Plasma plays a critical role in Plasma-Enhanced Chemical Vapor Deposition (PECVD) by enabling chemical reactions at lower temperatures, enhancing the deposition process, and improving the quality of thin films. It achieves this by generating reactive species such as excited neutrals, free radicals, ions, and electrons through inelastic collisions. These species facilitate the fragmentation of precursor molecules, surface activation, and film densification, making PECVD a versatile and efficient method for depositing high-quality thin films and nanostructured materials.
Key Points Explained:
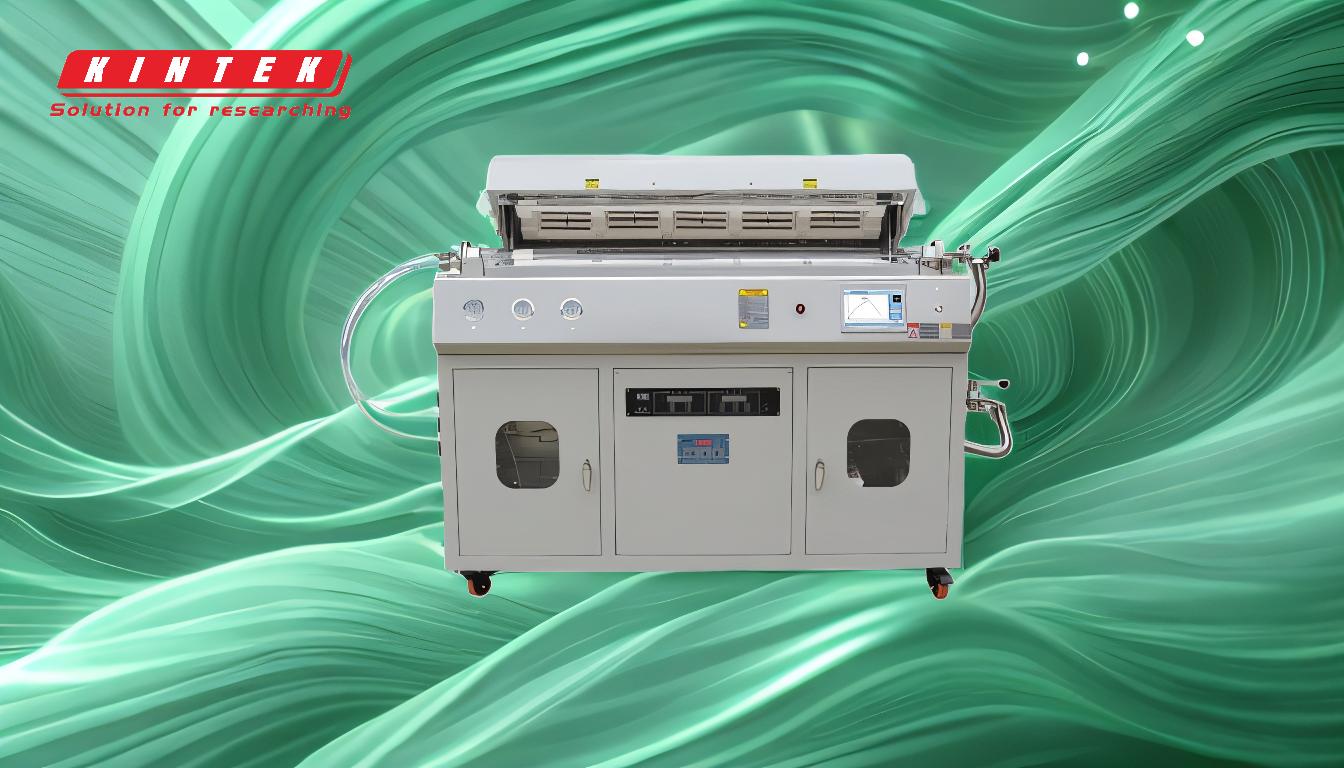
-
Promotion of Chemical Reactions
- Plasma in PECVD is essential for promoting chemical reactions at lower temperatures compared to traditional CVD methods.
- It achieves this by generating reactive species (excited neutrals, free radicals, ions, and electrons) through inelastic collisions between electrons and gas molecules.
- These reactive species enable the deposition of thin films without requiring high gas temperatures, making the process more energy-efficient and suitable for temperature-sensitive substrates.
-
Fragmentation of Precursor Molecules
- Plasma fragments volatile precursor molecules into smaller, reactive components, such as radicals and ions.
- For example, in the case of metallic nanoparticles, plasma fragments precursor molecules, which then react on nanoparticle surfaces to form coatings that mimic the chemistry of the original precursor.
- This fragmentation is crucial for creating uniform and high-quality thin films.
-
Surface Activation and Film Densification
- Plasma-generated ions and electrons have sufficient energy to break chemical bonds, creating radicals in the gas phase.
- Ions bombarding the surface of the growing film activate the surface by creating dangling bonds, which enhance film growth.
- Additionally, ions help densify the growing film by etching weakly bonded terminating groups, leading to improved film quality and durability.
-
Lower Temperature Deposition
- One of the key advantages of PECVD is its ability to deposit films at lower temperatures.
- Plasma increases the activation energy of reactants, reducing the required reaction temperature.
- This is particularly beneficial for applications involving temperature-sensitive materials or substrates.
-
Enhanced Deposition Efficiency
- Plasma excitation of deposition precursors enhances the overall efficiency of the deposition process.
- By generating reactive species, plasma ensures that precursor molecules are effectively utilized, reducing waste and improving reaction efficiency.
- This is especially important in industrial applications where cost and resource efficiency are critical.
-
Role of Plasma Generators
- Plasma generators in PECVD equipment are designed to create a uniform and stable plasma environment.
- For example, inductive coupling between the plasma generator and the furnace tube ensures effective plasma coverage, which is essential for consistent film deposition.
- The design of electrodes and plasma generators also plays a role in optimizing plasma power and thermal equilibrium, contributing to better crystal quality in deposited films.
-
Plasma in LPCVD and PACVD
- While PECVD is the primary focus, plasma also plays a role in Low-Pressure CVD (LPCVD) and Plasma-Assisted CVD (PACVD).
- In LPCVD, plasma is generated using an ion source and a coil, creating a radially nonuniform plasma that helps trap ions and electrons near the coil's surface.
- This mechanism is essential for depositing thin films and nanostructured materials with precise control over film properties.
In summary, plasma is indispensable in PECVD for enabling chemical reactions, fragmenting precursor molecules, activating surfaces, and enhancing deposition efficiency at lower temperatures. Its ability to generate reactive species and improve film quality makes it a cornerstone of modern thin-film deposition technologies.
Summary Table:
Key Role of Plasma in PECVD | Description |
---|---|
Promotes Chemical Reactions | Enables reactions at lower temperatures by generating reactive species. |
Fragments Precursor Molecules | Breaks down molecules into radicals and ions for uniform thin films. |
Activates Surfaces | Creates dangling bonds for enhanced film growth and densification. |
Lowers Deposition Temperature | Reduces reaction temperature, ideal for sensitive substrates. |
Enhances Deposition Efficiency | Improves precursor utilization and reduces waste. |
Optimizes Plasma Generators | Ensures uniform plasma coverage for consistent film quality. |
Supports LPCVD and PACVD | Plays a role in other CVD methods for precise film control. |
Learn how plasma can revolutionize your thin-film deposition process—contact our experts today!