The temperature for a furnace varies significantly depending on the type of furnace and its intended application. Graphitization furnaces operate at extremely high temperatures, typically between 2500°C to 3000°C, to process carbonaceous materials in an inert atmosphere. Muffle furnaces, on the other hand, are designed for a wide range of high-temperature processes, with operating temperatures ranging from 800°C to 1800°C. These furnaces are commonly used for sintering, annealing, heat treatment, and melting metals. Additionally, the ambient temperature for operating furnace controllers is critical, typically limited to 0-40°C to ensure optimal performance and prevent damage to the equipment. Understanding the specific temperature requirements for each furnace type is essential for achieving desired outcomes and maintaining equipment longevity.
Key Points Explained:
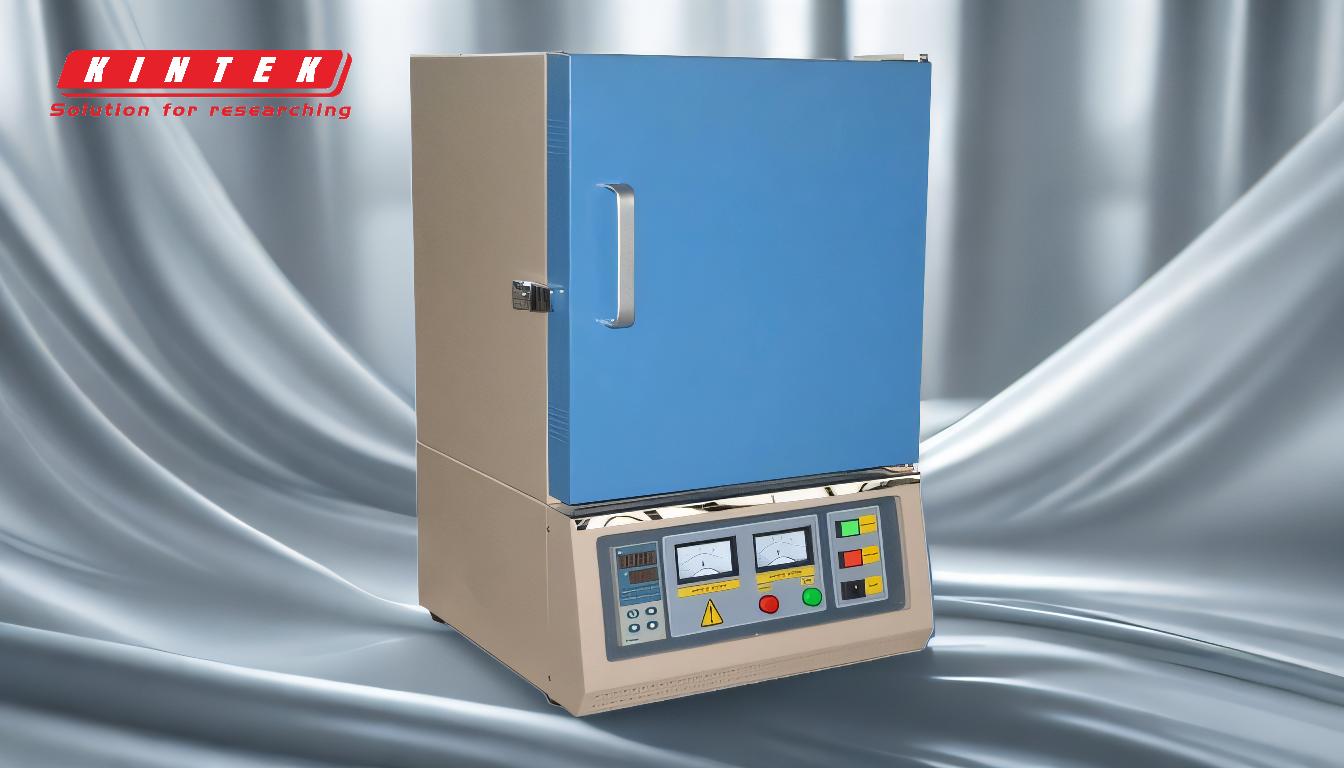
-
Graphitization Furnace Temperature Range:
- Graphitization furnaces operate at extremely high temperatures, typically between 2500°C to 3000°C.
- These temperatures are necessary to process carbonaceous materials, such as graphite, in a controlled inert atmosphere (e.g., argon or nitrogen) to prevent oxidation.
- This high-temperature range is unique to graphitization processes and is not suitable for other types of furnaces.
-
Muffle Furnace Temperature Range:
- Muffle furnaces are versatile and operate within a temperature range of 800°C to 1800°C.
- They are used for various high-temperature applications, including:
- Sintering: A process that bonds particles together without melting them.
- Annealing: Heat treatment to alter material properties, such as hardness or ductility.
- Melting and casting metals: Changing the physical characteristics of materials at elevated temperatures.
- The wide temperature range makes muffle furnaces suitable for both industrial and laboratory settings.
-
Ambient Temperature for Furnace Controllers:
- The ambient temperature for operating furnace controllers is critical and should be maintained between 0°C to 40°C.
- Operating outside this range can lead to malfunctions or damage to the controller, which may affect the furnace's performance.
- This temperature range ensures the longevity and reliability of the furnace's electronic components.
-
Sintering Furnace Temperature Considerations:
- Sintering furnaces must maintain temperatures below the melting point of the material being processed.
- The goal of sintering is to shape and bond materials without liquefying them, which requires precise temperature control.
- The temperature range for sintering typically falls between 800°C to 1800°C, depending on the material and application.
-
Maximum Temperature and Equipment Longevity:
- Furnaces should not exceed their rated maximum temperature to avoid damaging the electric heating elements.
- It is recommended to operate the furnace below 50°C of the maximum temperature to extend the life of the heating elements.
- This precaution helps prevent overheating and ensures consistent performance over time.
-
Applications of Specific Temperature Ranges:
- 500°C to 800°C: This range is commonly used for annealing and heat treatment processes, where materials are heated to alter their properties without reaching melting points.
- 800°C to 1800°C: This range is ideal for sintering, melting, and casting applications, where higher temperatures are required to achieve desired material transformations.
By understanding these key points, purchasers and operators can select the appropriate furnace type and temperature range for their specific applications, ensuring optimal results and equipment durability.
Summary Table:
Furnace Type | Temperature Range | Key Applications |
---|---|---|
Graphitization Furnace | 2500°C to 3000°C | Processing carbonaceous materials in an inert atmosphere (e.g., graphite production) |
Muffle Furnace | 800°C to 1800°C | Sintering, annealing, heat treatment, and melting metals |
Sintering Furnace | 800°C to 1800°C | Shaping and bonding materials without melting |
Ambient Temperature | 0°C to 40°C | Optimal range for furnace controllers to ensure performance and longevity |
Need help selecting the right furnace for your application? Contact our experts today for tailored advice!