Pyrolysis of natural rubber is a thermal decomposition process that occurs in the absence of oxygen, typically at high temperatures (300-900℃). This process breaks down the rubber into various by-products, including pyrolysis oil, carbon black, and combustible gases. These products have significant industrial applications, such as alternative fuels, raw materials for chemicals, and energy generation. The yield and composition of the products depend on the specific conditions of the pyrolysis process and the properties of the rubber being processed.
Key Points Explained:
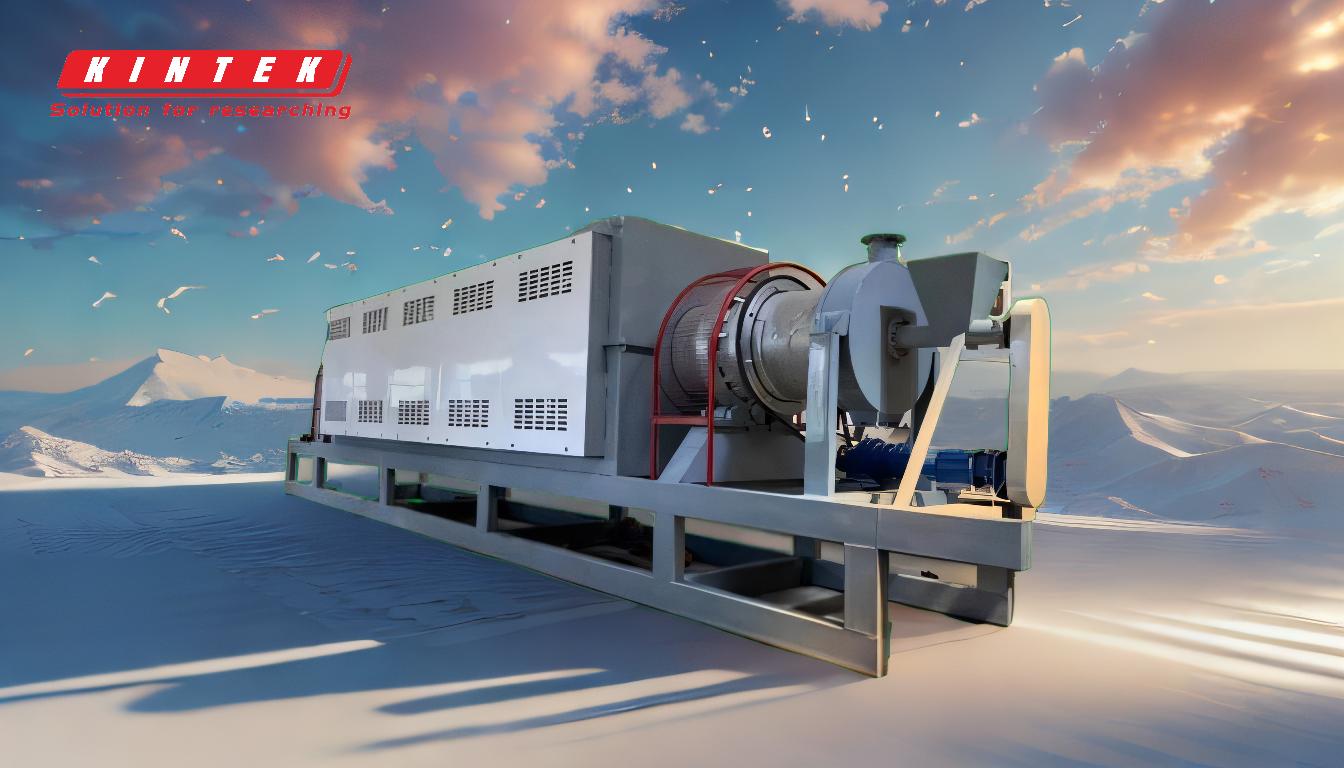
-
Definition of Pyrolysis:
- Pyrolysis is a thermochemical process where organic materials, such as natural rubber, are decomposed at high temperatures in the absence of oxygen.
- This process prevents combustion and instead breaks down the material into smaller molecules, resulting in solid, liquid, and gaseous products.
-
Process Conditions:
- Temperature: Pyrolysis typically occurs at temperatures ranging from 300℃ to 900℃. Higher temperatures generally increase the yield of gaseous products, while lower temperatures favor the production of liquids and solids.
- Absence of Oxygen: The lack of oxygen prevents combustion, allowing the material to decompose into its constituent parts rather than burning.
-
Products of Pyrolysis:
- Pyrolysis Oil: A liquid product that can be used as an alternative fuel or further refined into biodiesel. The oil output from natural rubber pyrolysis is typically around 35-45%.
- Carbon Black: A solid residue that can be used in various applications, including as a reinforcing agent in rubber products, as a pigment, or in the production of batteries. The yield of carbon black from natural rubber pyrolysis is usually 30-35%.
- Combustible Gases (Syn-gas): Non-condensable gases produced during pyrolysis, such as methane, hydrogen, and carbon monoxide. These gases are often used to generate heat energy for the pyrolysis process itself or for other industrial applications. The gas yield is typically around 8-15%.
-
Applications of Pyrolysis Products:
- Pyrolysis Oil: Can be used as a substitute for conventional fuels in industrial boilers, furnaces, and engines. It can also be refined into higher-value products like diesel or gasoline.
- Carbon Black: Widely used in the rubber industry to improve the strength and durability of rubber products. It is also used in the production of inks, paints, and plastics.
- Combustible Gases: Provide a source of energy for the pyrolysis process, reducing the need for external energy sources. They can also be used in power generation or as a feedstock for chemical synthesis.
-
Factors Affecting Pyrolysis Yield:
- Temperature: Higher temperatures generally increase the yield of gases, while lower temperatures favor the production of liquids and solids.
- Feedstock Composition: The type of rubber being pyrolyzed can affect the yield and composition of the products. For example, natural rubber may produce different yields compared to synthetic rubber or rubber from tires.
- Reaction Time: Longer reaction times can lead to more complete decomposition, potentially increasing the yield of gases and reducing the amount of solid residue.
-
Environmental and Economic Benefits:
- Waste Reduction: Pyrolysis provides a way to recycle natural rubber waste, reducing the amount of material that ends up in landfills.
- Resource Recovery: The process recovers valuable materials like oil, carbon black, and gases, which can be used in various industrial applications.
- Energy Efficiency: The combustible gases produced during pyrolysis can be used to generate heat, reducing the overall energy requirements of the process.
In summary, the pyrolysis of natural rubber is a valuable process for converting waste rubber into useful products. By understanding the conditions and factors that influence the process, it is possible to optimize the yield and quality of the resulting products, making pyrolysis an environmentally and economically beneficial solution for rubber waste management.
Summary Table:
Aspect | Details |
---|---|
Process | Thermal decomposition at 300-900℃ in the absence of oxygen. |
Products | Pyrolysis oil (35-45%), carbon black (30-35%), and combustible gases (8-15%). |
Applications | Alternative fuels, rubber reinforcement, energy generation, and more. |
Key Factors | Temperature, feedstock composition, and reaction time. |
Benefits | Waste reduction, resource recovery, and energy efficiency. |
Learn how pyrolysis can transform your rubber waste into valuable resources—contact us today!