Microwave pyrolysis is a process that uses microwave radiation to heat biomass efficiently, reducing the initiation time of pyrolysis reactions and the overall energy required. The temperature range for microwave pyrolysis can vary depending on the specific application and feedstock, but it generally falls within the range of 350-700 °C. This temperature range is influenced by factors such as the nature of the feedstock, moisture content, heating rates, and residence time. Higher temperatures typically increase the production of non-condensable gases, while lower temperatures favor the production of high-quality solid products. The process is also affected by other variables like pressure, atmosphere, and feed rate, which can further influence the outcome of the pyrolysis.
Key Points Explained:
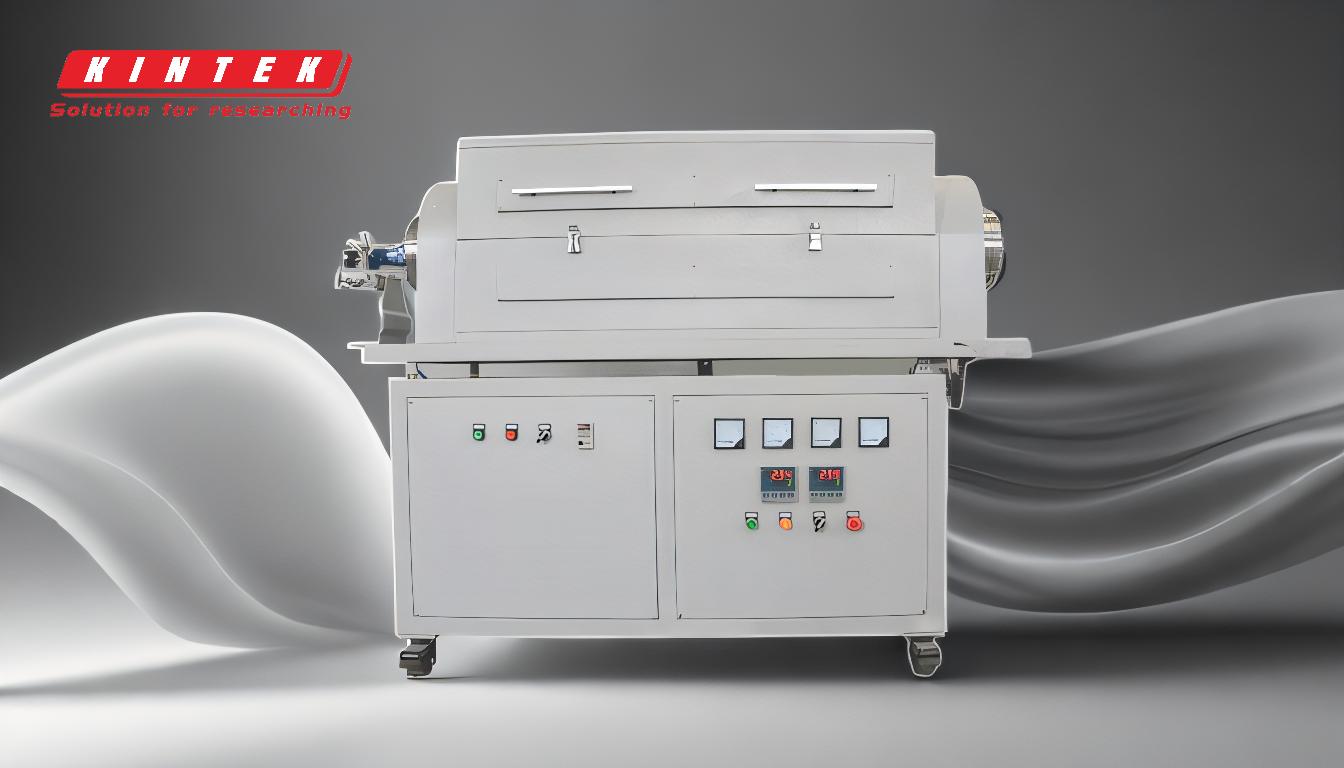
-
Temperature Range for Microwave Pyrolysis:
- Microwave pyrolysis typically operates within a temperature range of 350-700 °C.
- This range is influenced by the type of biomass or feedstock being processed, as well as the desired end products (e.g., gas, liquid, or solid).
- Higher temperatures (closer to 700 °C) are often used to maximize the production of non-condensable gases, while lower temperatures (around 350-400 °C) are better suited for producing high-quality solid products like biochar.
-
Factors Influencing Temperature in Microwave Pyrolysis:
- Feedstock Composition: Different materials decompose at different temperatures. For example, whole tires with fibers and steel may require higher temperatures compared to shredded tires with most steel removed.
- Moisture Content: Higher moisture content in the feedstock can affect the heating efficiency and may require adjustments in temperature.
- Heating Rates: Faster heating rates can reduce the overall energy required but may necessitate higher peak temperatures to achieve complete pyrolysis.
- Residence Time: Longer residence times at lower temperatures can achieve similar results to shorter times at higher temperatures, depending on the feedstock and desired products.
- Particle Size: Smaller particles heat more uniformly and quickly, which can influence the optimal temperature range.
-
Impact of Temperature on Pyrolysis Products:
-
Higher Temperatures (600-700 °C):
- Favor the production of non-condensable gases (e.g., syn-gas) and lighter liquid fractions.
- Increase the breakdown of complex organic molecules into simpler compounds.
-
Lower Temperatures (350-400 °C):
- Promote the formation of solid products like biochar and high-quality pyrolysis oil.
- Retain more of the original structure of the feedstock, which can be beneficial for certain applications.
-
Higher Temperatures (600-700 °C):
-
Comparison with Conventional Pyrolysis:
- Microwave pyrolysis is generally more efficient than conventional pyrolysis due to the direct and rapid heating provided by microwave radiation.
- The temperature range for microwave pyrolysis can be slightly lower than that of conventional pyrolysis, as microwaves can initiate reactions more quickly and at lower energy inputs.
- Conventional pyrolysis often requires higher external temperatures to achieve the same level of thermal decomposition.
-
Operational Considerations:
- Pressure: Atmospheric pressure is commonly used, but higher pressures can influence the temperature and product distribution.
- Atmosphere: The presence of inert gases (e.g., nitrogen) or reactive gases (e.g., oxygen) can affect the temperature requirements and product yields.
- Feed Rate: A consistent feed rate helps maintain stable temperatures within the pyrolysis reactor, ensuring uniform product quality.
-
Environmental and Energy Considerations:
- Microwave pyrolysis is energy-efficient, as it reduces the overall energy required for the process compared to traditional methods.
- The temperature control in microwave pyrolysis can also minimize unwanted by-products and reduce greenhouse gas emissions associated with the process.
In summary, the temperature of microwave pyrolysis is highly variable and depends on the specific application, feedstock, and desired outcomes. By carefully controlling factors such as heating rates, residence time, and particle size, operators can optimize the temperature to achieve the desired balance of gas, liquid, and solid products.
Summary Table:
Aspect | Details |
---|---|
Temperature Range | 350-700°C |
Key Influencing Factors | Feedstock composition, moisture content, heating rates, residence time, particle size |
Higher Temperatures | 600-700°C: Favors non-condensable gases and lighter liquid fractions |
Lower Temperatures | 350-400°C: Produces high-quality biochar and pyrolysis oil |
Comparison with Conventional Pyrolysis | More efficient, lower energy input, faster reactions |
Operational Considerations | Pressure, atmosphere, feed rate, and particle size influence outcomes |
Environmental Benefits | Energy-efficient, reduces greenhouse gas emissions, minimizes by-products |
Ready to optimize your biomass processing with microwave pyrolysis? Contact our experts today for tailored solutions!