Chemical vapor deposition (CVD) is a versatile manufacturing process used to create thin film coatings on various substrates. The thickness of these coatings can vary significantly depending on the application, material, and process parameters. CVD involves a chemical reaction of gaseous precursors that deposit a solid material onto a substrate, forming a thin film. The thickness of the deposited film is influenced by factors such as reaction time, temperature, pressure, and the nature of the substrate. Understanding these factors is crucial for achieving the desired film properties for specific applications.
Key Points Explained:
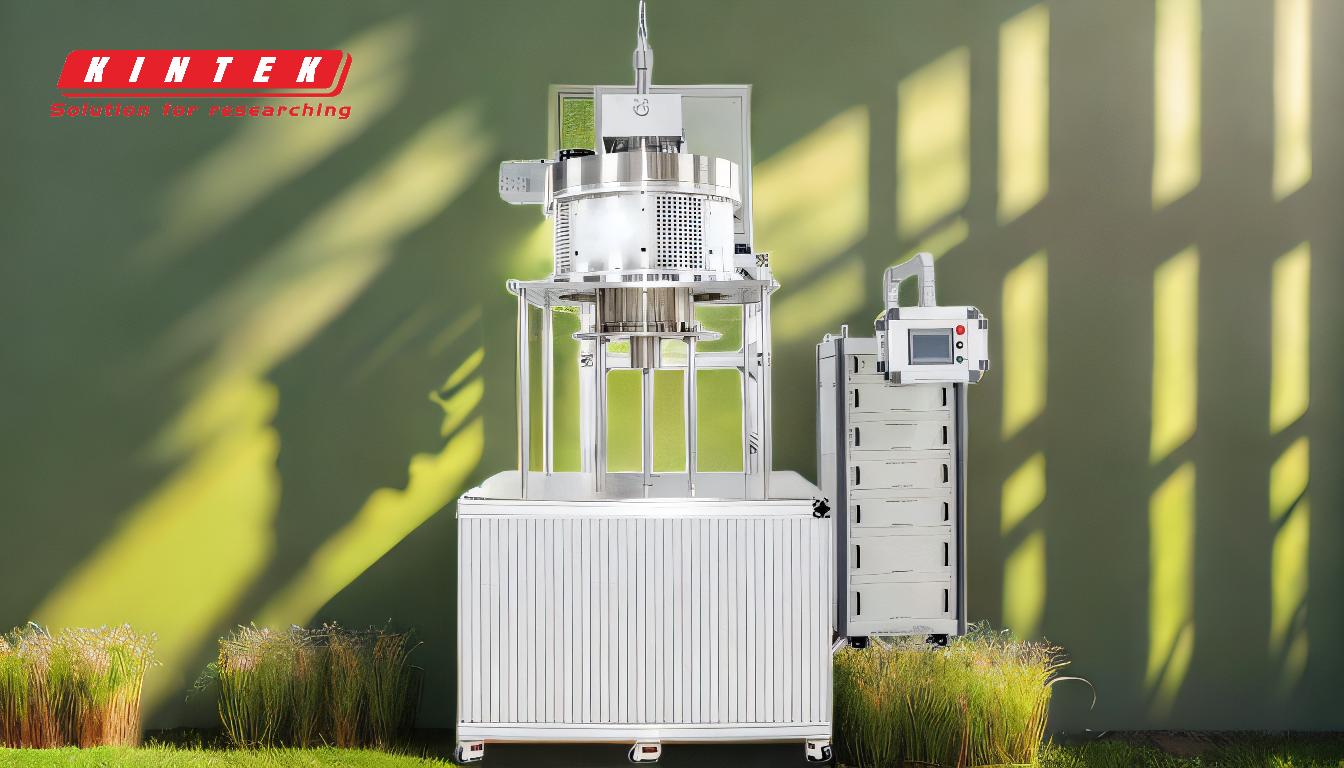
-
Definition of Chemical Vapor Deposition (CVD):
- CVD is a process where a solid material is deposited onto a substrate through the chemical reaction of gaseous precursors. The resulting thin film can range from nanometers to micrometers in thickness, depending on the application.
-
Factors Influencing Film Thickness:
- Reaction Time: Longer reaction times generally result in thicker films as more material is deposited.
- Temperature: Higher temperatures can increase the reaction rate, leading to thicker films, but excessive temperatures may cause defects.
- Pressure: The pressure within the reaction chamber affects the deposition rate and uniformity of the film.
- Substrate Properties: The nature of the substrate, including its surface roughness and chemical composition, can influence how the film adheres and grows.
-
Typical Thickness Range:
- CVD films can range from a few nanometers (for applications like semiconductor devices) to several micrometers (for protective coatings or optical layers). The exact thickness is tailored to the specific requirements of the application.
-
Applications and Thickness Requirements:
- Semiconductors: In semiconductor manufacturing, CVD is used to deposit thin films of materials like silicon dioxide or silicon nitride, often with thicknesses in the nanometer range.
- Protective Coatings: For applications requiring wear resistance or corrosion protection, thicker films in the micrometer range are common.
- Optical Coatings: CVD is also used to create optical layers with precise thicknesses to achieve desired light transmission or reflection properties.
-
Equipment and Process Control:
- The thickness of CVD films is controlled through precise management of the gas delivery system, reaction chamber conditions, and energy sources. Advanced process control systems ensure consistent and repeatable film thicknesses.
-
Challenges in Controlling Thickness:
- Achieving uniform thickness across large or complex substrates can be challenging. Variations in temperature, gas flow, or substrate properties can lead to non-uniform film growth.
- Advanced techniques like atomic layer deposition (ALD) are sometimes used for ultra-thin and highly uniform films.
By understanding these key points, purchasers of CVD equipment and consumables can make informed decisions about the specifications and capabilities needed for their specific applications. The ability to control and predict film thickness is critical for achieving the desired performance in the final product.
Summary Table:
Aspect | Details |
---|---|
Typical Thickness Range | Nanometers (semiconductors) to micrometers (protective/optical coatings) |
Key Influencing Factors | Reaction time, temperature, pressure, and substrate properties |
Applications | Semiconductors, protective coatings, optical layers |
Control Methods | Precise gas delivery, reaction chamber conditions, and energy source management |
Challenges | Uniformity across large/complex substrates; advanced techniques like ALD |
Need help selecting the right CVD equipment for your application? Contact our experts today for tailored solutions!