The pyrolysis method for biochar production involves heating biomass in the absence of oxygen to decompose it into biochar, gases, and liquids. This process is influenced by factors such as temperature, heating rate, residence time, and biomass properties. Pyrolysis can be categorized into slow and fast pyrolysis, each yielding different product distributions. Slow pyrolysis, characterized by low heating rates and long residence times, maximizes biochar yield, while fast pyrolysis, with high heating rates and short residence times, favors liquid production. The process includes pre-treatment, pyrolysis, discharging, and de-dusting stages, ensuring efficient and environmentally friendly biochar production. Proper optimization of operating conditions is crucial to achieve desired product quality and yield.
Key Points Explained:
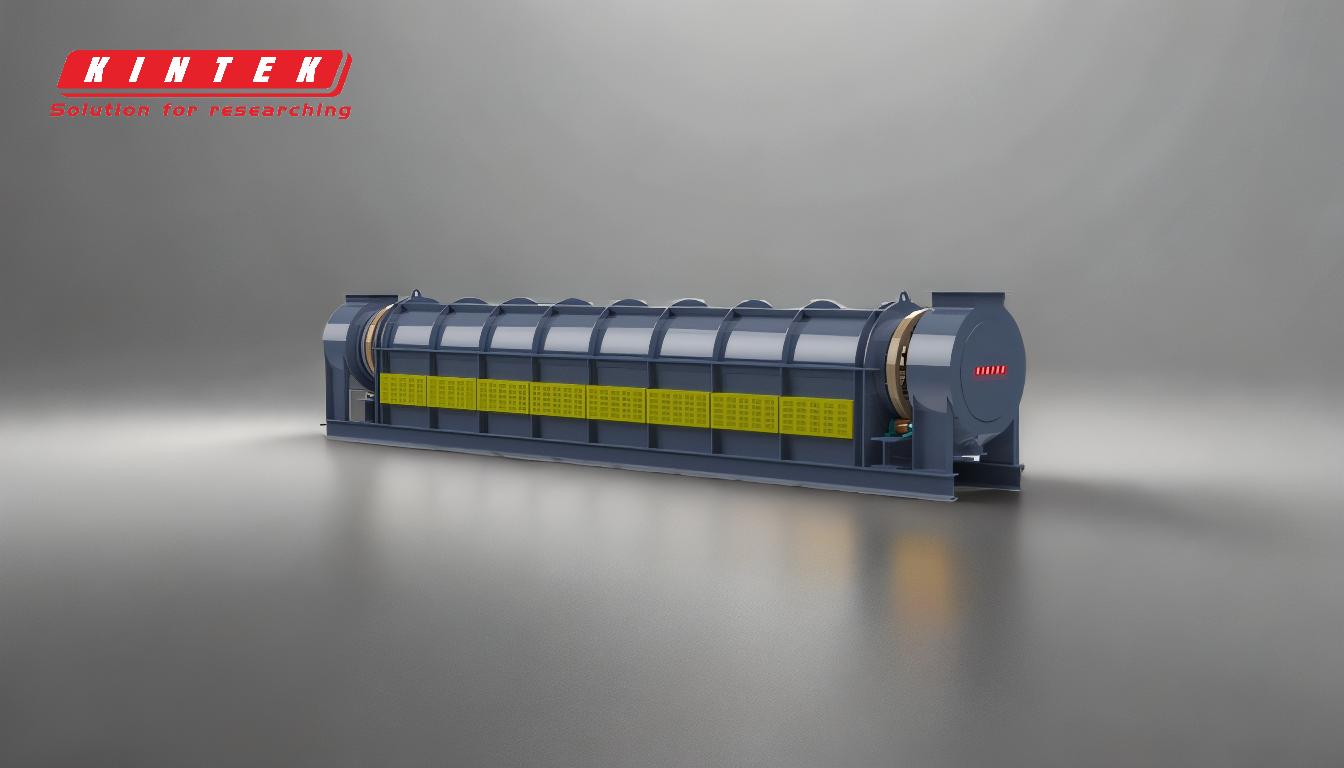
-
Definition of Pyrolysis:
- Pyrolysis is a thermal decomposition process that occurs in the absence of oxygen, converting biomass into biochar, gases, and liquids. This method is widely used for biochar production due to its ability to efficiently break down organic materials.
-
Types of Pyrolysis:
-
Slow Pyrolysis:
- Characterized by low heating rates (typically 0.1–1°C/s) and long residence times (minutes to hours).
- Maximizes biochar yield, making it suitable for applications where solid carbon sequestration is desired.
-
Fast Pyrolysis:
- Involves high heating rates (10–200°C/s) and short residence times (less than 2 seconds).
- Favors the production of liquid bio-oil, which can be used as a renewable fuel or chemical feedstock.
-
Slow Pyrolysis:
-
Key Factors Influencing Pyrolysis:
-
Temperature:
- The highest treatment temperature (HTT) significantly impacts the yield and properties of biochar. Higher temperatures generally increase the carbon content and stability of biochar but reduce its yield.
-
Heating Rate:
- Affects the distribution of pyrolysis products. Slow heating rates favor char production, while fast heating rates enhance liquid and gas yields.
-
Residence Time:
- Longer residence times at high temperatures promote secondary reactions, increasing gas yields. Shorter residence times are preferred for biochar production.
-
Biomass Properties:
- Moisture content, fixed carbon, and volatile matter in the biomass influence the pyrolysis process and product distribution. Lower moisture content and higher fixed carbon are generally favorable for biochar production.
-
Temperature:
-
Stages of Pyrolysis Process:
-
Pre-treatment:
- Involves drying and crushing the biomass to ensure uniform heating and efficient pyrolysis.
-
Pyrolysis:
- The biomass is heated in an oxygen-free environment, leading to thermal decomposition and the formation of biochar, gases, and liquids.
-
Discharging:
- The biochar is cooled to prevent further reactions and preserve its quality.
-
De-dusting:
- Exhaust gases are cleaned to reduce harmful substances, ensuring environmental compliance.
-
Pre-treatment:
-
Optimization of Pyrolysis Conditions:
- To maximize biochar yield and quality, specific conditions should be optimized:
- Low Temperatures and Heating Rates: Favor char production.
- Average Temperatures, High Heating Rates, and Short Gas Residence Time: Enhance liquid product yields.
- High Temperatures, Low Heating Rate, and Long Gas Residence Time: Increase gas yields.
- To maximize biochar yield and quality, specific conditions should be optimized:
-
Applications and Benefits of Biochar:
- Carbon Sequestration: Biochar is stable and can store carbon for centuries, contributing to climate change mitigation.
- Soil Amendment: Improves soil fertility, water retention, and microbial activity.
- Waste Management: Converts agricultural and forestry residues into valuable products, reducing waste and environmental impact.
By understanding and optimizing the pyrolysis process, producers can efficiently convert biomass into high-quality biochar, addressing environmental and agricultural challenges.
Summary Table:
Aspect | Details |
---|---|
Definition | Thermal decomposition of biomass in the absence of oxygen. |
Types of Pyrolysis | - Slow Pyrolysis: Low heating rates, long residence times, maximizes biochar. |
- Fast Pyrolysis: High heating rates, short residence times, favors liquid production. | |
Key Factors | - Temperature: Impacts biochar yield and properties. |
- Heating Rate: Influences product distribution. | |
- Residence Time: Affects gas and char yields. | |
- Biomass Properties: Moisture, fixed carbon, and volatile matter. | |
Process Stages | - Pre-treatment: Drying and crushing biomass. |
- Pyrolysis: Heating in oxygen-free environment. | |
- Discharging: Cooling biochar. | |
- De-dusting: Cleaning exhaust gases. | |
Applications | - Carbon sequestration. |
- Soil amendment. | |
- Waste management. |
Ready to optimize your biochar production? Contact our experts today for tailored solutions!