Thermal vapor deposition (TVD) is a specific type of physical vapor deposition (PVD) technique used to create thin films on substrates. It involves heating a solid material in a vacuum until it vaporizes, and then allowing the vapor to condense onto a substrate, forming a thin film. This method is widely used in industries such as semiconductors, optics, and electronics due to its ability to produce high-purity films with precise control over thickness and composition. The process is influenced by factors such as temperature, vacuum pressure, and substrate preparation, which determine the quality and properties of the deposited film.
Key Points Explained:
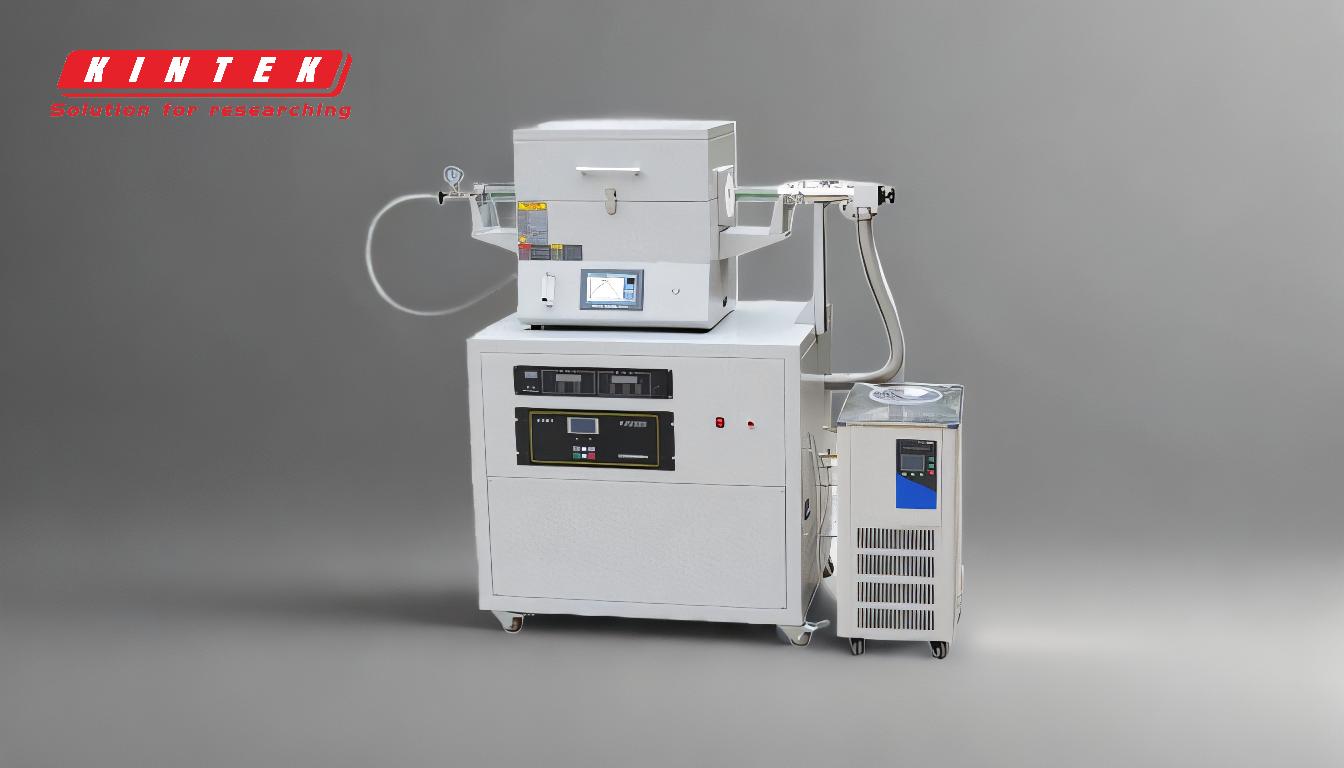
-
Definition and Classification of Thermal Vapor Deposition:
- Thermal vapor deposition is a subset of physical vapor deposition (PVD), which involves the physical transformation of a solid material into a vapor and its subsequent deposition onto a substrate.
- Unlike chemical vapor deposition (CVD), which relies on chemical reactions, TVD is purely a physical process, making it suitable for depositing materials that are sensitive to chemical reactions.
-
Basic Steps in Thermal Vapor Deposition:
- Vaporization: The solid material (target) is heated in a vacuum chamber until it vaporizes. This can be achieved using resistive heating, electron beams, or other heating methods.
- Transport: The vaporized material travels through the vacuum and reaches the substrate. The vacuum environment ensures minimal contamination and allows for precise control over the deposition process.
- Deposition: The vapor condenses onto the substrate, forming a thin film. The film's properties, such as thickness and uniformity, depend on factors like substrate temperature, deposition rate, and vacuum pressure.
- Post-Deposition Treatment: In some cases, the deposited film may undergo annealing or heat treatment to improve its structural and electrical properties.
-
Advantages of Thermal Vapor Deposition:
- High Purity: Since the process occurs in a vacuum, the risk of contamination is minimized, resulting in high-purity films.
- Precision: TVD allows for precise control over film thickness and composition, making it ideal for applications requiring fine layers, such as semiconductor devices and optical coatings.
- Versatility: A wide range of materials, including metals, alloys, and ceramics, can be deposited using TVD.
-
Applications of Thermal Vapor Deposition:
- Semiconductors: TVD is used to deposit thin films of silicon, germanium, and other semiconductor materials for integrated circuits and microelectronics.
- Optics: It is employed to create anti-reflective coatings, mirrors, and other optical components.
- Electronics: TVD is used to deposit conductive and insulating layers in electronic devices, such as transistors and capacitors.
- Flexible Electronics: With advancements in materials science, TVD is now used to deposit polymer-based thin films for applications like flexible solar cells and organic light-emitting diodes (OLEDs).
-
Factors Influencing the Quality of Deposited Films:
- Substrate Preparation: The cleanliness and surface properties of the substrate play a crucial role in film adhesion and uniformity.
- Deposition Rate: A controlled deposition rate ensures uniform film thickness and minimizes defects.
- Vacuum Pressure: Maintaining a high vacuum reduces contamination and allows for better control over the deposition process.
- Temperature: Both the substrate and the source material temperatures affect the film's microstructure and properties.
-
Comparison with Other Deposition Techniques:
- Chemical Vapor Deposition (CVD): Unlike TVD, CVD involves chemical reactions to form thin films. While CVD can produce high-quality films, it is less suitable for materials sensitive to chemical reactions.
- Sputtering: Sputtering is another PVD technique that uses energetic ions to eject atoms from a target material. It is more versatile than TVD but may require more complex equipment.
- Atomic Layer Deposition (ALD): ALD provides atomic-level control over film thickness but is generally slower and more expensive than TVD.
-
Challenges and Limitations:
- Material Limitations: Not all materials can be easily vaporized using thermal methods, limiting the range of materials that can be deposited.
- Uniformity: Achieving uniform film thickness over large areas can be challenging, especially for complex geometries.
- Cost: The need for high vacuum and precise temperature control can make TVD equipment expensive to operate and maintain.
In summary, thermal vapor deposition is a versatile and precise thin film deposition technique that plays a critical role in modern technology. Its ability to produce high-purity, uniform films makes it indispensable in industries ranging from semiconductors to optics. However, like any technique, it has its limitations and challenges, which must be carefully managed to achieve optimal results.
Summary Table:
Aspect | Details |
---|---|
Definition | A physical vapor deposition (PVD) technique for creating thin films. |
Key Steps | Vaporization, transport, deposition, and post-deposition treatment. |
Advantages | High purity, precision, and versatility in material deposition. |
Applications | Semiconductors, optics, electronics, and flexible electronics. |
Key Influencing Factors | Substrate preparation, deposition rate, vacuum pressure, and temperature. |
Limitations | Material limitations, uniformity challenges, and high operational costs. |
Discover how thermal vapor deposition can enhance your projects—contact our experts today!