Silicon Carbide (SiC) is a ceramic material known for its excellent thermal, mechanical, and chemical properties. One of its standout features is its low coefficient of thermal expansion, which is approximately 4.0 × 10⁻⁶/°C. This low thermal expansion, combined with its high thermal conductivity and mechanical strength, makes SiC highly resistant to thermal shock and suitable for high-temperature applications. Its ability to maintain structural integrity at temperatures up to 1400°C, and even approaching 1600°C without significant strength loss, further underscores its utility in demanding environments.
Key Points Explained:
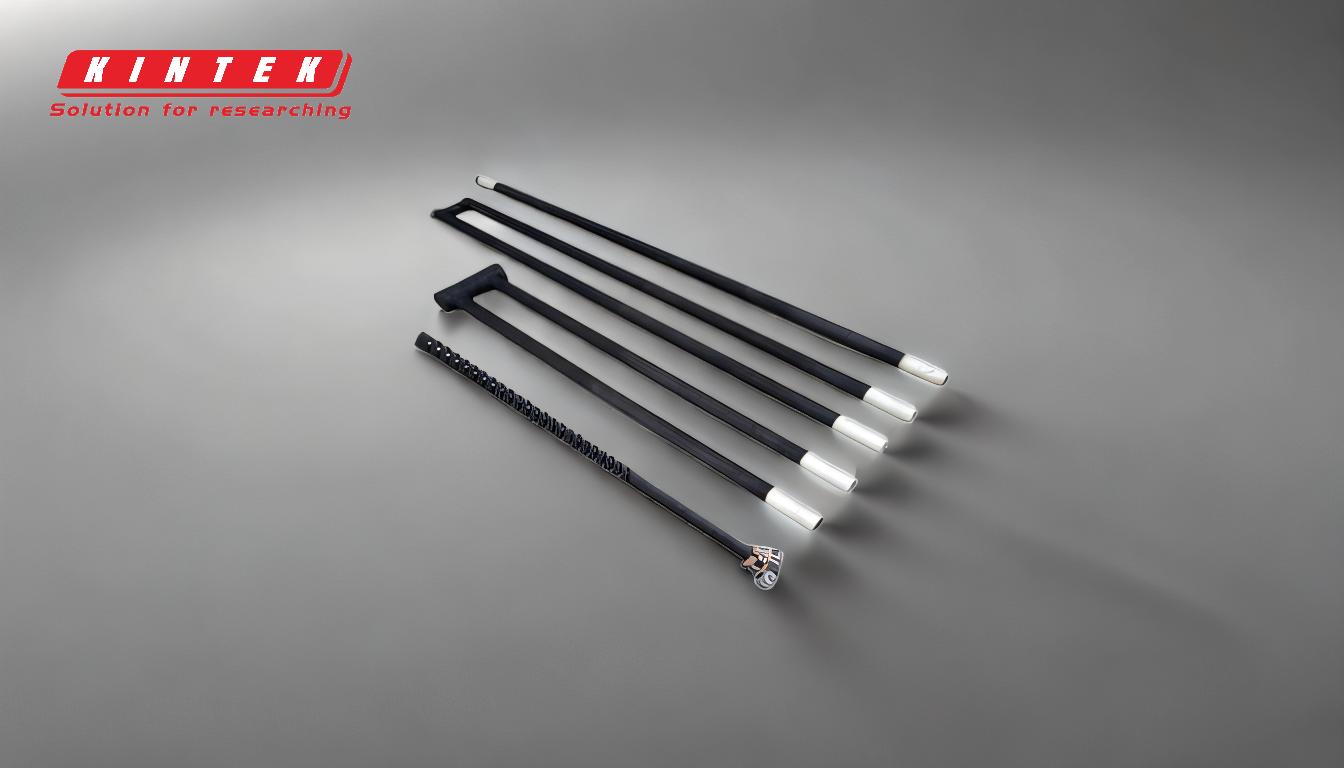
-
Thermal Expansion Coefficient of SiC
- The thermal expansion coefficient of SiC is 4.0 × 10⁻⁶/°C.
- This value is significantly lower than most other semiconductor and ceramic materials, making SiC highly dimensionally stable under varying temperatures.
- Low thermal expansion reduces the risk of cracking or deformation due to thermal stress, which is critical in applications involving rapid temperature changes.
-
Comparison to Other Materials
- SiC's thermal expansion is lower than that of many common materials, such as metals and other ceramics.
- For example, aluminum has a thermal expansion coefficient of about 23 × 10⁻⁶/°C, and steel is around 12 × 10⁻⁶/°C.
- This makes SiC particularly advantageous in environments where thermal mismatch between materials could lead to mechanical failure.
-
Thermal Shock Resistance
- The combination of low thermal expansion and high thermal conductivity (120–270 W/mK) gives SiC exceptional thermal shock resistance.
- Thermal shock resistance is the ability of a material to withstand rapid temperature changes without cracking or breaking.
- This property is crucial in applications such as aerospace, automotive, and industrial heating, where components are subjected to extreme thermal cycling.
-
High-Temperature Performance
- SiC maintains its mechanical strength and structural integrity at temperatures up to 1400°C, and even approaching 1600°C.
- This makes it ideal for use in high-temperature environments, such as in furnaces, gas turbines, and semiconductor manufacturing equipment.
- Its low thermal expansion ensures that it remains stable and reliable even under prolonged exposure to high temperatures.
-
Chemical and Mechanical Stability
- SiC is highly resistant to chemical corrosion, including resistance to strong acids, and maintains its properties in harsh environments.
- Its high hardness and wear resistance further enhance its durability in demanding applications.
- These properties, combined with its low thermal expansion, make SiC a preferred material for components exposed to both thermal and chemical stress.
-
Applications Leveraging Low Thermal Expansion
- Semiconductor Manufacturing: SiC's low thermal expansion and high thermal conductivity make it ideal for wafer handling and processing equipment.
- Aerospace and Defense: Components such as heat exchangers, nozzles, and structural parts benefit from SiC's stability under extreme conditions.
- Industrial Heating: SiC is used in heating elements, kiln furniture, and other high-temperature components due to its reliability and longevity.
- Automotive: In electric vehicles, SiC is used in power electronics and braking systems, where thermal management is critical.
-
Material Production and Properties
- SiC is produced by pressing or extruding and then sintering, resulting in a dense, high-strength material.
- Its low density, high elastic modulus, and superior chemical inertness further enhance its performance in thermal and mechanical applications.
- These properties, combined with its low thermal expansion, make SiC a versatile and reliable material for a wide range of industries.
In summary, the thermal expansion of SiC is a key factor in its widespread use across industries that require materials to perform reliably under extreme thermal and mechanical stress. Its low coefficient of thermal expansion, combined with other exceptional properties, ensures that SiC remains a material of choice for high-performance applications.
Summary Table:
Property | Value/Description |
---|---|
Thermal Expansion Coefficient | 4.0 × 10⁻⁶/°C |
Thermal Conductivity | 120–270 W/mK |
Maximum Operating Temperature | Up to 1600°C |
Key Applications | Semiconductor manufacturing, aerospace, industrial heating, automotive |
Advantages | Low thermal expansion, high thermal shock resistance, chemical stability, durability |
Interested in leveraging SiC's exceptional properties for your applications? Contact us today to learn more!