The temperature of a glass-melting furnace typically ranges between 1,500°C and 1,600°C (2,732°F to 2,912°F), depending on the type of glass being produced and the specific furnace design. Glass-melting furnaces are designed to maintain extremely high temperatures to melt raw materials like silica sand, soda ash, and limestone into molten glass. The temperature must be carefully controlled to ensure proper melting, homogenization, and refining of the glass. Continuous furnaces, as described in the reference, operate at permanent temperature conditions, which aligns with the need for consistent high heat in glass production.
Key Points Explained:
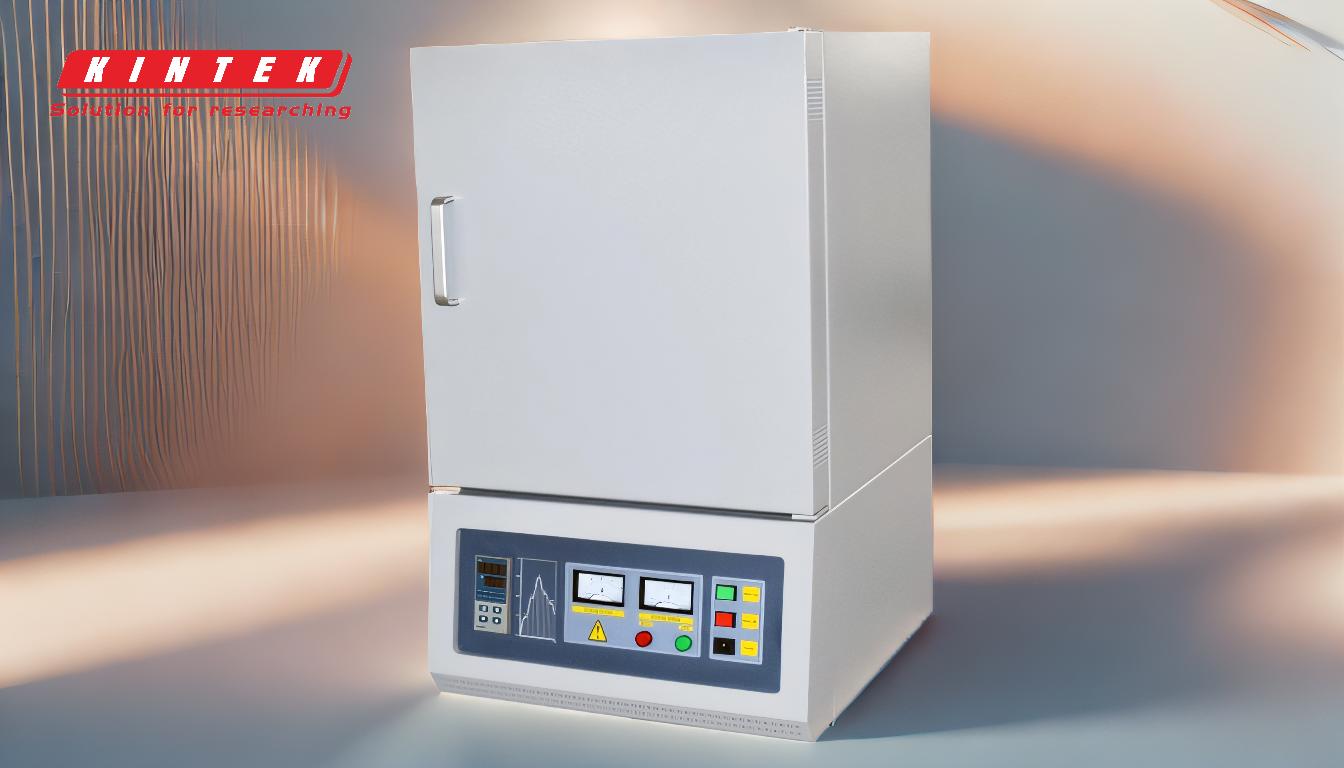
-
Temperature Range of Glass-Melting Furnaces:
- Glass-melting furnaces operate at temperatures between 1,500°C and 1,600°C (2,732°F to 2,912°F).
- This high temperature is necessary to melt raw materials like silica sand, soda ash, and limestone into a homogeneous molten state.
- The exact temperature depends on the type of glass being produced (e.g., soda-lime glass, borosilicate glass) and the furnace design.
-
Purpose of High Temperatures:
- Melting: Raw materials must be heated to their melting points to form a liquid glass mixture.
- Homogenization: High temperatures ensure that the molten glass is uniform in composition, free of bubbles, and ready for shaping.
- Refining: Impurities and gases are removed at these temperatures to produce clear, high-quality glass.
-
Continuous Furnace Operation:
- As mentioned in the reference, continuous furnaces operate at permanent temperature conditions.
- This is critical for glass production, as maintaining a consistent temperature ensures a steady flow of molten glass and consistent product quality.
- Continuous furnaces are ideal for large-scale glass production, where the same raw materials and processes are used repeatedly.
-
Factors Influencing Temperature:
- Glass Composition: Different types of glass require slightly different melting temperatures. For example, borosilicate glass, used in laboratory equipment, often requires higher temperatures than soda-lime glass.
- Furnace Design: The type of furnace (e.g., regenerative, recuperative, or electric) can influence the operating temperature and efficiency.
- Energy Source: Furnaces may use natural gas, electricity, or other fuels, which can affect the temperature control and distribution.
-
Temperature Control and Monitoring:
- Precise temperature control is essential to avoid underheating (which leads to incomplete melting) or overheating (which can damage the furnace or degrade the glass quality).
- Advanced furnaces use sensors and automated systems to monitor and adjust the temperature in real time.
-
Comparison to Other Furnaces:
- Unlike heat treatment furnaces for metals (e.g., annealing or hardening), glass-melting furnaces operate at much higher temperatures due to the unique properties of glass-forming materials.
- The reference highlights that continuous furnaces are specialized for specific processes, which applies to glass-melting furnaces as well.
By understanding these key points, a purchaser can better evaluate the specifications and capabilities of glass-melting furnaces, ensuring they meet the production requirements for their specific type of glass.
Summary Table:
Key Aspect | Details |
---|---|
Temperature Range | 1,500°C–1,600°C (2,732°F–2,912°F) |
Purpose of High Temperatures | Melting raw materials, homogenization, and refining impurities |
Furnace Operation | Continuous furnaces maintain permanent temperature for consistent quality |
Factors Influencing Temperature | Glass type, furnace design, and energy source |
Temperature Control | Real-time monitoring and automated systems ensure precision |
Ensure your glass production meets industry standards—contact our experts today for tailored solutions!