Chemical Vapor Deposition (CVD) is a widely used technique for synthesizing high-quality materials, such as graphene, on a substrate. The role of a catalyst in CVD is pivotal, as it significantly lowers the energy barrier required for the chemical reactions to occur. Without a catalyst, the process would demand extremely high temperatures, making it inefficient and impractical. The catalyst not only reduces the required temperature but also enhances the quality and uniformity of the deposited material. Below, we explore the key aspects of how catalysts function in CVD processes, particularly in the context of graphene production.
Key Points Explained:
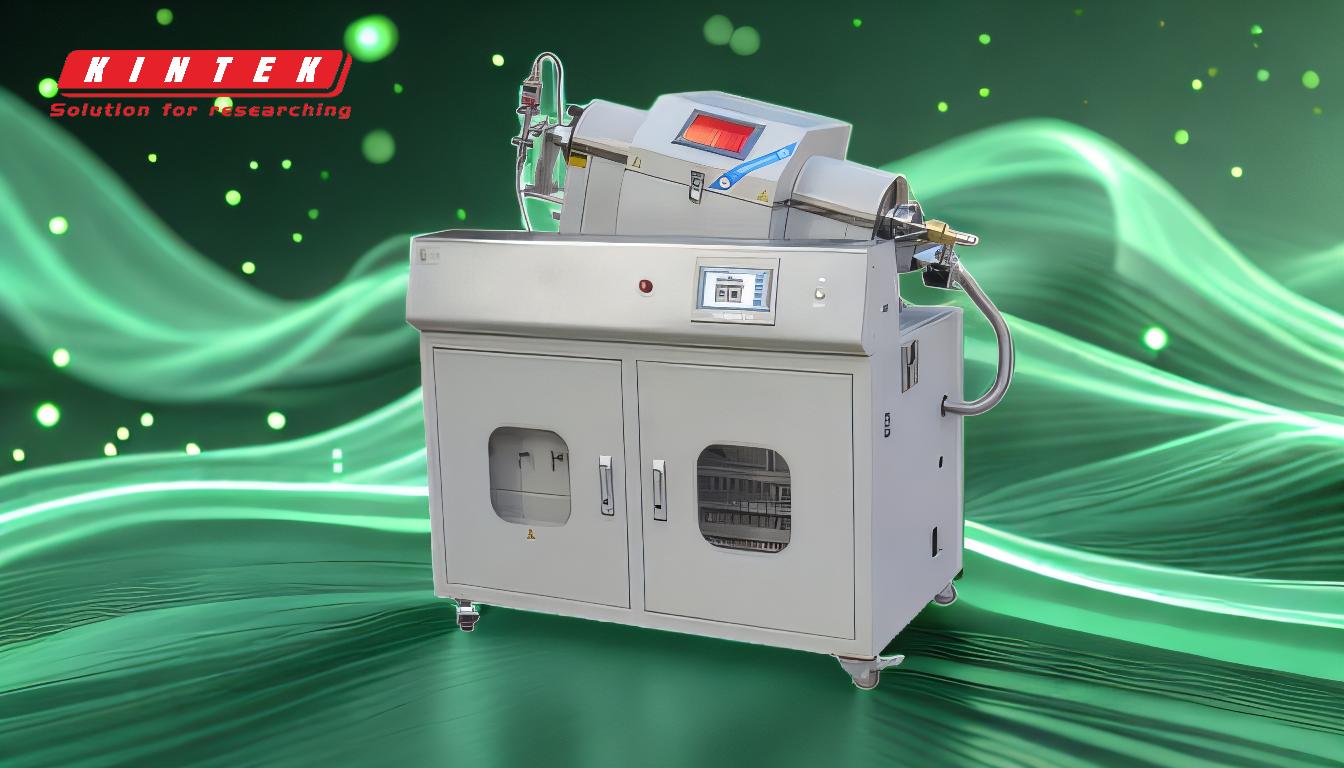
-
Temperature Reduction:
- Role: Catalysts in CVD processes, such as those used in graphene production, play a crucial role in lowering the activation energy required for the reaction. This reduction in energy translates to a significant decrease in the necessary temperature for the process.
- Example: Without a catalyst, the production of graphene via CVD would require temperatures exceeding 2500°C, which is impractical for most industrial applications. By introducing a catalyst, this temperature can be reduced to more manageable levels, typically around 800-1000°C.
- Impact: Lowering the temperature not only makes the process more energy-efficient but also reduces the risk of damaging the substrate or the equipment used in the process.
-
Enhanced Reaction Kinetics:
- Role: Catalysts accelerate the rate of chemical reactions by providing an alternative pathway with a lower activation energy. This is particularly important in CVD, where the deposition of material needs to be both rapid and controlled.
- Mechanism: In the case of graphene production, the catalyst facilitates the decomposition of carbon-containing gases (such as methane) into carbon atoms, which then form the graphene lattice on the substrate.
- Outcome: The presence of a catalyst ensures that the reaction proceeds at a faster rate, leading to quicker deposition times and higher throughput in industrial settings.
-
Improved Material Quality:
- Role: Catalysts not only speed up the reaction but also influence the quality of the deposited material. In graphene production, the catalyst helps in forming a uniform, high-quality monolayer of graphene.
- Example: Metals like copper and nickel are commonly used as catalysts in graphene CVD. These metals provide a surface that promotes the uniform growth of graphene, leading to fewer defects and better electrical properties.
- Impact: The use of a catalyst results in graphene with superior electrical conductivity, mechanical strength, and optical properties, which are essential for applications in electronics, sensors, and other advanced technologies.
-
Substrate Interaction:
- Role: The choice of catalyst also affects how the deposited material interacts with the substrate. In CVD, the catalyst must be carefully selected to ensure good adhesion and compatibility with the substrate material.
- Considerations: For instance, copper is often preferred for graphene CVD because it has a low carbon solubility, which helps in achieving a single-layer graphene growth. Nickel, on the other hand, has higher carbon solubility, which can lead to multilayer graphene formation.
- Outcome: The right catalyst-substrate combination ensures that the deposited material adheres well to the substrate, leading to durable and reliable end products.
-
Catalyst Regeneration and Reusability:
- Role: In some CVD processes, the catalyst can be regenerated and reused, which is economically beneficial. This is particularly relevant in large-scale industrial applications where the cost of catalysts can be significant.
- Mechanism: After the deposition process, the catalyst can often be cleaned and prepared for reuse in subsequent cycles. This reduces waste and lowers the overall cost of production.
- Impact: The ability to regenerate and reuse catalysts makes the CVD process more sustainable and cost-effective, which is crucial for its widespread adoption in various industries.
In summary, the role of a catalyst in CVD is multifaceted, encompassing temperature reduction, enhanced reaction kinetics, improved material quality, optimal substrate interaction, and economic benefits through regeneration and reusability. These factors collectively make catalysts indispensable in the efficient and effective production of high-quality materials like graphene via CVD.
Summary Table:
Role of Catalyst in CVD | Key Benefits |
---|---|
Temperature Reduction | Lowers required temperature, making the process energy-efficient and practical. |
Enhanced Reaction Kinetics | Accelerates reaction rates, enabling faster deposition and higher throughput. |
Improved Material Quality | Ensures uniform, high-quality graphene with superior electrical properties. |
Substrate Interaction | Optimizes adhesion and compatibility between the deposited material and substrate. |
Regeneration and Reusability | Reduces costs and waste by enabling catalyst reuse in industrial applications. |
Interested in optimizing your CVD process? Contact our experts today to learn more!