The PVD (Physical Vapor Deposition) process in semiconductors is a vacuum-based thin-film deposition technique used to create highly precise and uniform coatings on substrates. It involves the vaporization of a solid material into a gaseous state, followed by the transportation and condensation of these vaporized particles onto a substrate to form a thin film. The process is performed under high-vacuum conditions and typically involves steps such as vaporization, migration, and deposition. PVD is widely used in semiconductor manufacturing due to its ability to produce high-quality, durable, and uniform coatings essential for device performance.
Key Points Explained:
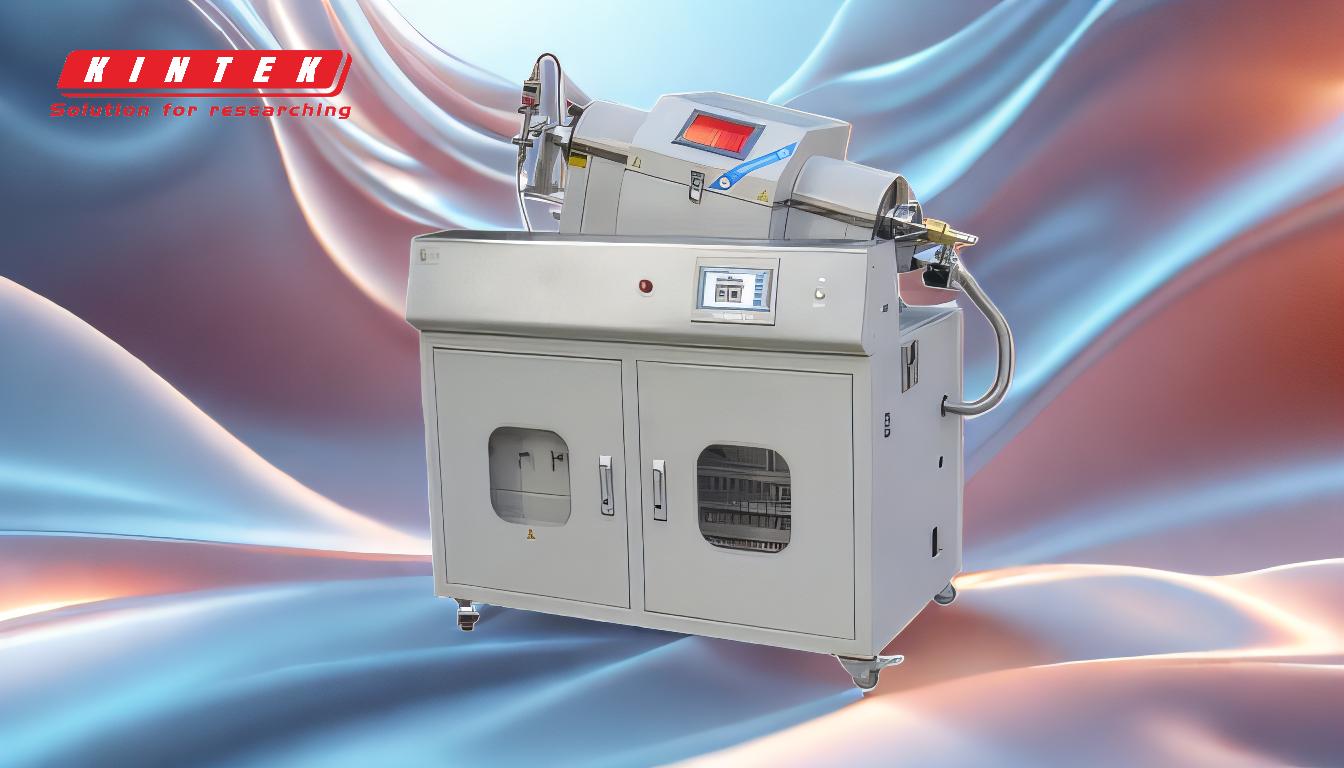
-
Overview of PVD in Semiconductors:
- PVD is a critical process in semiconductor fabrication, used to deposit thin films of materials such as metals, alloys, and compounds onto substrates.
- It is performed under high-vacuum conditions to ensure minimal contamination and precise control over the deposition process.
- The resulting thin films are essential for creating conductive, insulating, or protective layers in semiconductor devices.
-
Key Steps in the PVD Process:
-
Vaporization of Coating Material:
- The solid material (target) is vaporized through methods like evaporation, sputtering, or laser ablation.
- High-energy sources such as plasma, electricity, or lasers are used to excite the target material, converting it into a vapor or plasma state.
-
Transportation of Vaporized Particles:
- The vaporized atoms or molecules are transported through the vacuum chamber to the substrate.
- During transportation, the particles may undergo collisions or reactions with other gases introduced into the chamber.
-
Deposition onto Substrate:
- The vaporized particles condense onto the substrate, forming a thin, uniform layer.
- The substrate is typically maintained at a lower temperature to facilitate condensation and layer formation.
-
Vaporization of Coating Material:
-
Methods of PVD:
-
Evaporation:
- The target material is heated until it evaporates, and the vapor is deposited onto the substrate.
- Commonly used for depositing metals like aluminum or gold.
-
Sputtering:
- A high-energy plasma bombards the target material, dislodging atoms that are then deposited onto the substrate.
- Suitable for depositing a wide range of materials, including alloys and compounds.
-
Laser Ablation:
- A high-power laser is used to vaporize the target material, which is then deposited onto the substrate.
- Often used for materials that are difficult to evaporate or sputter.
-
Evaporation:
-
Applications in Semiconductor Manufacturing:
-
Conductive Layers:
- PVD is used to deposit metals like copper, aluminum, and tungsten for interconnects and electrodes.
-
Barrier Layers:
- Thin films of materials like titanium nitride (TiN) are deposited to prevent diffusion between layers.
-
Protective Coatings:
- PVD is used to create durable, corrosion-resistant coatings on semiconductor devices.
-
Conductive Layers:
-
Advantages of PVD:
-
High Precision and Uniformity:
- PVD allows for the deposition of extremely thin and uniform layers, essential for advanced semiconductor devices.
-
Material Versatility:
- A wide range of materials, including metals, alloys, and compounds, can be deposited using PVD.
-
Low-Temperature Process:
- PVD is performed at relatively low temperatures, reducing the risk of thermal damage to the substrate.
-
High Precision and Uniformity:
-
Challenges and Considerations:
-
High-Vacuum Requirements:
- Maintaining a high vacuum is essential for the PVD process, which can be costly and technically challenging.
-
Complexity of Equipment:
- PVD systems require sophisticated equipment for plasma generation, vacuum control, and substrate handling.
-
Limited Deposition Rates:
- Compared to other deposition methods, PVD can have slower deposition rates, impacting throughput.
-
High-Vacuum Requirements:
By understanding the PVD process and its role in semiconductor manufacturing, equipment and consumable purchasers can better evaluate the requirements for PVD systems, including vacuum pumps, target materials, and deposition chambers, to ensure optimal performance and cost-effectiveness.
Summary Table:
Aspect | Details |
---|---|
Overview | Vacuum-based thin-film deposition for semiconductors. |
Key Steps | Vaporization, transportation, and deposition of materials. |
Methods | Evaporation, sputtering, and laser ablation. |
Applications | Conductive layers, barrier layers, and protective coatings. |
Advantages | High precision, material versatility, and low-temperature process. |
Challenges | High-vacuum requirements, complex equipment, and limited deposition rates. |
Discover how PVD can enhance your semiconductor manufacturing—contact our experts today!