The temperature range for heat treatment of steel varies depending on the specific type of heat treatment being performed and the desired properties of the steel. Generally, heat treatment processes such as annealing, normalizing, quenching, and tempering involve heating the steel to specific temperatures within a range of approximately 150°C to 1200°C. These temperatures are carefully controlled to achieve the desired microstructure and mechanical properties, such as hardness, toughness, and ductility. The exact temperature range depends on factors like the steel's composition, the type of heat treatment, and the intended application.
Key Points Explained:
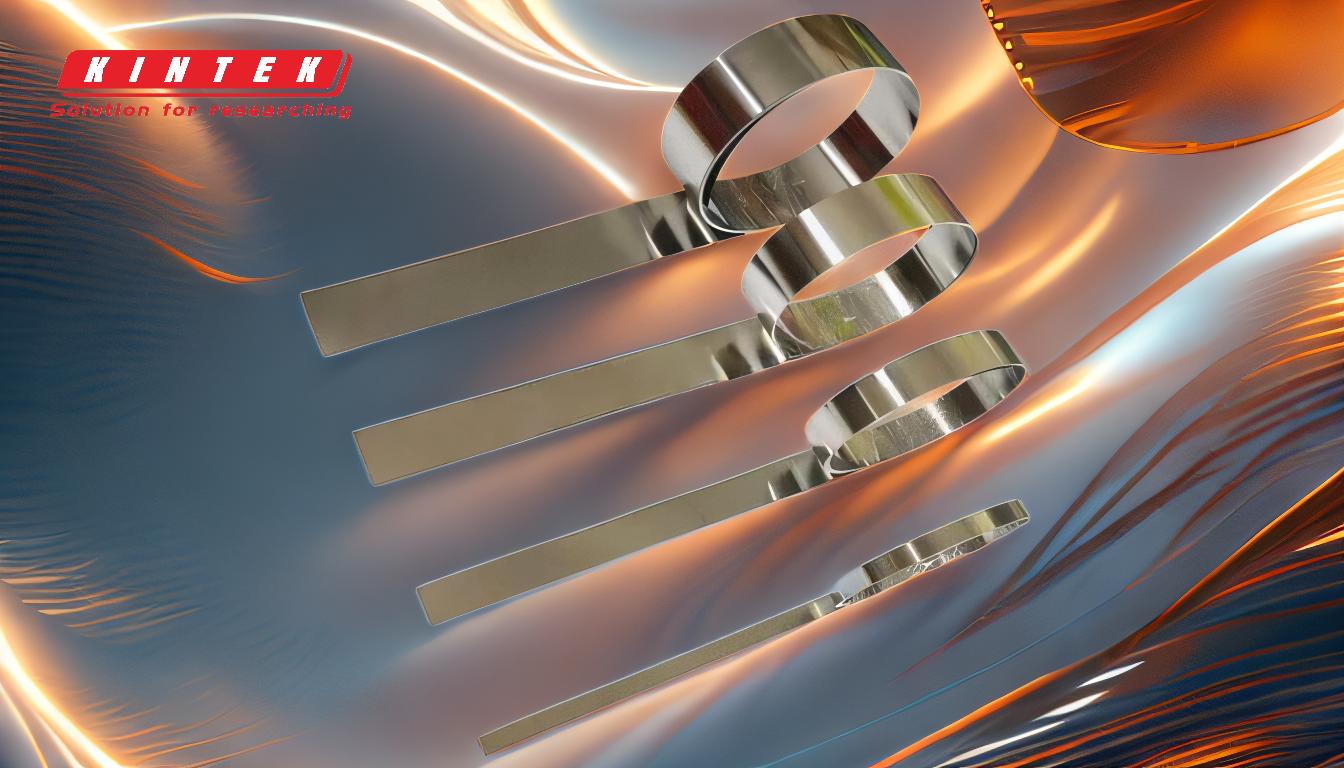
-
Types of Heat Treatment and Their Temperature Ranges:
- Annealing: This process involves heating the steel to a temperature between 700°C and 900°C, followed by slow cooling. The goal is to soften the steel, improve machinability, and relieve internal stresses.
- Normalizing: Steel is heated to a temperature slightly above the upper critical temperature (typically between 800°C and 950°C) and then air-cooled. This process refines the grain structure and improves mechanical properties.
- Quenching: The steel is heated to a temperature between 800°C and 950°C, depending on the steel type, and then rapidly cooled (usually in water, oil, or air) to achieve high hardness.
- Tempering: After quenching, the steel is reheated to a lower temperature (typically between 150°C and 650°C) to reduce brittleness and improve toughness while maintaining hardness.
-
Factors Influencing Temperature Selection:
- Steel Composition: The carbon content and alloying elements in the steel determine the critical temperatures and the appropriate heat treatment range.
- Desired Properties: The intended application of the steel (e.g., high strength, wear resistance, or ductility) dictates the heat treatment process and temperature.
- Cooling Rate: The cooling method (slow cooling for annealing, rapid cooling for quenching) affects the final microstructure and properties.
-
Importance of Temperature Control:
- Precise temperature control is critical to achieving the desired mechanical and microstructural properties. Overheating can lead to grain growth and reduced strength, while insufficient heating may not achieve the desired transformation.
-
Practical Considerations:
- Heat treatment furnaces must be capable of maintaining uniform temperatures within the required range. Advanced furnaces with digital controls and thermocouples ensure accuracy and consistency.
- Safety measures, such as proper ventilation and protective equipment, are essential when working with high-temperature processes.
By understanding the temperature ranges and their effects on steel properties, manufacturers can select the appropriate heat treatment process to meet specific application requirements.
Summary Table:
Heat Treatment Process | Temperature Range | Purpose |
---|---|---|
Annealing | 700°C - 900°C | Soften steel, improve machinability, relieve stress |
Normalizing | 800°C - 950°C | Refine grain structure, enhance mechanical properties |
Quenching | 800°C - 950°C | Achieve high hardness through rapid cooling |
Tempering | 150°C - 650°C | Reduce brittleness, improve toughness |
Need help selecting the right heat treatment process for your steel? Contact our experts today!