Sputter deposition is a widely used physical vapor deposition (PVD) technique for creating thin films on substrates. It involves bombarding a target material with high-energy ions (typically argon) in a vacuum environment, causing atoms from the target to be ejected and deposited onto a substrate. This process results in a dense, conformal, and well-adhered thin film. Sputter deposition is favored over other methods, such as thermal evaporation, due to its ability to produce high-quality coatings with better adhesion and uniformity. It is commonly used in industries like semiconductor manufacturing, optics, and solar cell production.
Key Points Explained:
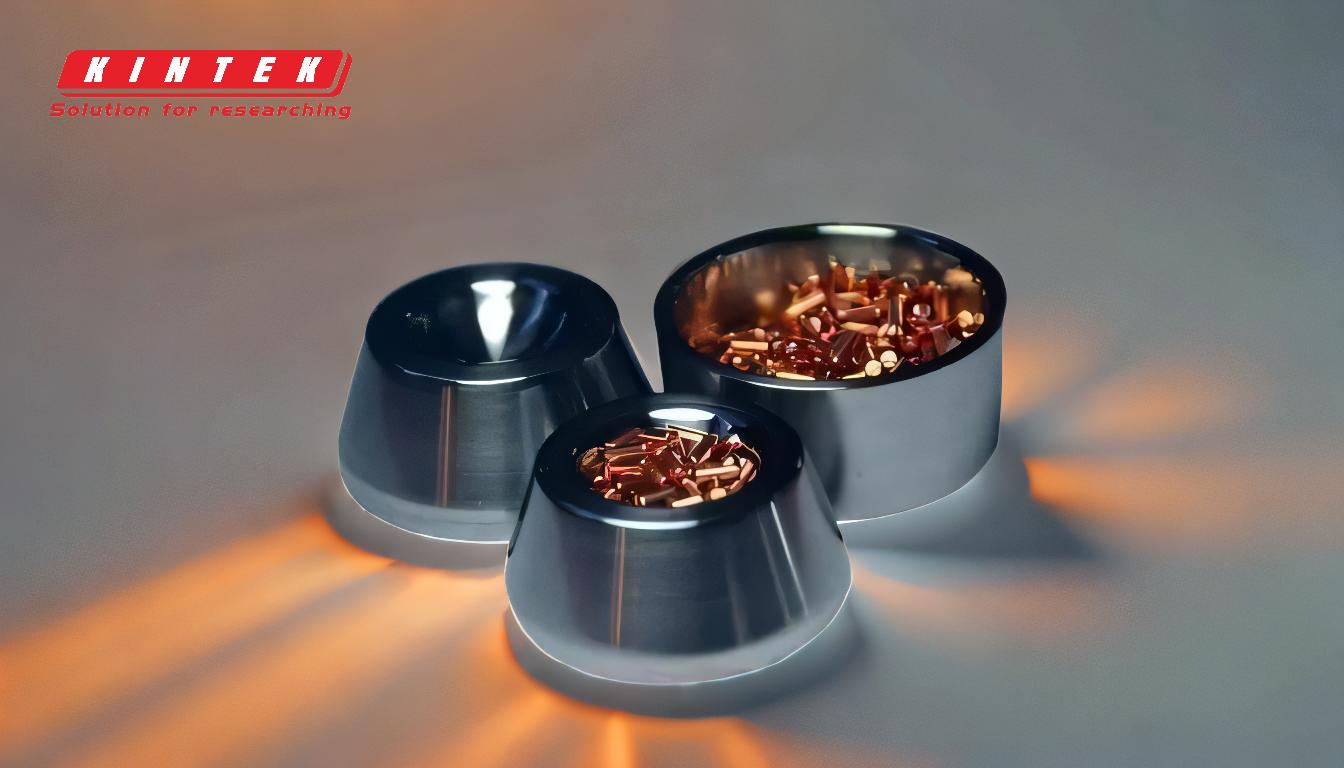
-
Basic Principle of Sputter Deposition:
- Sputter deposition is a PVD technique where a target material is bombarded with high-energy ions (usually argon) in a vacuum chamber.
- The energy from the ions ejects atoms from the target material, which then travel through the vacuum and deposit onto a substrate, forming a thin film.
- This process is driven by momentum transfer from the ions to the target atoms, a phenomenon known as sputtering.
-
Role of Plasma and Argon Gas:
- A plasma is created by ionizing an inert gas, typically argon, within the vacuum chamber.
- The positively charged argon ions are accelerated toward the negatively charged target material, causing the ejection of target atoms.
- The use of argon gas is preferred because it is inert and does not react chemically with the target or substrate.
-
Magnetron Sputtering:
- Magnetron sputtering is an advanced form of sputter deposition that uses magnetic fields to confine the plasma near the target surface.
- This confinement increases the density of the plasma, enhancing the sputtering rate and improving the efficiency of the process.
- Magnetron sputtering produces denser and more uniform thin films compared to traditional sputtering methods.
-
Advantages Over Thermal Evaporation:
- Sputter deposition produces films with better adhesion and density because the ejected atoms have higher kinetic energy.
- It allows for the deposition of a wider range of materials, including metals, alloys, and ceramics, which may be difficult to evaporate thermally.
- The process is more controllable and reproducible, making it suitable for industrial applications.
-
Applications of Sputter Deposition:
- Semiconductor Manufacturing: Used to deposit thin films of metals, insulators, and semiconductors on silicon wafers.
- Optical Coatings: Applied to create anti-reflective, reflective, or protective layers on lenses and mirrors.
- Solar Cells: Used to deposit conductive and anti-reflective layers for improved efficiency.
- Decorative Coatings: Applied to create durable and aesthetically pleasing finishes on consumer products.
-
Process Steps:
- Vacuum Creation: The chamber is evacuated to remove contaminants and create a clean environment.
- Plasma Generation: Argon gas is introduced and ionized to form a plasma.
- Target Bombardment: Argon ions bombard the target, ejecting atoms.
- Film Deposition: Ejected atoms travel through the vacuum and deposit onto the substrate, forming a thin film.
- Substrate Exposure: A shutter mechanism may be used to control the timing of deposition.
-
Resputtering Phenomenon:
- Resputtering occurs when deposited material on the substrate is re-emitted due to further ion bombardment.
- This can affect the uniformity and composition of the thin film, requiring careful control of process parameters.
-
Comparison with Other Deposition Methods:
- Unlike thermal evaporation, sputter deposition does not rely on heating the target material to its vaporization point.
- It provides better step coverage and conformality, making it ideal for coating complex geometries.
-
Key Considerations for Equipment and Consumables:
- Target Material: Must be of high purity and compatible with the desired film properties.
- Substrate Preparation: Proper cleaning and surface treatment are essential for good adhesion.
- Process Parameters: Factors like gas pressure, power, and substrate temperature must be optimized for specific applications.
Sputter deposition is a versatile and reliable technique for thin film deposition, offering advantages in terms of film quality, material compatibility, and process control. Its applications span a wide range of industries, making it a critical technology in modern manufacturing and research.
Summary Table:
Aspect | Details |
---|---|
Process | Bombarding a target with high-energy ions in a vacuum to deposit thin films. |
Key Advantages | Better adhesion, uniformity, and material compatibility. |
Applications | Semiconductors, optics, solar cells, and decorative coatings. |
Plasma Role | Argon gas ionized to create plasma for efficient sputtering. |
Magnetron Sputtering | Enhances sputtering rate and produces denser, uniform films. |
Ready to elevate your thin film processes? Contact our experts today for tailored solutions!