The PVD (Physical Vapor Deposition) color process is a vacuum-based coating technology used to apply thin, durable, and vibrant colored layers onto substrates. This process involves transforming a solid material into a vapor state, which then condenses onto a substrate to form a thin film. The color is achieved by introducing reactive gases during the process, which chemically react with the vaporized material to create compounds with specific optical properties. PVD coatings are known for their durability, resistance to wear, and ability to produce a wide range of colors, making them popular in industries such as automotive, jewelry, and consumer electronics. The process is performed under high-vacuum conditions, ensuring high-quality, uniform coatings.
Key Points Explained:
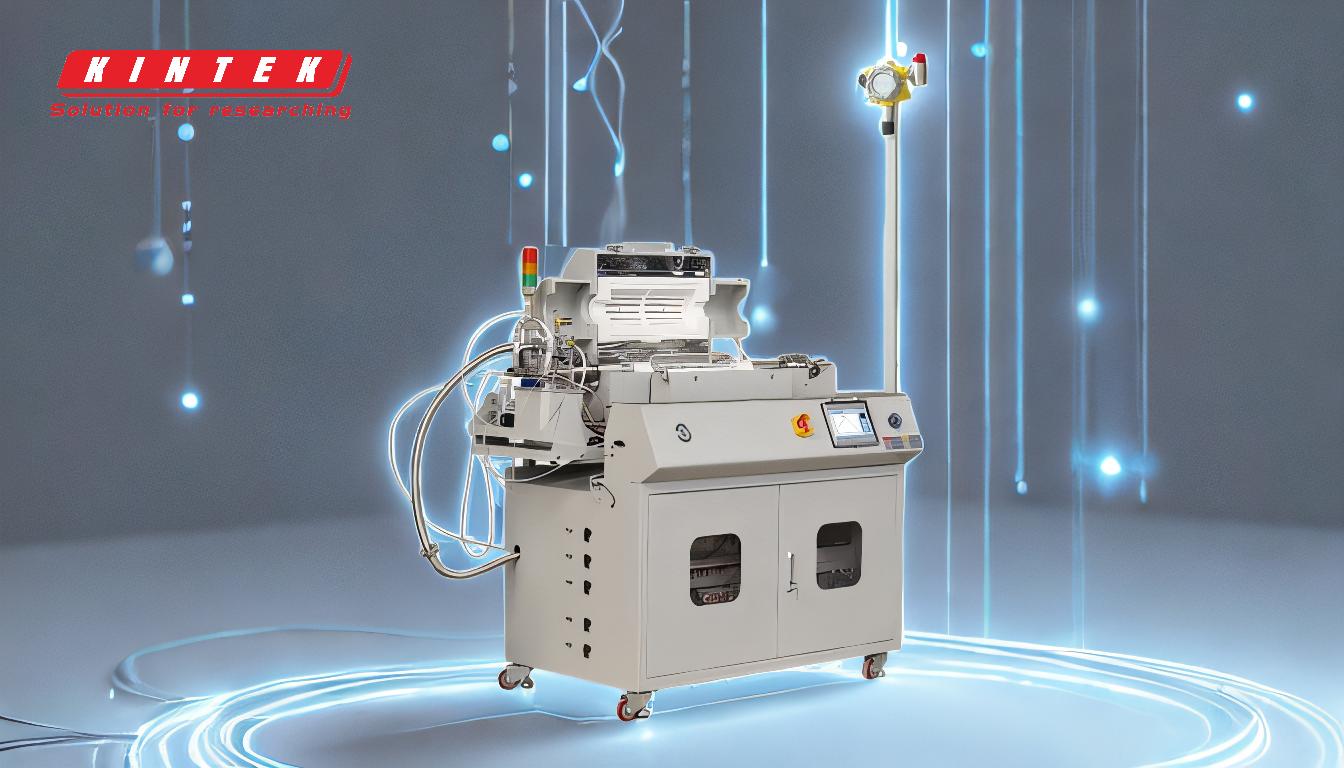
-
Overview of the PVD Process:
- PVD is a vacuum-based coating process where a solid material is vaporized and then deposited onto a substrate to form a thin film.
- The process is performed under high-vacuum conditions, ensuring a clean and controlled environment for the deposition.
- PVD is widely used for decorative and functional coatings due to its ability to produce durable, wear-resistant, and aesthetically pleasing finishes.
-
Steps Involved in the PVD Color Process:
- Vaporization: The solid material (target) is vaporized using methods such as sputtering, evaporation, or laser ablation. This step involves converting the solid into a vapor state, often by exciting the material with plasma or high-energy sources.
- Introduction of Reactive Gas: A reactive gas (e.g., nitrogen, oxygen, or acetylene) is introduced into the chamber. This gas chemically reacts with the vaporized material to form compounds with specific optical properties, which determine the color of the coating.
- Transportation: The vaporized material and reactive gas are transported through the vacuum chamber to the substrate. This step ensures uniform distribution of the vapor and gas mixture.
- Deposition: The vaporized material and reactive gas condense onto the substrate, forming a thin, colored film. The deposition process occurs at relatively low temperatures, making it suitable for a wide range of materials, including plastics and metals.
-
Color Formation in PVD:
- The color of the PVD coating is determined by the chemical composition of the deposited material and the reactive gas used.
- For example, titanium nitride (TiN) produces a gold-colored coating, while titanium aluminum nitride (TiAlN) can produce a range of colors, including blue, purple, and bronze.
- The thickness of the coating and the angle of deposition can also influence the final color, allowing for a wide range of hues and effects.
-
Advantages of PVD Coatings:
- Durability: PVD coatings are highly resistant to wear, corrosion, and scratching, making them ideal for applications requiring long-lasting finishes.
- Aesthetic Appeal: The process can produce a wide range of colors and finishes, from metallic to matte, enhancing the visual appeal of products.
- Environmental Friendliness: PVD is a clean process that produces minimal waste and does not involve harmful chemicals, making it environmentally friendly.
- Versatility: PVD can be applied to a variety of substrates, including metals, plastics, and ceramics, making it suitable for diverse industries.
-
Applications of PVD Color Coatings:
- Automotive Industry: PVD coatings are used for decorative trims, emblems, and functional components such as piston rings and engine parts.
- Jewelry: The process is used to create durable, scratch-resistant coatings on watches, rings, and other accessories.
- Consumer Electronics: PVD coatings are applied to smartphones, laptops, and other devices to enhance their appearance and durability.
- Architectural Applications: PVD is used for coating door handles, faucets, and other fixtures to provide both aesthetic and functional benefits.
-
Comparison with Other Coating Processes:
- CVD (Chemical Vapor Deposition): Unlike PVD, CVD involves chemical reactions at the substrate surface, often requiring higher temperatures. PVD is preferred for applications requiring lower temperatures and more precise control over the coating properties.
- Electroplating: PVD coatings are generally more durable and environmentally friendly compared to electroplating, which often involves toxic chemicals and produces more waste.
-
Challenges and Considerations:
- Cost: The PVD process can be more expensive than traditional coating methods due to the need for specialized equipment and high-vacuum conditions.
- Complexity: Achieving consistent color and finish requires precise control over process parameters, such as gas flow, pressure, and temperature.
- Substrate Compatibility: While PVD can be applied to a wide range of materials, some substrates may require pre-treatment to ensure proper adhesion of the coating.
By understanding the PVD color process, purchasers can make informed decisions about its suitability for their specific applications, balancing factors such as cost, durability, and aesthetic requirements.
Summary Table:
Aspect | Details |
---|---|
Process Overview | Vacuum-based coating technology for thin, durable, and vibrant colored layers. |
Key Steps | Vaporization, reactive gas introduction, transportation, and deposition. |
Color Formation | Determined by chemical composition, reactive gas, and deposition angle. |
Advantages | Durability, aesthetic appeal, environmental friendliness, and versatility. |
Applications | Automotive, jewelry, consumer electronics, and architectural uses. |
Comparison with CVD | PVD is preferred for lower temperatures and precise control. |
Challenges | Higher cost, process complexity, and substrate compatibility considerations. |
Ready to enhance your products with durable, vibrant PVD coatings? Contact us today to learn more!