The tooling factor in e-beam evaporation refers to the ratio of the thickness of the deposited material on the substrate to the thickness of the source material that was evaporated. It is a critical parameter that accounts for the efficiency and uniformity of the deposition process. The tooling factor is influenced by several factors, including the geometry of the vacuum chamber, the position and orientation of the substrate relative to the source, and the material properties of both the source and the substrate. Understanding and optimizing the tooling factor is essential for achieving precise and consistent thin-film coatings in e-beam evaporation processes.
Key Points Explained:
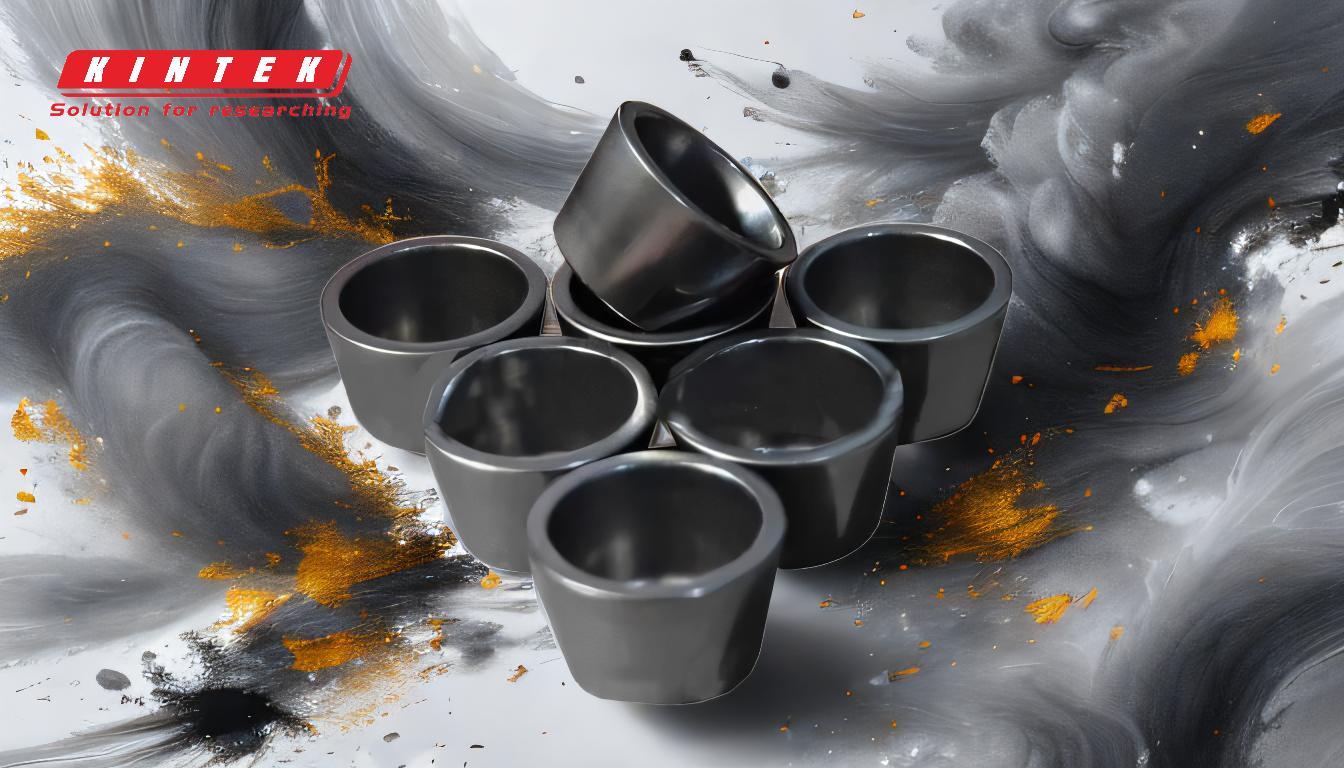
-
Definition of Tooling Factor:
- The tooling factor is a dimensionless ratio that quantifies the efficiency of material transfer from the source to the substrate during e-beam evaporation. It is calculated as the thickness of the deposited film on the substrate divided by the thickness of the source material that was evaporated.
- This factor is crucial for predicting and controlling the thickness of the deposited film, ensuring that the final product meets the desired specifications.
-
Factors Influencing the Tooling Factor:
- Geometry of the Vacuum Chamber: The shape and size of the vacuum chamber can affect the distribution of evaporated material. A well-designed chamber ensures a more uniform deposition across the substrate.
- Position and Orientation of the Substrate: The distance between the source and the substrate, as well as the angle at which the substrate is placed, can significantly impact the tooling factor. Proper alignment is necessary to achieve uniform film thickness.
- Material Properties: The properties of both the source material and the substrate, such as their thermal conductivity and melting points, can influence the evaporation rate and the adhesion of the deposited film.
-
Importance in E-Beam Evaporation:
- Precision and Consistency: A well-calibrated tooling factor allows for precise control over the thickness of the deposited film, which is essential for applications requiring high accuracy, such as in semiconductor manufacturing.
- Process Optimization: Understanding the tooling factor helps in optimizing the e-beam evaporation process, reducing material waste, and improving the overall efficiency of the deposition process.
-
Challenges and Considerations:
- Moderate System Complexity: E-beam evaporation systems are relatively complex, and achieving a consistent tooling factor requires careful calibration and maintenance of the equipment.
- Limited Scalability: The tooling factor can be affected by the scalability of the process, especially at reduced deposition rates. This can limit the throughput and utilization of the system.
- Moderate Costs: The costs associated with maintaining and calibrating the system to achieve an optimal tooling factor can be moderate, but they are necessary for ensuring high-quality results.
-
Comparison with Other Deposition Methods:
- When compared to other thin-film deposition methods like sputtering, e-beam evaporation offers distinct advantages in terms of film purity and the ability to deposit refractory materials. However, the tooling factor must be carefully managed to ensure that these advantages are fully realized.
In summary, the tooling factor is a critical parameter in e-beam evaporation that influences the efficiency, precision, and consistency of the deposition process. By understanding and optimizing this factor, manufacturers can achieve high-quality thin-film coatings that meet the stringent requirements of various industrial applications.
Summary Table:
Key Aspect | Details |
---|---|
Definition | Ratio of deposited film thickness to evaporated source material thickness. |
Influencing Factors | - Vacuum chamber geometry - Substrate position/orientation - Material properties |
Importance | Ensures precision, consistency, and efficiency in thin-film deposition. |
Challenges | - Moderate system complexity - Limited scalability - Moderate costs |
Comparison with Sputtering | Offers superior film purity and refractory material deposition capabilities. |
Optimize your e-beam evaporation process—contact our experts today for tailored solutions!