A rotary kiln typically consists of multiple temperature zones designed to facilitate specific thermal processes. The primary zones include the pre-heating zone and the high-temperature heating zone. These zones are essential for ensuring that materials undergo the necessary chemical and physical transformations as they move through the kiln. Each zone can be independently controlled to meet precise process requirements, allowing for optimal heat distribution and efficiency. The design and operation of these zones are influenced by factors such as the type of material being processed, the desired end product, and the specific reactions that need to occur at different stages of the heating process.
Key Points Explained:
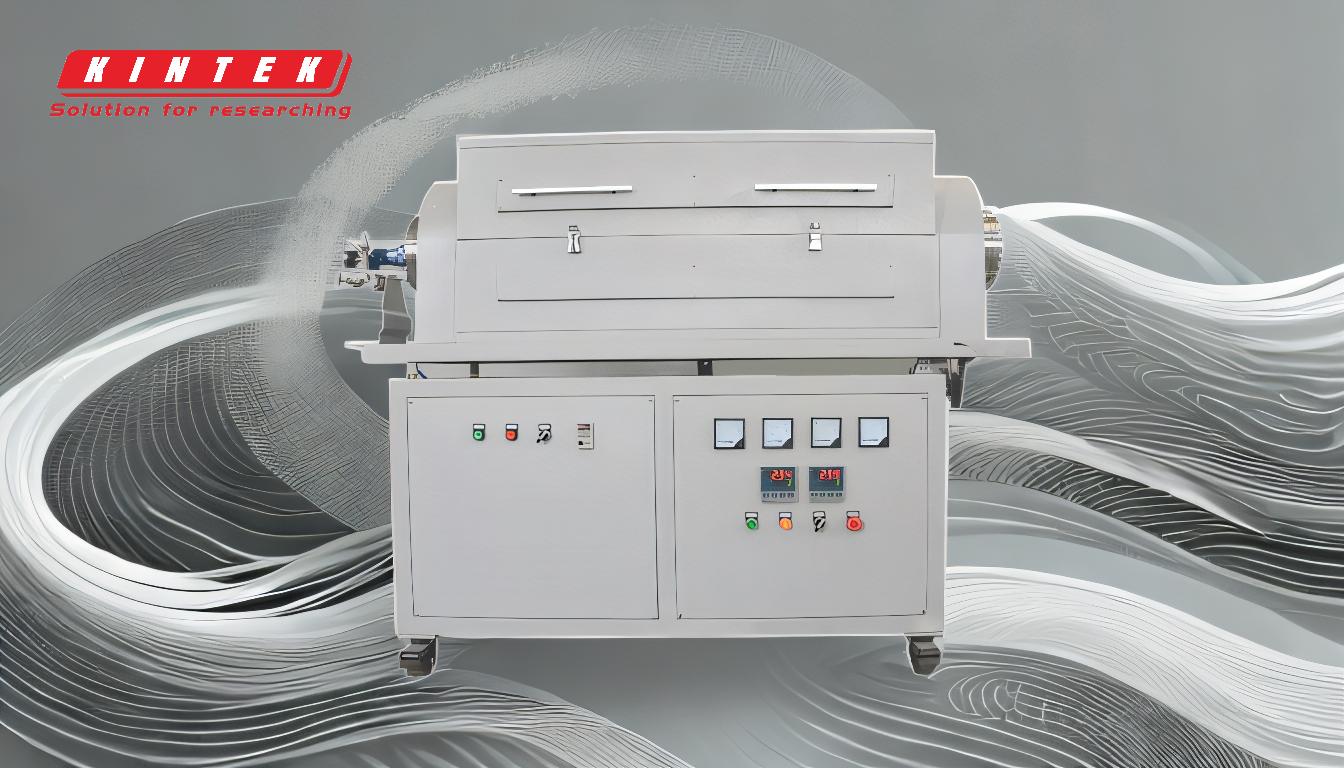
-
Pre-Heating Zone:
- Purpose: The pre-heating zone is the initial stage where materials are gradually heated to prepare them for the high-temperature reactions in the subsequent zones.
- Temperature Range: The temperature in this zone is typically lower compared to the high-temperature heating zone, often ranging from ambient temperature to several hundred degrees Celsius.
- Function: This zone helps to remove moisture, volatiles, and other impurities from the material, ensuring that it is properly conditioned before entering the high-temperature zone.
-
High-Temperature Heating Zone:
- Purpose: This is the core zone where the primary thermal reactions occur, such as calcination, sintering, or pyrolysis.
- Temperature Range: The temperature in this zone can reach very high levels, often exceeding 1000°C, depending on the material and the specific process requirements.
- Function: The high-temperature heating zone is critical for driving the necessary chemical reactions that transform the raw material into the desired product. The temperature and residence time in this zone are carefully controlled to achieve the desired outcome.
-
Multiple Temperature Zones:
- Customization: Both the pre-heating and high-temperature heating zones can be divided into multiple sub-zones, each with its own temperature setting. This allows for precise control over the heating profile, ensuring that the material is heated uniformly and efficiently.
- Process Optimization: The ability to set different temperatures in various zones enables the optimization of the overall process, leading to better product quality and energy efficiency.
-
Control and Monitoring:
- Temperature Control: Advanced rotary kilns are equipped with sophisticated control systems that allow operators to monitor and adjust the temperature in each zone in real-time. This ensures that the process remains within the desired parameters and any deviations are quickly corrected.
- Feedback Mechanisms: Sensors and feedback mechanisms are often integrated into the kiln to provide continuous data on the temperature profile, enabling precise adjustments and ensuring consistent product quality.
-
Design Considerations:
- Kiln Geometry: The size and shape of the kiln, including the diameter, length, and aspect ratio, play a significant role in determining the temperature distribution and residence time of the material. Internal fixtures like constriction dams and lifters can also influence the temperature profile by affecting the material flow and heat transfer.
- Heat Distribution: The placement of heaters around the kiln (360° heater placement) ensures even heat transmission, which is crucial for maintaining uniform temperatures across the different zones.
-
Operational Requirements:
- Material Properties: The type of material being processed, its thermal conductivity, and its reaction kinetics are key factors that influence the temperature settings in each zone.
- Process Parameters: Operational parameters such as feed rate, rotational speed, and kiln loading (% fill) must be carefully managed to ensure that the material is exposed to the correct temperature profile throughout its journey in the kiln.
In summary, the temperature zones in a rotary kiln are carefully designed and controlled to facilitate the specific thermal processes required for transforming raw materials into finished products. The pre-heating and high-temperature heating zones, along with their sub-zones, are essential components that ensure efficient and effective heat treatment, leading to high-quality end products.
Summary Table:
Zone | Purpose | Temperature Range | Function |
---|---|---|---|
Pre-Heating Zone | Gradually heats materials to prepare for high-temperature reactions | Ambient to several hundred °C | Removes moisture, volatiles, and impurities for proper conditioning |
High-Temperature Zone | Drives primary thermal reactions like calcination, sintering, or pyrolysis | Often exceeds 1000°C | Transforms raw materials into desired products through precise heat control |
Multiple Sub-Zones | Customizable temperature settings for uniform heating and process optimization | Varies by application | Ensures efficient heat distribution and energy efficiency |
Discover how rotary kiln temperature zones can enhance your thermal processes—contact our experts today for tailored solutions!