In pyrolysis, a catalyst plays a crucial role in enhancing the efficiency and quality of the process by promoting specific chemical reactions. It improves the yield of valuable biofuels and chemicals, such as oil from plastics, and ensures the production of higher-quality products that can be upgraded to drop-in fuels. Catalysts like biochar-based ones are particularly effective in driving desirable reactions, making the process more economically and environmentally viable. Below, the key points of the role of catalysts in pyrolysis are explained in detail.
Key Points Explained:
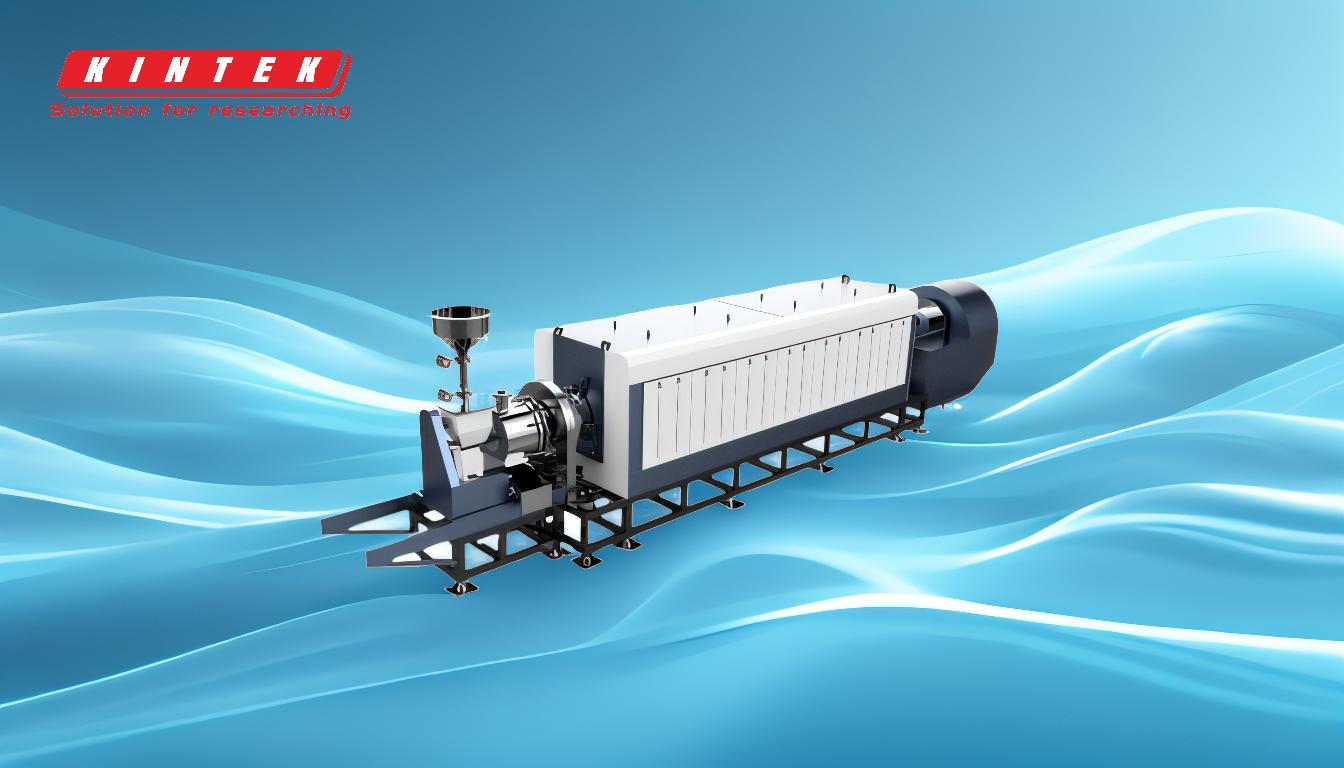
-
Promotion of Desirable Chemical Reactions
- Catalysts accelerate specific chemical reactions during pyrolysis, such as cracking, dehydrogenation, and isomerization, which break down complex molecules into simpler, more valuable ones.
- For example, in plastic pyrolysis, catalysts help convert long-chain polymers into shorter-chain hydrocarbons, producing oil and other useful chemicals.
- This targeted reaction promotion ensures that the process is more efficient and yields higher quantities of desired products.
-
Improvement in Yield of Valuable Products
- By facilitating optimal reaction pathways, catalysts increase the yield of valuable biofuels and chemicals, such as bio-oil, syngas, and biochar.
- For instance, biochar-based catalysts have been shown to enhance the production of biofuels by improving the breakdown of biomass or plastic feedstocks.
- This higher yield makes pyrolysis a more economically attractive process for producing renewable energy and chemical feedstocks.
-
Enhancement of Product Quality
- Catalysts improve the quality of pyrolysis products by reducing the formation of unwanted byproducts, such as tar or char, and ensuring a more uniform output.
- The resulting products, such as oils, are of higher quality and can be more easily upgraded to drop-in fuels, which are compatible with existing fuel infrastructure.
- This reduces the need for further refining and makes the end products more marketable.
-
Facilitation of Drop-in Fuel Production
- Drop-in fuels are synthetic fuels that contain only molecules found in conventional hydrocarbon fuels, making them directly usable in existing engines and infrastructure.
- Catalysts enable the production of pyrolysis oils that are rich in these desirable molecules, simplifying the upgrading process and reducing costs.
- This is particularly important for the transition to renewable energy sources, as it allows for a seamless integration of biofuels into current systems.
-
Economic and Environmental Benefits
- By improving reaction efficiency and product quality, catalysts reduce the overall energy and resource requirements of the pyrolysis process.
- This leads to lower operational costs and a smaller environmental footprint, making pyrolysis a more sustainable option for waste management and energy production.
- Additionally, the use of biochar-based catalysts, which are often derived from waste materials, further enhances the sustainability of the process.
-
Versatility in Feedstock Conversion
- Catalysts enable the pyrolysis process to handle a wide range of feedstocks, including biomass, plastics, and other organic waste materials.
- This versatility is crucial for addressing diverse waste streams and maximizing resource recovery.
- For example, catalysts can be tailored to optimize the conversion of specific feedstocks, such as plastic waste, into high-value products like oil.
In summary, catalysts are indispensable in pyrolysis, as they enhance reaction efficiency, improve product yield and quality, and enable the production of drop-in fuels. Their role not only makes pyrolysis more economically viable but also contributes to sustainable waste management and renewable energy production.
Summary Table:
Key Role of Catalysts | Impact |
---|---|
Promotion of Desirable Reactions | Accelerates cracking, dehydrogenation, and isomerization for better yields. |
Improved Product Yield | Increases bio-oil, syngas, and biochar production from feedstocks. |
Enhanced Product Quality | Reduces unwanted byproducts, ensuring uniform, high-quality outputs. |
Drop-in Fuel Production | Simplifies upgrading to fuels compatible with existing infrastructure. |
Economic & Environmental Benefits | Lowers costs and reduces the environmental footprint of pyrolysis. |
Versatility in Feedstock Conversion | Optimizes conversion of biomass, plastics, and organic waste into oil. |
Unlock the full potential of pyrolysis with tailored catalysts—contact our experts today!