The temperature range of arc heating is primarily influenced by the high-energy electric discharge that occurs during the process. While the substrate temperature can remain relatively low (below 100°C), the arc itself generates extremely high temperatures, often exceeding 3000°C in the arc area. This high temperature is due to the concentration of energy in the gas during the electric discharge, which is a key characteristic of arc technology. Below is a detailed explanation of the temperature range and its implications.
Key Points Explained:
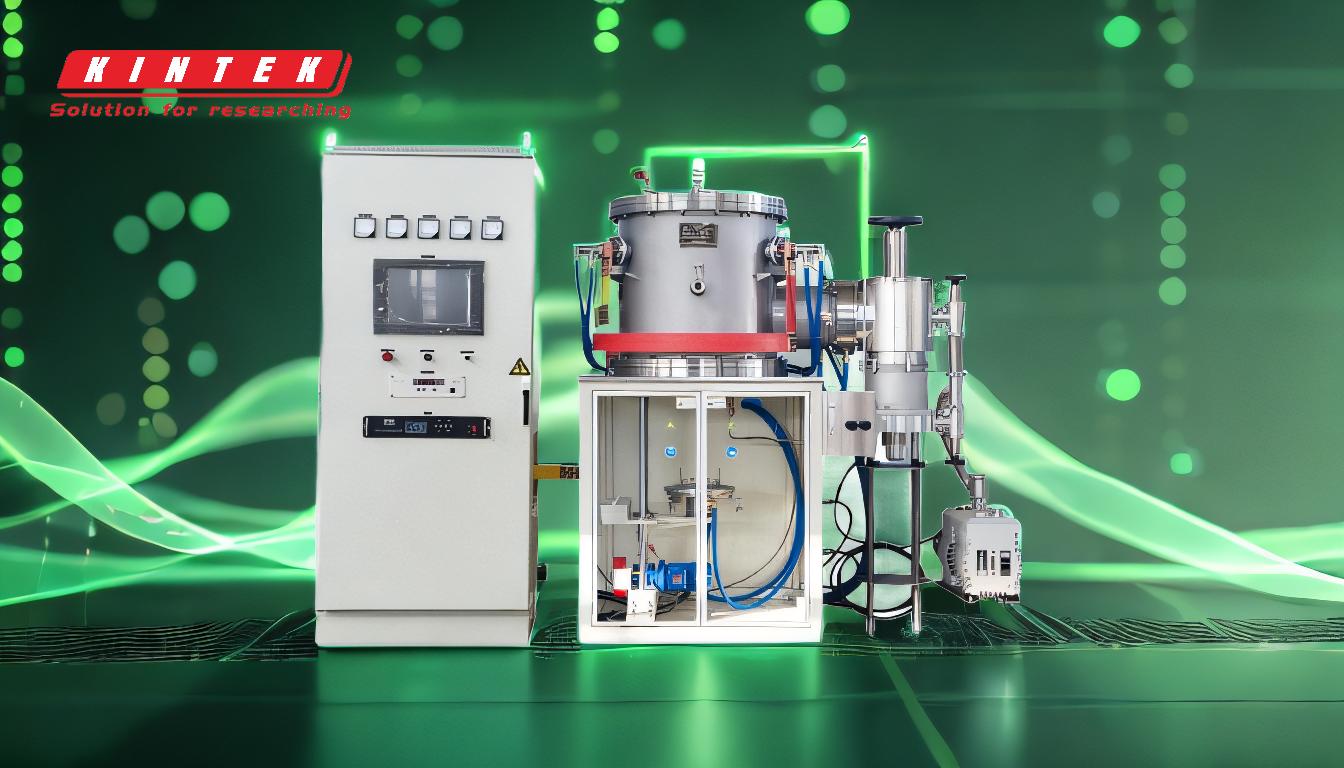
-
Substrate Temperature During Arc Heating
- The substrate temperature during arc heating is typically maintained below 100°C.
- This is a significant advantage of arc technology, as it minimizes thermal damage to the substrate, making it suitable for temperature-sensitive materials.
- The low substrate temperature is achieved due to the localized nature of the arc heating process, where heat generation is concentrated in the arc area rather than the entire substrate.
-
Arc Temperature During Electric Discharge
- The temperature in the arc area during electric discharge exceeds 3000°C.
- This extreme temperature is a result of the high energy concentration in the gas during the arc formation.
- The high temperature is essential for processes like metal evaporation, ionization, and the formation of dense coatings with good adhesion properties.
-
Implications of High Arc Temperature
- The high temperature in the arc area enables the evaporation of various metal compositions without altering the remaining solid target's composition.
- It ensures high ionization rates, which contribute to the formation of dense and well-adhered coatings.
- The flexibility in machine design, such as the ability to place cathodes in any position, is also a result of the localized high-temperature arc.
-
Balancing High Arc Temperature and Low Substrate Temperature
- The ability to maintain a low substrate temperature while achieving high arc temperatures is a unique feature of arc heating.
- This balance is achieved through precise control of the arc discharge and the use of cooling mechanisms to prevent heat transfer to the substrate.
- It makes arc heating suitable for applications requiring high-quality coatings on temperature-sensitive materials.
-
Applications of Arc Heating
- Arc heating is widely used in industries requiring high deposition rates and dense coatings, such as aerospace, automotive, and tool manufacturing.
- The low substrate temperature makes it ideal for coating materials that cannot withstand high thermal stress.
- The high arc temperature ensures efficient material evaporation and ionization, resulting in superior coating properties.
In summary, the temperature range of arc heating is characterized by two distinct zones: the high-temperature arc area (exceeding 3000°C) and the low-temperature substrate (below 100°C). This combination of extreme heat in the arc and minimal thermal impact on the substrate is a defining feature of arc technology, enabling its use in a wide range of industrial applications.
Summary Table:
Aspect | Details |
---|---|
Substrate Temperature | Below 100°C, ideal for temperature-sensitive materials. |
Arc Temperature | Exceeds 3000°C, enabling metal evaporation and dense coating formation. |
Key Benefits | High ionization rates, precise control, and minimal thermal damage. |
Applications | Aerospace, automotive, tool manufacturing, and temperature-sensitive coatings. |
Learn how arc heating can enhance your industrial processes—contact our experts today!