The temperature of a burnout oven typically ranges from 500°C to 1,000°C, depending on the specific application and materials being processed. Burnout ovens are used in various industries, such as dental labs, jewelry making, and metal casting, to remove organic materials like wax or plastic from molds before they are filled with metal or ceramic. The temperature must be carefully controlled to ensure complete burnout of the organic material without damaging the mold or the final product. Understanding the temperature requirements is crucial for achieving optimal results in these processes.
Key Points Explained:
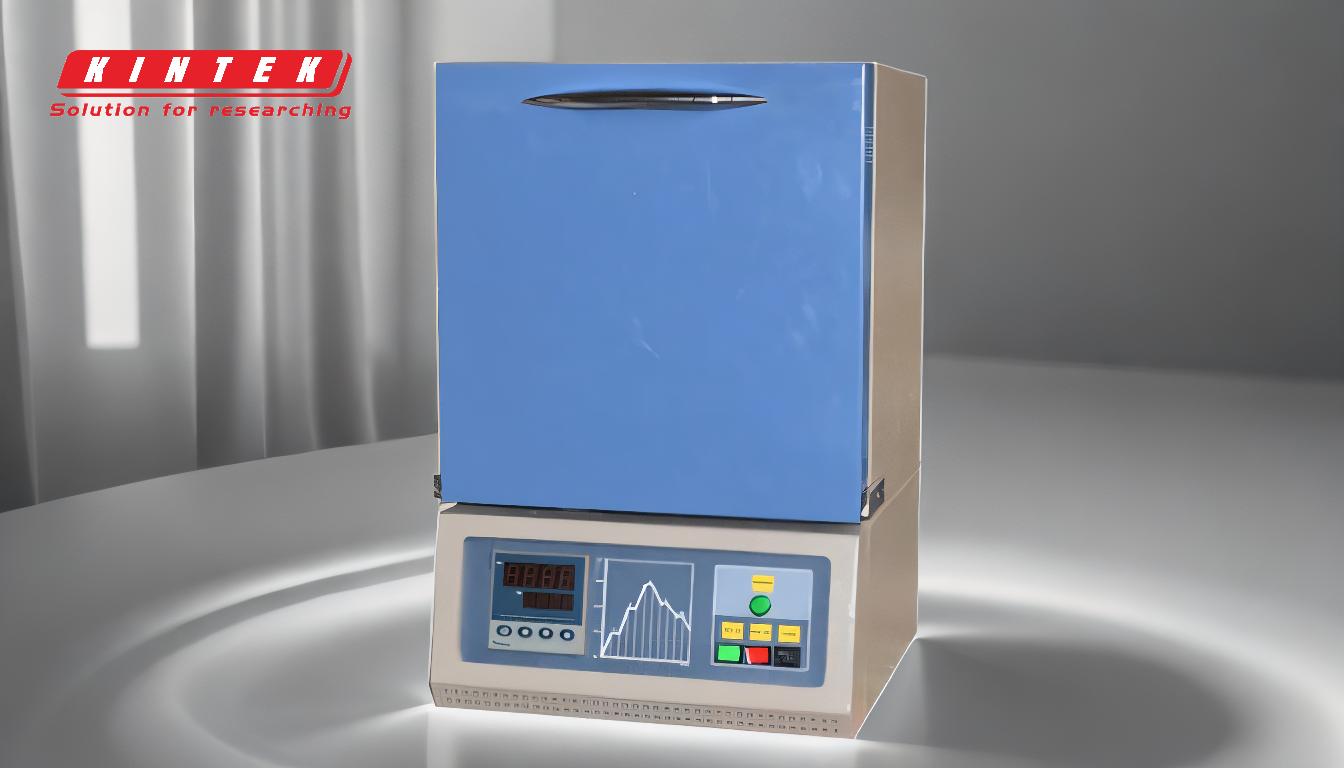
-
Temperature Range of Burnout Ovens:
- Burnout ovens generally operate within a temperature range of 500°C to 1,000°C. This range is selected based on the type of material being removed and the specific requirements of the process.
- For example, in dental labs, the temperature might be set around 850°C to 950°C to ensure complete wax burnout from the investment molds.
-
Applications of Burnout Ovens:
- Dental Labs: Used to remove wax patterns from investment molds before casting dental prosthetics.
- Jewelry Making: Employed to eliminate wax or resin from molds before metal casting.
- Metal Casting: Utilized in foundries to burn out organic binders from ceramic molds.
-
Importance of Temperature Control:
- Precise temperature control is essential to ensure that all organic materials are completely burned out. Incomplete burnout can lead to defects in the final product.
- Overheating can damage the mold or cause unwanted reactions, while underheating may leave residues that affect the quality of the cast.
-
Factors Influencing Temperature Settings:
- Material Type: Different materials require different burnout temperatures. For instance, wax burns out at lower temperatures compared to certain plastics.
- Mold Composition: The material of the mold itself can influence the required temperature. Ceramic molds can withstand higher temperatures than some other materials.
- Process Requirements: The specific requirements of the casting process, such as the type of metal being used, can also dictate the necessary burnout temperature.
-
Safety Considerations:
- Operating burnout ovens at high temperatures requires strict safety protocols to prevent accidents. Proper ventilation is necessary to remove fumes generated during the burnout process.
- Regular maintenance and calibration of the oven are crucial to ensure it operates within the desired temperature range and maintains safety standards.
-
Optimizing Burnout Processes:
- To achieve the best results, it's important to follow the manufacturer's guidelines for the specific burnout oven being used.
- Experimentation and experience can help in fine-tuning the temperature settings for different materials and molds, ensuring efficient and effective burnout.
Understanding the temperature requirements and operational nuances of burnout ovens is essential for anyone involved in processes that require the removal of organic materials from molds. Proper use and maintenance of these ovens can significantly impact the quality of the final product.
Summary Table:
Aspect | Details |
---|---|
Temperature Range | 500°C to 1,000°C, depending on material and application. |
Applications | Dental labs, jewelry making, metal casting. |
Key Factors | Material type, mold composition, process requirements. |
Safety Considerations | Proper ventilation, regular maintenance, and calibration are essential. |
Optimization Tips | Follow manufacturer guidelines and fine-tune settings for best results. |
Need help choosing the right burnout oven for your needs? Contact our experts today!