The temperature of calcining, also known as calcination, typically ranges between 800°C and 1300°C, depending on the specific application and material being processed. For example, in limestone calcination, the temperature is often controlled within 1000°C to 1100°C due to factors such as the density, size, and impurities of the limestone. Calcination involves heating a substance in the presence of oxygen or air, or under limited air supply, to induce thermal decomposition. This process is carried out in specialized reactors called calciners or furnaces, which are designed to handle high temperatures and controlled conditions. The release of carbon dioxide is a common byproduct of calcination.
Key Points Explained:
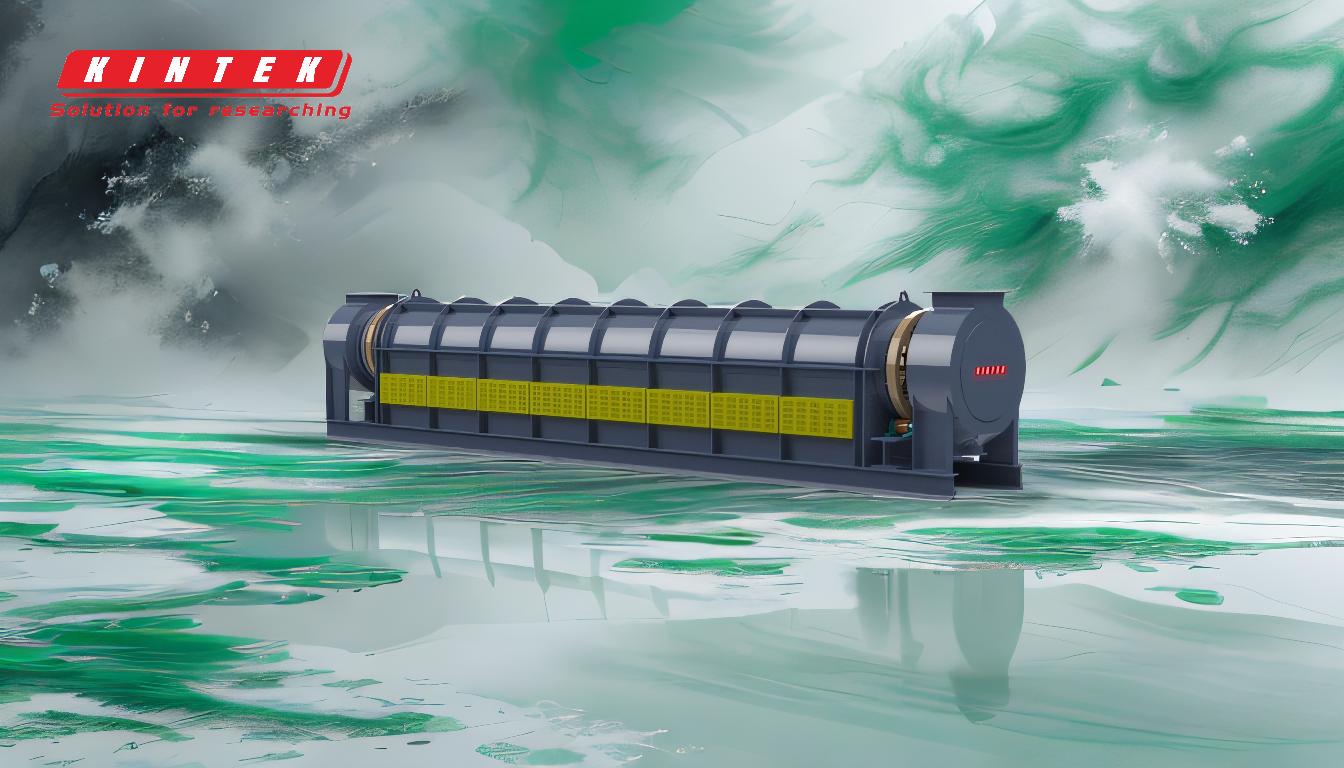
-
Definition of Calcination:
- Calcination is a thermal treatment process where a substance is heated to high temperatures, typically in the presence of oxygen or air, or under limited air supply.
- The process induces thermal decomposition, breaking down the material into simpler compounds or releasing volatile components.
-
Temperature Range for Calcination:
- The temperature for calcination generally ranges between 800°C and 1300°C.
- For limestone calcination, the temperature is often controlled within 1000°C to 1100°C due to variations in limestone density, block size, and impurities.
-
Factors Influencing Calcination Temperature:
- Material Properties: The composition, density, and size of the material being calcined influence the required temperature.
- Heat Loss: Practical considerations, such as heat loss during the process, may necessitate adjustments to the temperature range.
- Application-Specific Requirements: Different materials and industrial applications may require tailored temperature settings.
-
Equipment Used for Calcination:
- Calciners: Cylindrical reactors designed to handle high temperatures and controlled conditions for calcination.
- Furnaces: Sometimes used for calcination due to their ability to achieve and maintain the high temperatures required.
-
Byproducts of Calcination:
- During calcination, carbon dioxide (CO₂) is often released as a byproduct, particularly in processes like limestone calcination.
-
Industrial Applications:
- Calcination is widely used in industries such as cement production, metallurgy, and chemical manufacturing.
- The process is essential for transforming raw materials into usable products by removing impurities or altering their chemical structure.
By understanding these key points, an equipment or consumable purchaser can make informed decisions about the temperature settings and equipment needed for specific calcination processes.
Summary Table:
Key Aspect | Details |
---|---|
Temperature Range | 800°C to 1300°C (1000°C–1100°C for limestone) |
Factors Influencing Temp | Material properties, heat loss, application-specific requirements |
Equipment Used | Calciners, furnaces |
Byproducts | Carbon dioxide (CO₂) |
Industrial Applications | Cement production, metallurgy, chemical manufacturing |
Need help selecting the right equipment for calcination? Contact our experts today!