Inert gases play a crucial role in various industries due to their non-reactive properties. They are primarily used to create controlled environments that prevent unwanted chemical reactions, such as oxidation and hydrolysis, which can degrade materials or samples. Inert gases like nitrogen and argon are widely employed in chemical reactions, heat treatment processes, and fire prevention measures. Their ability to maintain a stable, non-reactive atmosphere ensures the integrity of materials, enhances safety, and improves the efficiency of industrial processes. This makes inert gases indispensable in applications ranging from laboratory research to large-scale manufacturing.
Key Points Explained:
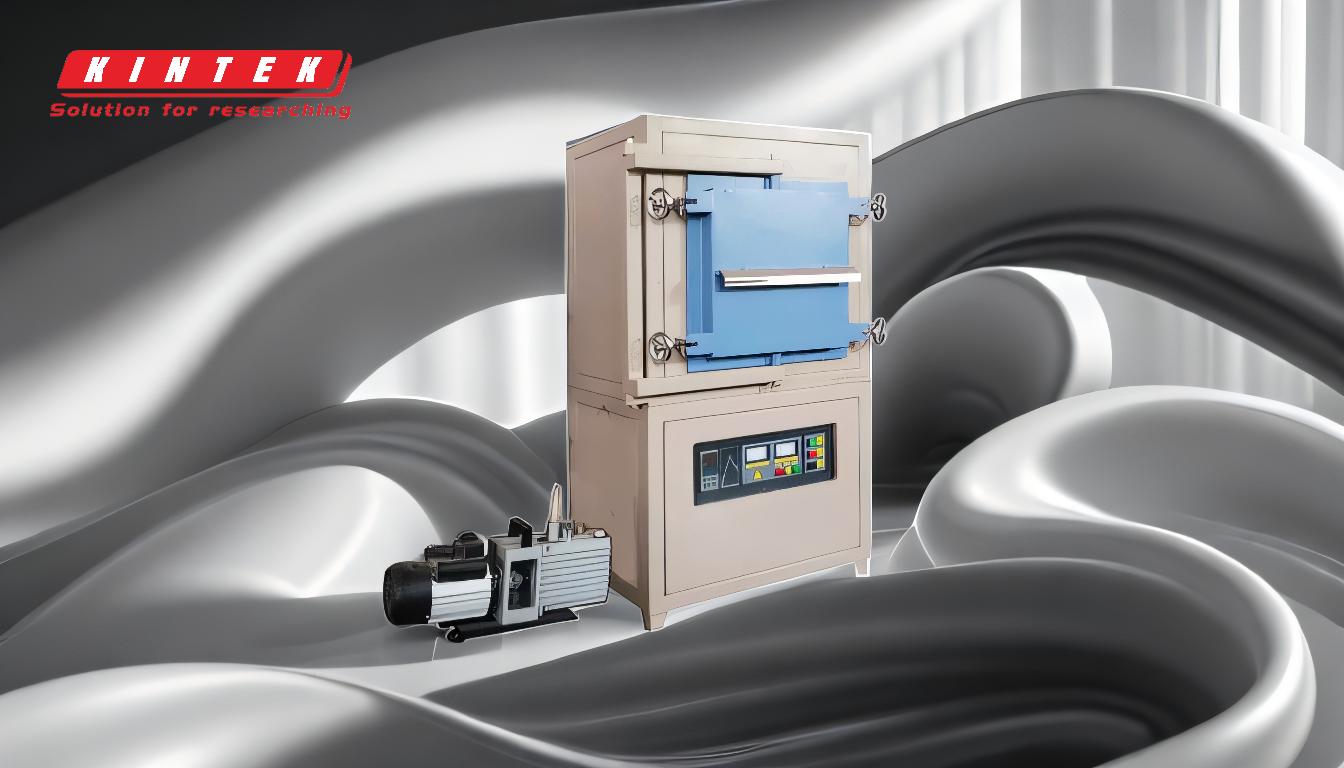
-
Prevention of Unwanted Chemical Reactions:
- Inert gases are used to avoid undesirable reactions such as oxidation and hydrolysis, which can degrade samples or materials.
- These reactions often occur when materials are exposed to oxygen or moisture in the air. By replacing the air with an inert gas, these reactions are minimized or completely prevented.
- This is particularly important in the chemical industry, where maintaining the purity and integrity of substances is critical.
-
Fire and Explosion Prevention:
- Inert gases are employed to purge transfer lines and vessels, reducing the risk of fire and explosion.
- By displacing oxygen, which is necessary for combustion, inert gases create a safer environment for handling flammable materials.
- This application is vital in industries where volatile substances are processed or stored.
-
Heat Treatment Applications:
- Inert gases are used in heat treatment processes to protect materials from oxidation and other reactive processes.
- Nitrogen is commonly used as an inert gas in heat treatment furnaces to provide a protective atmosphere where carbon, oxygen, and nitrogen do not react with steel.
- Argon is another inert gas used for similar purposes, especially in applications requiring higher purity or where nitrogen might react with certain materials.
- Inert gas atmosphere furnaces are equipped with advanced controls and insulation to ensure optimal performance and cost efficiency.
-
Material Integrity and Quality:
- The use of inert gases helps maintain the integrity and quality of materials during processing and storage.
- By preventing oxidation and other degradation processes, inert gases ensure that materials retain their desired properties and performance characteristics.
- This is crucial in industries such as metallurgy, electronics, and pharmaceuticals, where material quality directly impacts the final product.
-
Cost Efficiency and Process Optimization:
- The use of inert gases can lead to significant cost savings by reducing material losses due to degradation and improving process efficiency.
- Advanced inert gas systems, such as those with precision temperature controls and energy-efficient insulation, optimize the use of inert gases, further enhancing cost-effectiveness.
- These systems also contribute to consistent product quality, reducing the need for rework or waste.
In summary, inert gases are essential in creating stable, non-reactive environments that protect materials from degradation, enhance safety, and improve process efficiency. Their applications span across various industries, making them a critical component in modern manufacturing and research.
Summary Table:
Application | Key Benefit |
---|---|
Prevention of Chemical Reactions | Minimizes oxidation and hydrolysis, preserving material integrity. |
Fire and Explosion Prevention | Displaces oxygen, reducing combustion risks in volatile environments. |
Heat Treatment Processes | Protects materials from oxidation, ensuring consistent quality in heat treatment. |
Material Integrity and Quality | Maintains desired properties by preventing degradation during processing. |
Cost Efficiency | Reduces material losses and improves process efficiency, lowering overall costs. |
Ready to optimize your processes with inert gases? Contact our experts today to learn more!