Pyrolysis is a thermochemical process where complex materials are thermally degraded in the absence of oxygen, leading to the breakdown of larger molecules into smaller, volatile fragments. This process generates a variety of products, including gases (syngas), liquids (bio-oil), and solids (bio-char), depending on the material and conditions used. Pyrolysis is widely applied in converting biomass, plastics, and other waste materials into useful products, thereby reducing waste and generating valuable outputs. The process is energy-intensive and requires precise control of temperature and atmosphere to optimize product yield and quality.
Key Points Explained:
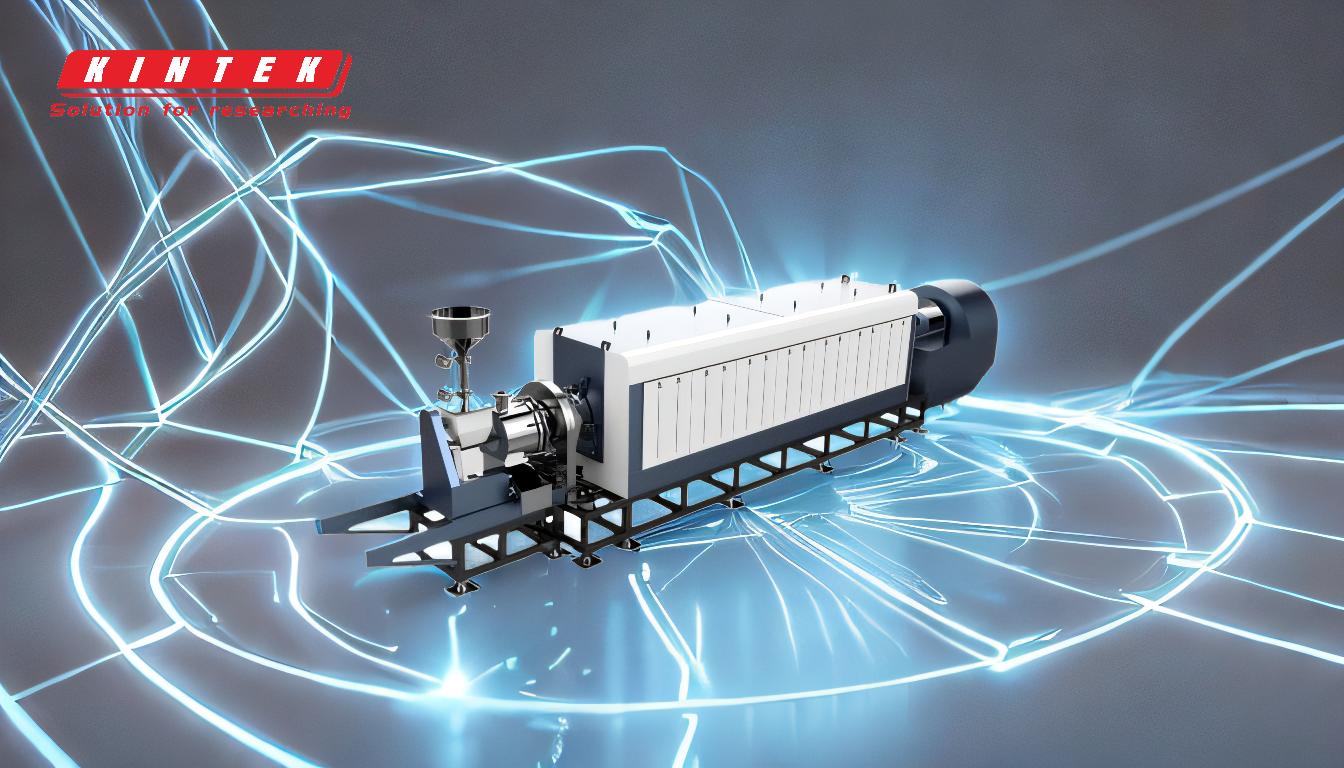
-
Definition and Etymology of Pyrolysis:
- Pyrolysis is derived from the Greek words 'pyro' (fire or heat) and 'lysis' (separation), meaning the breakdown of materials using heat.
- It involves the thermal decomposition of materials at elevated temperatures, typically between 400-900°C, in the absence of oxygen.
-
Mechanism of Pyrolysis:
- The process begins with heating the material above its decomposition temperature, causing chemical bonds to break.
- This results in the formation of smaller molecules or residues with larger molecular mass.
- The absence of oxygen prevents combustion, allowing for the controlled breakdown of the material.
-
Products of Pyrolysis:
- Gases (Syngas): Includes hydrogen, carbon monoxide, and methane, which can be used as fuel or chemical feedstocks.
- Liquids (Bio-oil): A mixture of water and volatile organic compounds, useful as a renewable fuel or for chemical production.
- Solids (Bio-char): Carbon-rich materials that can be used as soil amendments or for carbon sequestration.
-
Applications of Pyrolysis:
- Biomass Conversion: Converts agricultural and forestry residues into bio-oil, syngas, and bio-char.
- Plastic and Tire Recycling: Breaks down plastics and tires into valuable oils and gases, reducing landfill waste.
- Hazardous Waste Treatment: Safely decomposes hazardous materials into less harmful substances.
-
Process Conditions and Control:
- Temperature: Critical for determining the composition and yield of pyrolysis products. Higher temperatures favor gas production, while lower temperatures favor liquid and solid products.
- Atmosphere: Typically an inert atmosphere (e.g., nitrogen) or vacuum is used to prevent oxidation and side reactions.
- Catalysts: In catalytic pyrolysis, catalysts are used to enhance the breakdown of materials and improve product quality.
-
Energy Requirements and Challenges:
- Pyrolysis is energy-intensive, requiring significant heat input to achieve the necessary temperatures.
- The process must be carefully controlled to optimize product yields and minimize energy consumption.
- Challenges include managing the variability of feedstocks and ensuring the economic viability of the process.
-
Comparison to Other Processes:
- Thermal Cracking: Similar to pyrolysis but operates at lower temperatures and is used in petroleum refining.
- Combustion: Involves burning materials in the presence of oxygen, producing heat and CO2, unlike pyrolysis which avoids combustion.
- Hydrolysis: Involves breaking down materials using water, which is different from the thermal decomposition in pyrolysis.
-
Environmental and Economic Benefits:
- Waste Reduction: Converts waste materials into useful products, reducing landfill use and environmental pollution.
- Resource Recovery: Generates valuable products like bio-oil and syngas, which can replace fossil fuels.
- Carbon Sequestration: Bio-char can be used to sequester carbon in soils, contributing to climate change mitigation.
By understanding these key points, purchasers of equipment and consumables can better evaluate the suitability of pyrolysis technology for their specific needs, considering factors like feedstock type, desired products, and process conditions.
Summary Table:
Aspect | Details |
---|---|
Definition | Thermal decomposition of materials at 400-900°C in the absence of oxygen. |
Products | Gases (syngas), liquids (bio-oil), and solids (bio-char). |
Applications | Biomass conversion, plastic recycling, hazardous waste treatment. |
Key Factors | Temperature, atmosphere, and catalysts determine product yield and quality. |
Benefits | Waste reduction, resource recovery, and carbon sequestration. |
Discover how pyrolysis can transform your waste into valuable resources—contact us today for expert guidance!