hardness, and strength.
- Without sintering, the green compact would lack the necessary structural integrity and performance characteristics for real-world applications.
In summary, sintering is a fundamental process in powder metallurgy that enables the production of high-quality, durable, and precise components. By bonding metal particles at high temperatures, it enhances material properties, reduces porosity, and ensures dimensional accuracy, making it indispensable in modern manufacturing.
Summary Table:
Aspect | Details |
---|---|
Purpose | Bonds metal particles, reduces porosity, enhances mechanical properties. |
Process | Heating below melting point, controlled atmosphere, diffusion bonding. |
Benefits | Improved strength, wear resistance, cost-effectiveness, versatility. |
Applications | Gears, bearings, electrical contacts, automotive, aerospace, electronics. |
Key Parameters | Temperature, atmosphere, cooling rate. |
Role in Manufacturing | Final step in powder metallurgy, ensures structural integrity and precision. |
Discover how sintering can optimize your manufacturing process—contact our experts today!