The silicon carbide method refers to a process used in the production of silicon carbide (SiC), a compound of silicon and carbon known for its exceptional hardness and thermal conductivity. This method typically involves the high-temperature reaction of silica (SiO₂) and carbon (C) in a furnace, often using silicon carbide crucibles to contain the reaction materials. Silicon carbide is widely used in various industries, including electronics, automotive, and abrasives, due to its durability and resistance to high temperatures. The method is crucial for producing high-quality SiC, which is essential for advanced applications like semiconductors and cutting tools.
Key Points Explained:
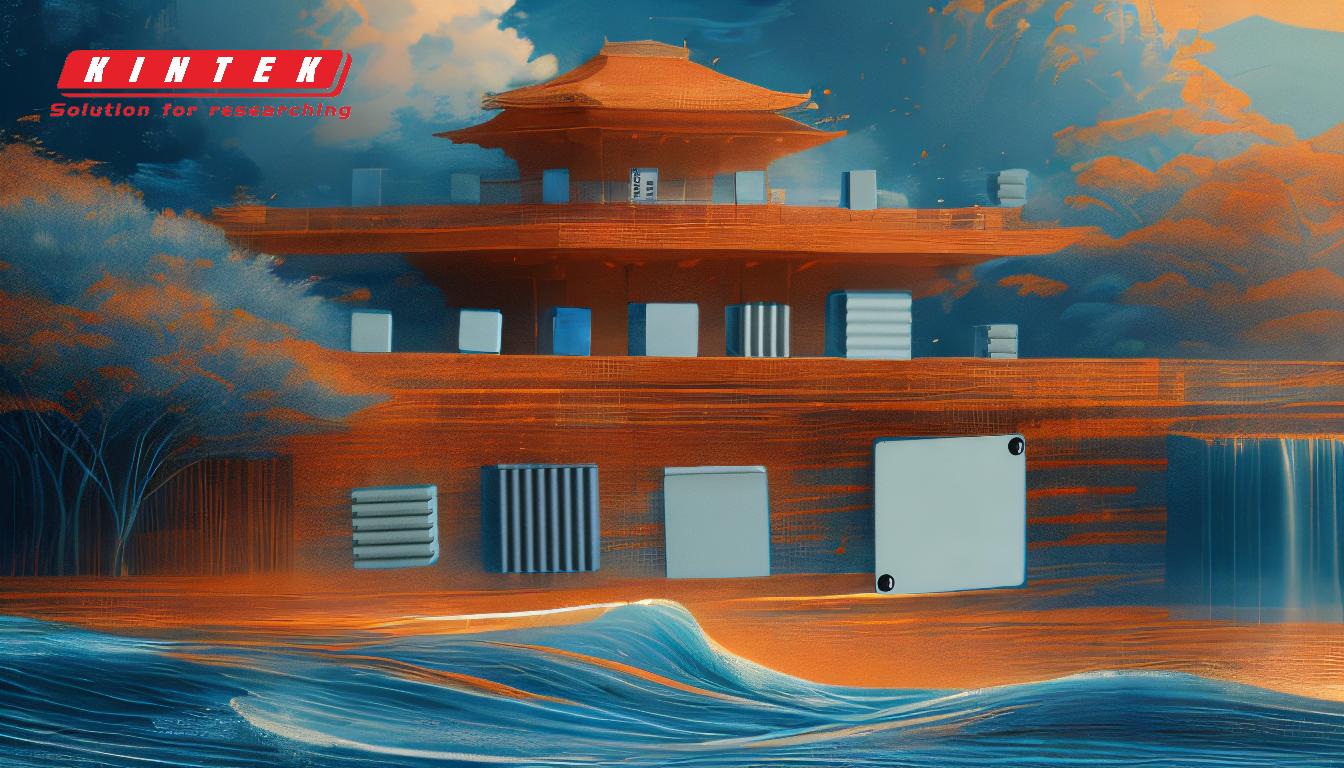
-
Definition of Silicon Carbide Method:
- The silicon carbide method is a chemical process that synthesizes silicon carbide by reacting silica (SiO₂) with carbon (C) at high temperatures, typically above 2000°C. This reaction is often carried out in specialized furnaces, and the use of silicon carbide crucibles is common due to their ability to withstand extreme temperatures and chemical stability.
-
Chemical Reaction Involved:
- The core reaction in the silicon carbide method is:
[ \text{SiO}_2 + 3\text{C} \rightarrow \text{SiC} + 2\text{CO} ] - This reaction requires precise control of temperature and pressure to ensure the formation of high-purity silicon carbide. The carbon source is usually in the form of petroleum coke or other carbon-rich materials.
- The core reaction in the silicon carbide method is:
-
Role of Silicon Carbide Crucibles:
- Silicon carbide crucibles are essential in this method due to their ability to endure the extreme conditions of the reaction. They are chemically inert, thermally stable, and resistant to thermal shock, making them ideal for containing the reactants and preventing contamination.
-
Applications of Silicon Carbide:
- Silicon carbide produced through this method is used in a variety of industries:
- Electronics: As a semiconductor material in high-power and high-temperature devices.
- Automotive: In brake discs and other components requiring high thermal conductivity and durability.
- Abrasives: For cutting, grinding, and polishing due to its hardness.
- Refractories: In furnaces and kilns for their heat resistance.
- Silicon carbide produced through this method is used in a variety of industries:
-
Advantages of the Silicon Carbide Method:
- High-purity silicon carbide can be produced with minimal impurities.
- The method is scalable for industrial production.
- The resulting material has excellent mechanical, thermal, and electrical properties, making it suitable for advanced applications.
-
Challenges and Considerations:
- The process requires high energy input due to the extreme temperatures needed.
- Precise control of raw material quality and reaction conditions is necessary to achieve consistent results.
- The cost of silicon carbide crucibles and other equipment can be high, but their durability often justifies the investment.
-
Future Trends:
- Advances in furnace technology and material science are expected to improve the efficiency and reduce the cost of the silicon carbide method.
- The growing demand for silicon carbide in electric vehicles and renewable energy systems is driving innovation in production techniques.
By understanding the silicon carbide method and its critical components, such as silicon carbide crucibles, industries can leverage this material for cutting-edge applications while optimizing production processes.
Summary Table:
Aspect | Details |
---|---|
Definition | Chemical process to synthesize silicon carbide (SiC) from silica and carbon. |
Reaction | SiO₂ + 3C → SiC + 2CO (requires >2000°C). |
Key Component | Silicon carbide crucibles for high-temperature stability. |
Applications | Electronics, automotive, abrasives, refractories. |
Advantages | High-purity SiC, scalable production, excellent material properties. |
Challenges | High energy input, precise control, equipment costs. |
Future Trends | Improved efficiency, reduced costs, driven by EV and renewable energy demand. |
Discover how silicon carbide can transform your industrial processes—contact our experts today!