A vacuum leak test is a critical procedure used to ensure the integrity of a vacuum system, such as a furnace, by detecting and quantifying leaks. The range of a vacuum leak test typically depends on the sensitivity of the equipment and the specific requirements of the application. The primary goal is to maintain a leak-tight environment, preventing contamination from external impurities. The test measures the rate at which gas escapes or enters the system, often expressed in units like mbar·L/s or Pa·m³/s. The acceptable leak rate varies based on the system's design and operational standards, ensuring that the vacuum environment remains stable and uncontaminated.
Key Points Explained:
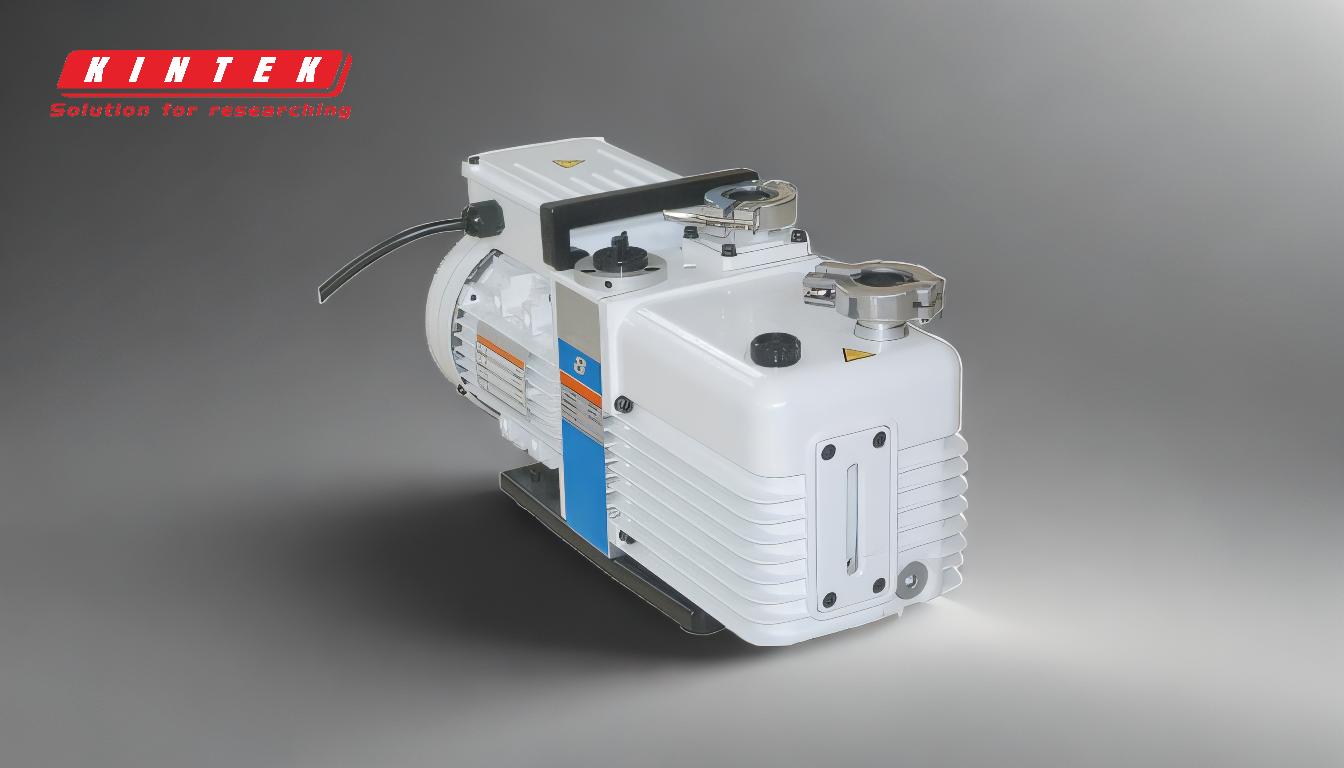
-
Purpose of a Vacuum Leak Test:
- The primary purpose of a vacuum leak test is to ensure the integrity of the vacuum system, such as a furnace, by detecting and quantifying leaks. This is crucial for maintaining a contamination-free environment, especially in processes like heat treatment or material processing where impurities can compromise the quality of the final product.
-
Leak Rate Measurement:
- The leak rate is typically measured in units such as mbar·L/s or Pa·m³/s. These units quantify the volume of gas that escapes or enters the system per unit of time. The sensitivity of the measurement depends on the equipment used, such as helium leak detectors or pressure decay testers.
-
Range of Leak Rates:
- The acceptable range for a vacuum leak test varies depending on the application. For example:
- In high-vacuum systems, the acceptable leak rate might be as low as 10^-9 mbar·L/s.
- In less critical applications, such as industrial furnaces, the acceptable leak rate could be in the range of 10^-5 to 10^-3 mbar·L/s.
- The specific range is determined by the system's design, operational requirements, and industry standards.
- The acceptable range for a vacuum leak test varies depending on the application. For example:
-
Factors Influencing the Leak Test Range:
- System Design: The complexity and size of the vacuum system can influence the acceptable leak rate. Larger systems may have higher baseline leak rates due to their increased surface area.
- Operational Standards: Different industries have varying standards for acceptable leak rates. For example, semiconductor manufacturing may require stricter leak rate tolerances compared to general industrial applications.
- Environmental Conditions: External factors such as temperature and pressure can affect the leak rate measurement. Proper calibration and testing conditions are essential for accurate results.
-
Testing Methods:
- Helium Leak Detection: This is one of the most sensitive methods, using helium as a tracer gas to detect even the smallest leaks. It is commonly used in high-vacuum systems.
- Pressure Decay Testing: This method measures the drop in pressure over time to determine the leak rate. It is less sensitive than helium detection but is suitable for many industrial applications.
- Bubble Testing: A simple and cost-effective method where the system is pressurized and submerged in a liquid to visually detect bubbles indicating leaks.
-
Importance of Regular Testing:
- Regular vacuum leak testing is essential to ensure the long-term performance and reliability of the vacuum system. Leaks can develop over time due to wear and tear, thermal cycling, or mechanical stress. Regular testing helps identify and address leaks before they compromise the system's integrity.
By understanding the range and factors influencing a vacuum leak test, equipment and consumable purchasers can make informed decisions about the appropriate testing methods and acceptable leak rates for their specific applications. This ensures the maintenance of a contamination-free environment and the optimal performance of the vacuum system.
Summary Table:
Aspect | Details |
---|---|
Purpose | Ensure vacuum system integrity by detecting and quantifying leaks. |
Leak Rate Units | mbar·L/s or Pa·m³/s |
Acceptable Leak Rates | High-vacuum: 10^-9 mbar·L/s; Industrial: 10^-5 to 10^-3 mbar·L/s |
Testing Methods | Helium leak detection, pressure decay testing, bubble testing |
Key Factors | System design, operational standards, environmental conditions |
Ensure your vacuum system's integrity—contact our experts today for tailored leak testing solutions!