Sinter plays a crucial role in the blast furnace process, primarily serving as a prepared iron-bearing material that enhances the efficiency and productivity of ironmaking. It is produced by agglomerating fine iron ore particles, fluxes, and other additives into a porous, lumpy material through a sintering process. Sinter improves the permeability of the blast furnace burden, reduces coke consumption, and ensures a stable and consistent chemical composition, which is essential for efficient iron production. By replacing raw iron ore fines, sinter helps optimize the blast furnace operation, leading to better gas flow, reduced energy consumption, and improved overall performance.
Key Points Explained:
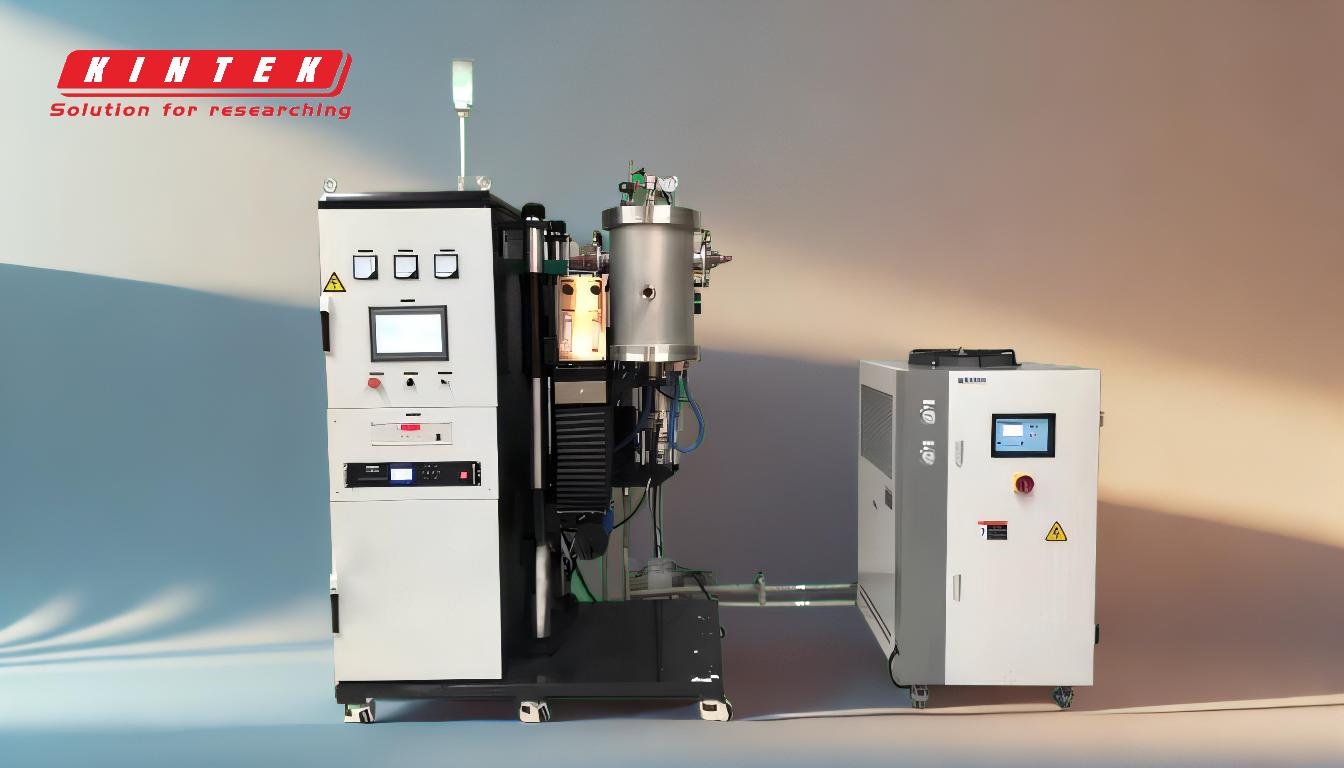
-
Enhances Permeability of the Blast Furnace Burden:
- Sinter is a porous material with a uniform structure, which improves the permeability of the blast furnace burden. This allows for better gas flow through the furnace, ensuring efficient heat transfer and chemical reactions.
- The uniform size and shape of sinter particles prevent the formation of dense layers, which can obstruct gas flow and reduce furnace efficiency.
-
Reduces Coke Consumption:
- Sinter contains pre-added fluxes, such as limestone or dolomite, which reduce the need for additional fluxes during the blast furnace operation. This lowers the coke requirement, as coke is primarily used as a reducing agent and heat source.
- The reduction in coke consumption not only decreases operational costs but also minimizes the environmental impact by reducing carbon emissions.
-
Ensures Consistent Chemical Composition:
- Sinter is produced with a controlled chemical composition, ensuring a stable and predictable input for the blast furnace. This consistency is critical for maintaining the desired quality of molten iron and slag.
- The uniform composition of sinter reduces the risk of fluctuations in the furnace's thermal and chemical conditions, leading to smoother operations and higher productivity.
-
Replaces Raw Iron Ore Fines:
- Raw iron ore fines are difficult to use directly in a blast furnace due to their fine particle size, which can lead to poor gas flow and inefficient combustion. Sinter provides a lumpy alternative that is easier to handle and more effective in the furnace.
- By using sinter, blast furnace operators can optimize the burden mix, improving the overall efficiency of the ironmaking process.
-
Improves Energy Efficiency:
- The use of sinter reduces the energy required for the blast furnace operation. The pre-heating and partial reduction of iron oxides during the sintering process lower the thermal load on the furnace.
- This energy efficiency translates to cost savings and a smaller carbon footprint, aligning with modern sustainability goals.
-
Facilitates Better Slag Formation:
- Sinter contains fluxes that promote the formation of slag with the desired properties, such as viscosity and melting point. Proper slag formation is essential for the removal of impurities and the smooth operation of the blast furnace.
- The controlled addition of fluxes in sinter ensures that the slag composition remains consistent, enhancing the overall efficiency of the ironmaking process.
In summary, sinter is a vital component in the blast furnace process, offering numerous benefits such as improved permeability, reduced coke consumption, consistent chemical composition, and enhanced energy efficiency. Its role in optimizing the burden mix and ensuring stable furnace operations makes it indispensable in modern ironmaking.
Summary Table:
Key Benefits of Sinter | Impact on Blast Furnace |
---|---|
Enhances Permeability | Improves gas flow, heat transfer, and chemical reactions. |
Reduces Coke Consumption | Lowers operational costs and carbon emissions. |
Ensures Consistent Composition | Stabilizes furnace conditions, improving molten iron quality. |
Replaces Raw Iron Ore Fines | Optimizes burden mix for better efficiency. |
Improves Energy Efficiency | Reduces thermal load, saving energy and costs. |
Facilitates Better Slag Formation | Ensures proper impurity removal and smooth furnace operation. |
Learn how sinter can revolutionize your ironmaking process—contact our experts today!