The thickness of thin films produced by Physical Vapor Deposition (PVD) typically ranges from 0.00004 to 0.0002 inches (approximately 1 to 5 micrometers). This thickness is influenced by various factors, including the deposition method (e.g., sputtering or evaporation), process parameters like cycle time, power applied, and material properties. PVD is a versatile vacuum-based deposition technique used to create thin films on substrates such as metals, ceramics, glass, and polymers. The process involves transitioning materials from a condensed phase to a vapor phase and then back to a thin film condensed phase. Achieving the desired thickness and quality requires precise control of factors like deposition temperature, substrate preparation, and vacuum conditions.
Key Points Explained:
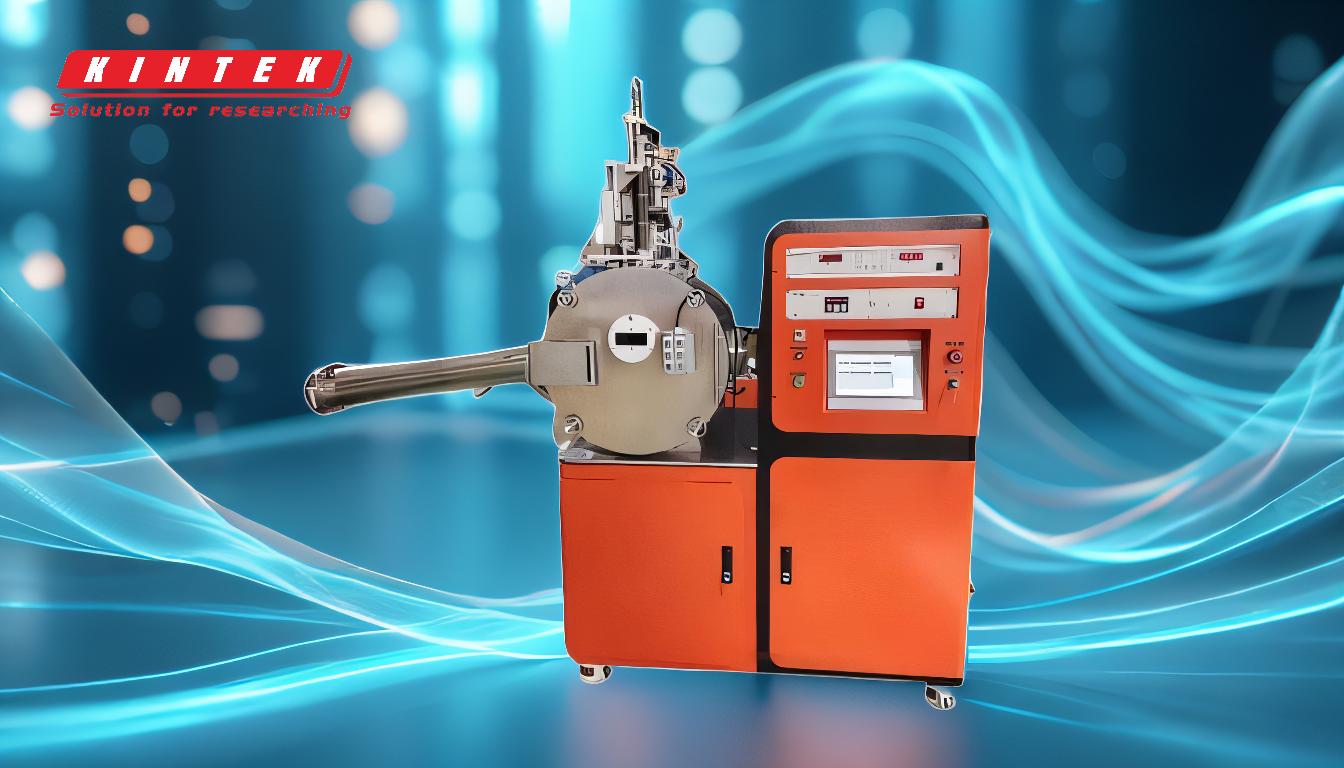
-
Typical Thickness Range of PVD Coatings:
- PVD coatings generally range in thickness from 0.00004 to 0.0002 inches (approximately 1 to 5 micrometers).
- This range is suitable for applications requiring tight tolerances and minimal material build-up.
- The thin nature of PVD coatings ensures that the surface finish of the substrate is replicated accurately.
-
Factors Influencing Thickness:
- Deposition Method: The two most common PVD methods, sputtering and evaporation, can produce different thicknesses based on their specific process parameters.
- Cycle Time: Longer sputtering or evaporation cycles result in thicker coatings.
- Power Applied: Higher power levels during sputtering increase the energy of coating particles, leading to faster deposition and potentially thicker films.
- Material Properties: The mass and energy level of the coating particles (ranging from tens to thousands of electron volts) affect the deposition rate and final thickness.
- Substrate Preparation: Proper cleaning and surface treatment of the substrate ensure uniform deposition and consistent thickness.
-
Process Parameters and Their Impact:
- Temperature: PVD processes typically operate within a temperature range of 320 to 900 degrees Fahrenheit. Higher temperatures can enhance adhesion and uniformity but may also affect the final thickness.
- Vacuum Conditions: The residual gas composition and pressure in the vacuum chamber influence the deposition rate and film quality.
- Line of Sight: PVD is a line-of-sight process, meaning the coating material travels in a straight line from the source to the substrate. This characteristic requires careful positioning of the substrate to achieve uniform thickness.
-
Advantages of PVD for Thin Film Deposition:
- Environmentally Friendly: PVD processes do not involve harmful chemicals, making them a sustainable choice for thin film production.
- High Purity: The vacuum environment ensures that the coatings are free from contaminants, resulting in high-purity thin films.
- Improved Surface Quality: PVD coatings enhance the surface properties of substrates, including hardness, wear resistance, and corrosion resistance.
-
Applications of PVD Thin Films:
- Industrial Coatings: PVD is widely used for coating tools, molds, and components to improve durability and performance.
- Decorative Finishes: The ability to replicate surface finishes makes PVD ideal for decorative applications on jewelry, watches, and architectural elements.
- Electronics: Thin films produced by PVD are used in semiconductors, solar cells, and optical devices due to their precise thickness control and high quality.
-
Comparison with Other Deposition Techniques:
- PVD offers better control over thickness compared to some other deposition methods, such as chemical vapor deposition (CVD), which can result in thicker and less uniform coatings.
- Unlike CVD, PVD does not require heat treatment after deposition, simplifying the process and reducing production time.
By understanding these key points, a purchaser or engineer can make informed decisions about using PVD for specific applications, ensuring optimal performance and cost-effectiveness.
Summary Table:
Aspect | Details |
---|---|
Thickness Range | 0.00004 to 0.0002 inches (1 to 5 micrometers) |
Deposition Methods | Sputtering, evaporation |
Key Influencing Factors | Cycle time, power applied, material properties, substrate preparation |
Temperature Range | 320 to 900 degrees Fahrenheit |
Applications | Industrial coatings, decorative finishes, electronics |
Advantages | Environmentally friendly, high purity, improved surface quality |
Achieve precise thin film coatings with PVD—contact our experts today for tailored solutions!