The sputtering process of evaporation is a widely used thin film deposition technique in industries such as semiconductors, optics, and solar panels. It involves bombarding a target material with high-energy particles, typically argon ions, in a vacuum chamber. This bombardment ejects atoms from the target, which then deposit onto a substrate, forming a thin film. The process is highly controlled, allowing for precise deposition rates and the creation of dense, high-quality films. Magnetron sputtering, a variant of this process, enhances efficiency and control, making it ideal for applications in microelectronics and optical devices.
Key Points Explained:
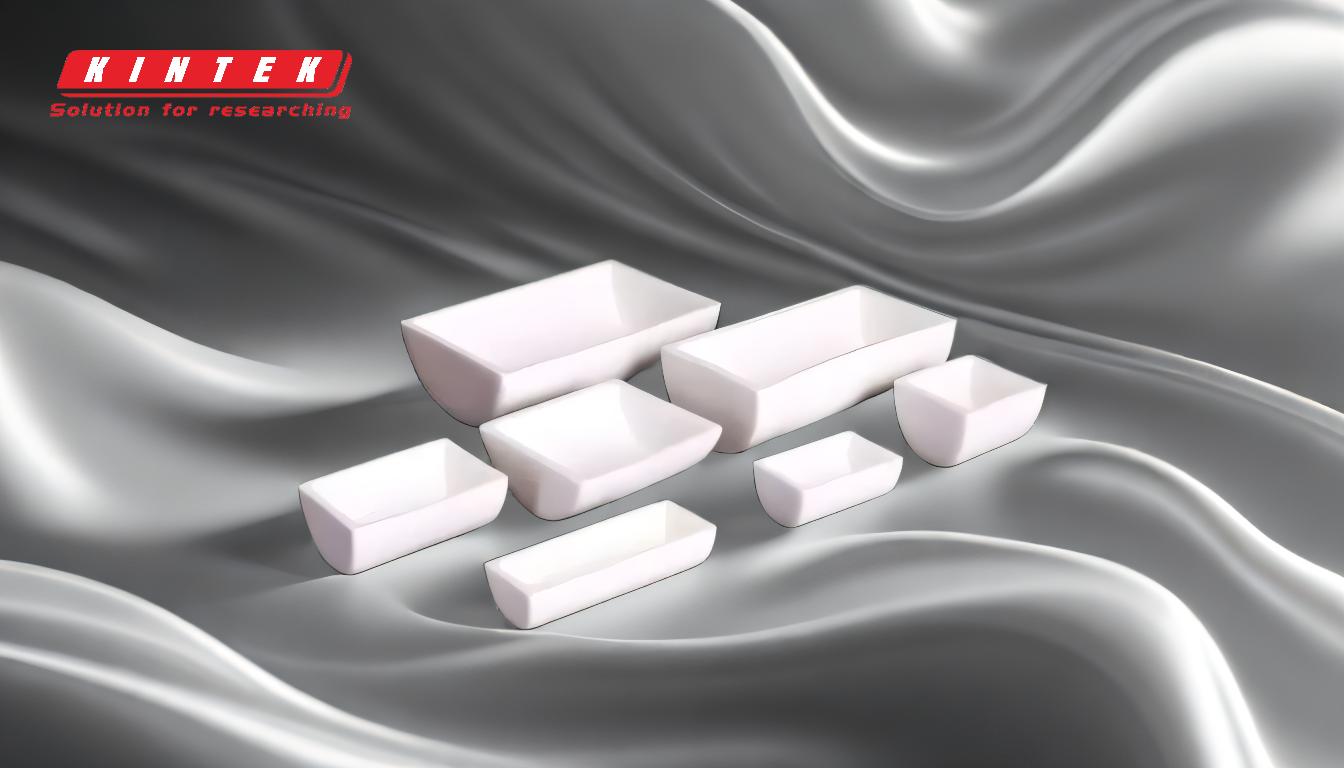
-
Fundamentals of Sputtering:
- Sputtering is a physical vapor deposition (PVD) process where atoms are ejected from a target material due to bombardment by high-energy particles, typically argon ions.
- The ejected atoms travel through a vacuum and deposit onto a substrate, forming a thin film.
- This process is widely used in industries requiring precise thin film deposition, such as semiconductors, optical devices, and solar panels.
-
Role of Plasma and Vacuum:
- The process begins in a vacuum chamber where a controlled gas, usually argon, is introduced.
- A cathode is electrically energized to generate a plasma, ionizing the argon gas.
- The positively charged argon ions are accelerated towards the target material, which acts as the cathode, due to an electrical field.
-
Ejection and Deposition:
- When the argon ions collide with the target material, they transfer their kinetic energy, causing atoms from the target to be ejected.
- These ejected atoms form a vapor stream that travels through the vacuum chamber.
- The atoms then condense on the substrate, forming a thin film or coating.
-
Magnetron Sputtering:
- Magnetron sputtering is an advanced form of sputtering that uses magnetic fields to enhance the efficiency of the process.
- The magnetic field traps electrons near the target, increasing the ionization of the argon gas and thus the rate of sputtering.
- This method offers high deposition rates and precise control, making it suitable for depositing dielectric and nitride films in microelectronics.
-
Deposition Rate and Control:
- The deposition rate, measured in thickness per unit time, is a critical factor in the sputtering process.
- High deposition rates are achievable with magnetron sputtering, which is beneficial for industrial applications requiring rapid production.
- Precise control over the deposition process ensures the creation of high-quality, dense films with minimal residual stress.
-
Applications and Advantages:
- Sputtering is used in the production of semiconductors, optical devices, CDs, and solar panels.
- The process is versatile, allowing for the deposition of a wide range of materials, including metals, alloys, and ceramics.
- It produces films with excellent adhesion, uniformity, and density, making it a preferred method for high-performance applications.
By understanding these key points, one can appreciate the complexity and precision involved in the sputtering process of evaporation, as well as its critical role in modern manufacturing and technology.
Summary Table:
Aspect | Details |
---|---|
Process | Physical vapor deposition (PVD) using high-energy argon ions. |
Key Components | Vacuum chamber, target material, substrate, plasma, and magnetic fields. |
Deposition Rate | High rates achievable with magnetron sputtering. |
Applications | Semiconductors, optical devices, solar panels, and microelectronics. |
Advantages | Precise control, high-quality films, excellent adhesion, and uniformity. |
Discover how sputtering can revolutionize your manufacturing process—contact us today!