Thin film deposition involves the application of a very thin layer of material onto a substrate, and the choice of substrate material is critical to the success of the process. The substrate material must be compatible with the deposition technique and the intended application. Common substrate materials include silicon, glass, metals, and polymers, each offering unique properties that make them suitable for specific uses. The selection of the substrate material depends on factors such as thermal stability, electrical conductivity, mechanical strength, and cost.
Key Points Explained:
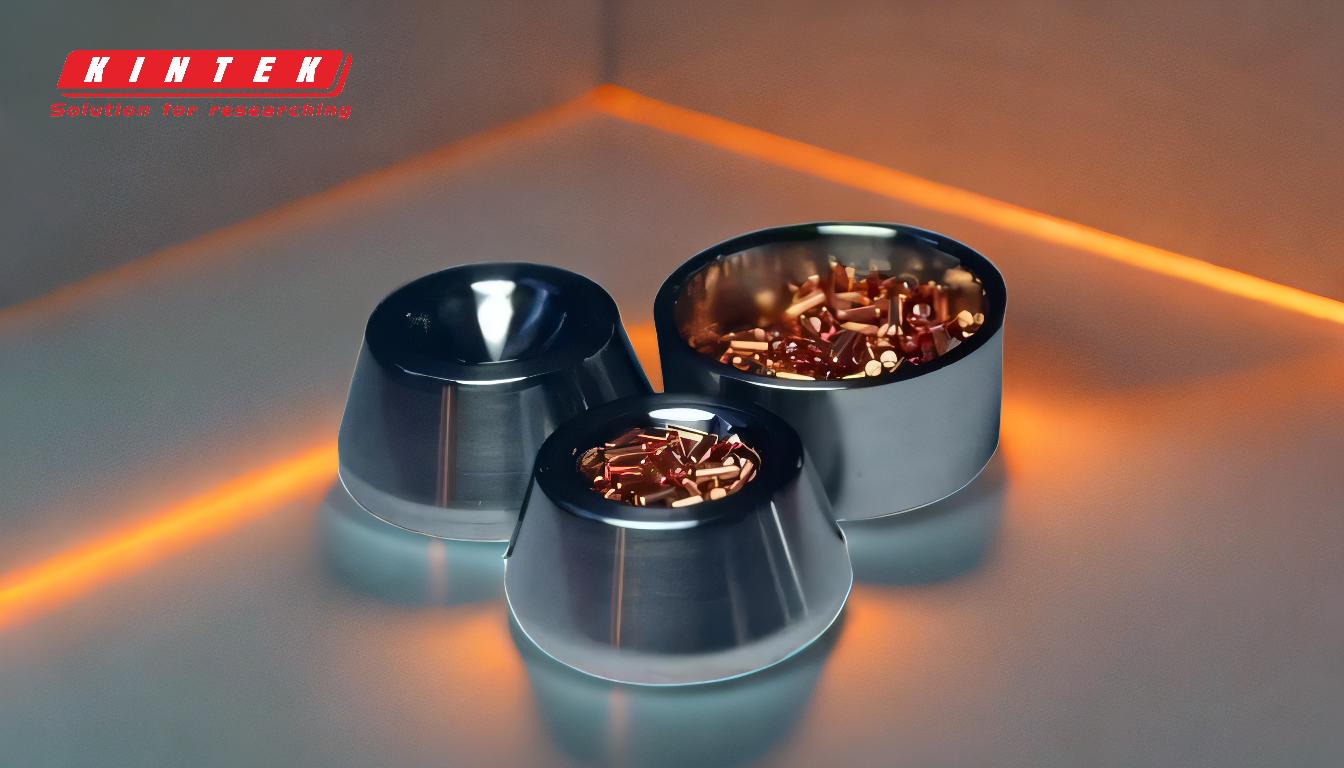
-
Silicon as a Substrate Material:
- Properties: Silicon is one of the most widely used substrate materials in thin film deposition, particularly in the semiconductor industry. It offers excellent thermal stability, high electrical conductivity, and compatibility with various deposition techniques.
- Applications: Silicon substrates are commonly used in the fabrication of integrated circuits, solar cells, and microelectromechanical systems (MEMS).
- Advantages: Silicon's high purity and uniformity make it ideal for applications requiring precise control over film thickness and composition.
- Disadvantages: Silicon substrates can be expensive, and their brittleness may limit their use in flexible or high-impact applications.
-
Glass as a Substrate Material:
- Properties: Glass substrates are known for their transparency, thermal stability, and chemical inertness. They are often used in applications where optical clarity is essential.
- Applications: Glass substrates are widely used in the production of display panels, optical coatings, and photovoltaic cells.
- Advantages: Glass is relatively inexpensive and can be easily shaped into various forms, making it versatile for different applications.
- Disadvantages: Glass is brittle and can be susceptible to thermal shock, which may limit its use in high-temperature or high-stress environments.
-
Metals as Substrate Materials:
- Properties: Metals such as aluminum, copper, and stainless steel are commonly used as substrate materials due to their high thermal and electrical conductivity, as well as their mechanical strength.
- Applications: Metal substrates are often used in the production of electronic components, reflective coatings, and corrosion-resistant layers.
- Advantages: Metals offer excellent durability and can withstand high temperatures, making them suitable for harsh environments.
- Disadvantages: Metals can be expensive, and their high thermal conductivity may lead to challenges in controlling the deposition process.
-
Polymers as Substrate Materials:
- Properties: Polymers, such as polyimide and polyethylene terephthalate (PET), are flexible, lightweight, and can be easily processed into thin films.
- Applications: Polymer substrates are commonly used in flexible electronics, wearable devices, and packaging materials.
- Advantages: Polymers are cost-effective and can be tailored to exhibit specific mechanical, thermal, and electrical properties.
- Disadvantages: Polymers generally have lower thermal stability compared to inorganic materials, which may limit their use in high-temperature applications.
-
Other Substrate Materials:
- Ceramics: Ceramics like alumina and zirconia are used in applications requiring high thermal and chemical stability.
- Composites: Composite materials, which combine the properties of different materials, are used in specialized applications where specific performance characteristics are needed.
- Advantages: These materials offer unique combinations of properties, such as high strength, thermal stability, and resistance to wear and corrosion.
- Disadvantages: They can be more expensive and difficult to process compared to more common substrate materials like silicon and glass.
In summary, the choice of substrate material for thin film deposition depends on the specific requirements of the application, including thermal stability, electrical conductivity, mechanical strength, and cost. Each material offers unique advantages and disadvantages, and the selection process involves careful consideration of these factors to ensure the success of the thin film deposition process.
Summary Table:
Substrate Material | Key Properties | Applications | Advantages | Disadvantages |
---|---|---|---|---|
Silicon | High thermal stability, electrical conductivity | Integrated circuits, solar cells, MEMS | High purity, uniformity | Expensive, brittle |
Glass | Transparency, thermal stability, inertness | Display panels, optical coatings, photovoltaic cells | Inexpensive, versatile | Brittle, susceptible to thermal shock |
Metals | High thermal/electrical conductivity, strength | Electronic components, reflective coatings, corrosion-resistant layers | Durable, withstands high temperatures | Expensive, challenges in deposition control |
Polymers | Flexibility, lightweight, processability | Flexible electronics, wearable devices, packaging materials | Cost-effective, customizable properties | Lower thermal stability |
Ceramics/Composites | High thermal/chemical stability, strength | Specialized applications requiring unique performance characteristics | High strength, wear/corrosion resistance | Expensive, difficult to process |
Need help selecting the perfect substrate material for your thin film deposition process? Contact our experts today for personalized guidance!