Thermal evaporation in a vacuum is a widely used thin-film deposition technique where a solid material is heated in a high-vacuum environment until it reaches its evaporation point, producing a vapor stream. This vapor stream travels through the vacuum chamber and condenses onto a substrate, forming a thin film. The process relies on heating the material using resistive heating elements like boats or coils, which generate heat through electrical resistance. The vacuum environment ensures minimal contamination and allows the vaporized particles to travel unimpeded to the substrate. This method is commonly used in industries like electronics, optics, and coatings due to its simplicity and ability to produce high-purity films.
Key Points Explained:
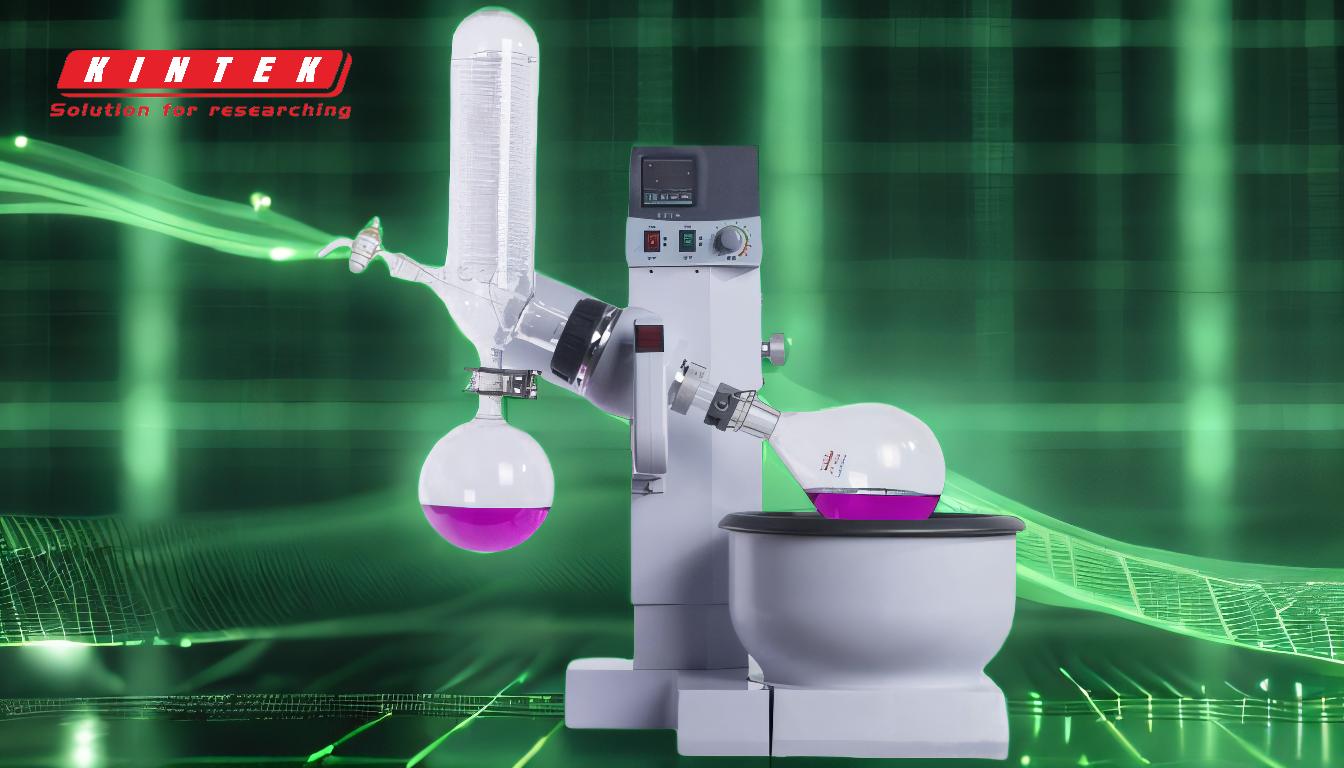
-
Basic Principle of Thermal Evaporation:
- Thermal evaporation involves heating a solid material in a high-vacuum chamber until it reaches its evaporation point.
- The material gains sufficient thermal energy to break atomic bonds, releasing atoms or molecules into the vapor phase.
- The vapor stream travels through the vacuum and deposits onto a substrate, forming a thin film.
-
Role of Vacuum Environment:
- A high-vacuum environment is critical for thermal evaporation as it minimizes the presence of contaminants and ensures the vaporized particles travel unimpeded.
- The vacuum reduces collisions between vaporized particles and residual gas molecules, ensuring a clean and uniform deposition process.
-
Heating Mechanism:
- The material is heated using resistive heating elements such as boats, coils, or baskets.
- An electric current passes through these elements, generating heat through electrical resistance.
- The heat melts and evaporates the material, producing a vapor stream.
-
Evaporation Source Types:
- Boats: Typically made of refractory metals like tungsten or molybdenum, boats hold the material and heat it uniformly.
- Coils: Wire coils are used to hold and heat the material, often for materials with lower melting points.
- Baskets: These are used for materials that require more controlled heating or are difficult to handle in boats or coils.
-
Vaporization and Deposition:
- As the material is heated, it transitions from a solid to a vapor phase.
- The vaporized particles travel through the vacuum chamber and condense onto the substrate, forming a thin film.
- The deposition process is controlled by factors like temperature, evaporation rate, and substrate position.
-
Applications of Thermal Evaporation:
- Electronics: Used for depositing conductive and insulating layers in semiconductor devices.
- Optics: Applied in the production of reflective and anti-reflective coatings for lenses and mirrors.
- Coatings: Used for decorative and protective coatings on various materials.
-
Advantages of Thermal Evaporation:
- High Purity: The vacuum environment ensures minimal contamination, resulting in high-purity films.
- Simplicity: The process is relatively simple and cost-effective compared to other deposition techniques.
- Versatility: Can be used with a wide range of materials, including metals, alloys, and some organic compounds.
-
Limitations of Thermal Evaporation:
- Material Compatibility: Not all materials can be evaporated due to high melting points or decomposition at elevated temperatures.
- Uniformity Challenges: Achieving uniform thickness across large substrates can be difficult.
- Step Coverage: Poor step coverage compared to other techniques like sputtering or chemical vapor deposition (CVD).
-
Process Control Parameters:
- Temperature: Must be precisely controlled to ensure consistent evaporation rates.
- Vacuum Level: A high vacuum (typically 10^-6 to 10^-7 Torr) is required for optimal performance.
- Substrate Position and Orientation: Affects film uniformity and adhesion.
-
Comparison with Other Deposition Techniques:
- Sputtering: Offers better step coverage and can handle materials with higher melting points but is more complex and expensive.
- Chemical Vapor Deposition (CVD): Provides excellent uniformity and conformality but requires reactive gases and higher temperatures.
- Thermal Evaporation: Simpler and more cost-effective but limited by material compatibility and uniformity challenges.
By understanding these key points, a purchaser or user of thermal evaporation equipment can make informed decisions about its suitability for specific applications and optimize the process for desired outcomes.
Summary Table:
Key Aspect | Details |
---|---|
Basic Principle | Heating a solid material in a vacuum until it evaporates and forms a thin film. |
Vacuum Environment | Ensures minimal contamination and unimpeded vapor travel. |
Heating Mechanism | Resistive heating elements (boats, coils, baskets) generate heat. |
Applications | Electronics, optics, coatings. |
Advantages | High purity, simplicity, versatility. |
Limitations | Material compatibility, uniformity challenges, poor step coverage. |
Process Control | Temperature, vacuum level, substrate position. |
Discover how thermal evaporation can enhance your thin-film processes—contact our experts today!