Electron beam evaporation is a sophisticated physical vapor deposition (PVD) technique used to deposit thin films of materials with high melting points. The process relies on a high-energy electron beam generated by a heated tungsten filament, which emits electrons through thermionic emission. These electrons are accelerated by a high-voltage electric field and focused onto a target material using a magnetic field. The kinetic energy of the electrons is converted into thermal energy upon impact, heating the target material to its evaporation point. The resulting vapor then condenses onto a substrate to form a thin film. This method is highly effective in vacuum environments, minimizing contamination and enabling precise control over the deposition process.
Key Points Explained:
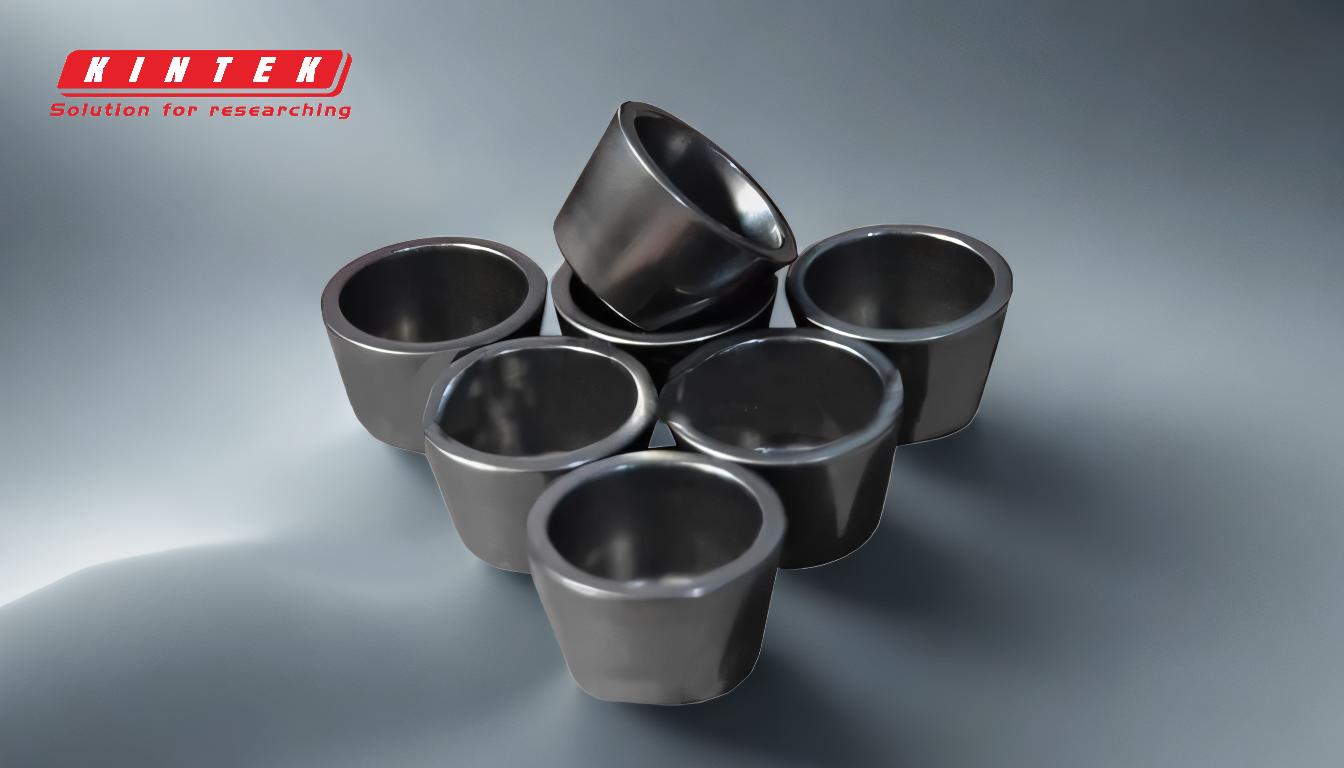
-
Electron Beam Generation:
- The process begins with a tungsten filament heated by an electric current, typically between 5 and 10 kV. This heating causes thermionic emission, where electrons are released from the filament due to thermal energy.
- The emitted electrons are then accelerated by a high-voltage electric field, gaining significant kinetic energy.
-
Focusing the Electron Beam:
- A magnetic field is used to focus the high-energy electrons into a concentrated beam. This ensures that the electrons are directed precisely onto the target material.
- The focused electron beam is directed toward a crucible containing the material to be evaporated. The crucible is often water-cooled to prevent overheating and damage.
-
Energy Conversion and Evaporation:
- When the electron beam strikes the target material, the kinetic energy of the electrons is converted into thermal energy, rapidly heating the material.
- The intense heat causes the material to evaporate or sublimate, releasing it in a vapor phase. This process can achieve extremely high temperatures, making it suitable for materials with very high melting points.
-
Vacuum Environment:
- The entire process occurs within a high vacuum chamber, typically at pressures as low as 10^-7 mbar. The vacuum minimizes contamination from background gases, ensuring the purity of the deposited thin film.
- The vacuum also allows for high vapor pressures at relatively low temperatures, facilitating the evaporation of materials that would otherwise require much higher temperatures.
-
Deposition onto Substrate:
- The vaporized material disperses within the vacuum chamber and condenses onto a substrate positioned above the crucible. This forms a thin, uniform film on the substrate.
- The deposition is a line-of-sight process, meaning the material deposits primarily on surfaces directly exposed to the vapor stream. This characteristic is beneficial for lift-off processes but may limit coverage on complex geometries or sidewalls.
-
Reactive Deposition:
- In some cases, reactive gases such as oxygen or nitrogen can be introduced into the chamber. These gases react with the vaporized material to form non-metallic films, such as oxides or nitrides, expanding the range of materials that can be deposited.
-
Advantages of Electron Beam Evaporation:
- High Temperature Capability: The method can evaporate materials with extremely high melting points, which are difficult to process using other techniques.
- High Purity Films: The vacuum environment and precise control over the electron beam result in films with minimal contamination.
- Versatility: The process can be used to deposit a wide range of materials, including metals, ceramics, and semiconductors.
-
Applications:
- Electron beam evaporation is widely used in industries requiring high-precision thin films, such as semiconductor manufacturing, optical coatings, and aerospace components.
- It is particularly valuable for applications requiring high-temperature materials or films with specific electrical, optical, or mechanical properties.
By understanding these key points, one can appreciate the complexity and precision of electron beam evaporation, a process that combines advanced physics and engineering to achieve high-performance thin film deposition.
Summary Table:
Key Aspect | Details |
---|---|
Electron Beam Generation | Tungsten filament heated to 5-10 kV, emits electrons via thermionic emission. |
Focusing the Electron Beam | Magnetic field focuses electrons onto the target material. |
Energy Conversion | Kinetic energy converts to thermal energy, evaporating the target material. |
Vacuum Environment | Operates at pressures as low as 10^-7 mbar, ensuring high-purity films. |
Deposition onto Substrate | Vapor condenses onto a substrate, forming a thin, uniform film. |
Reactive Deposition | Reactive gases (e.g., oxygen, nitrogen) create non-metallic films. |
Advantages | High temperature capability, high purity, and versatility. |
Applications | Semiconductor manufacturing, optical coatings, aerospace components. |
Discover how electron beam evaporation can elevate your thin film processes—contact our experts today!