The PECVD (Plasma-Enhanced Chemical Vapor Deposition) process is a sophisticated method used to deposit thin films, such as silicon nitride, onto substrates like silicon wafers. It leverages low-temperature plasma to enable chemical reactions at lower temperatures than traditional CVD, making it more efficient and suitable for producing high-quality, uniform films. The process involves introducing process gases into a chamber, generating a glow discharge via an RF field, and allowing the gases to undergo chemical and plasma reactions to form a solid film on the substrate. This method is widely used in semiconductor manufacturing and photovoltaic cell production due to its precision and controllability.
Key Points Explained:
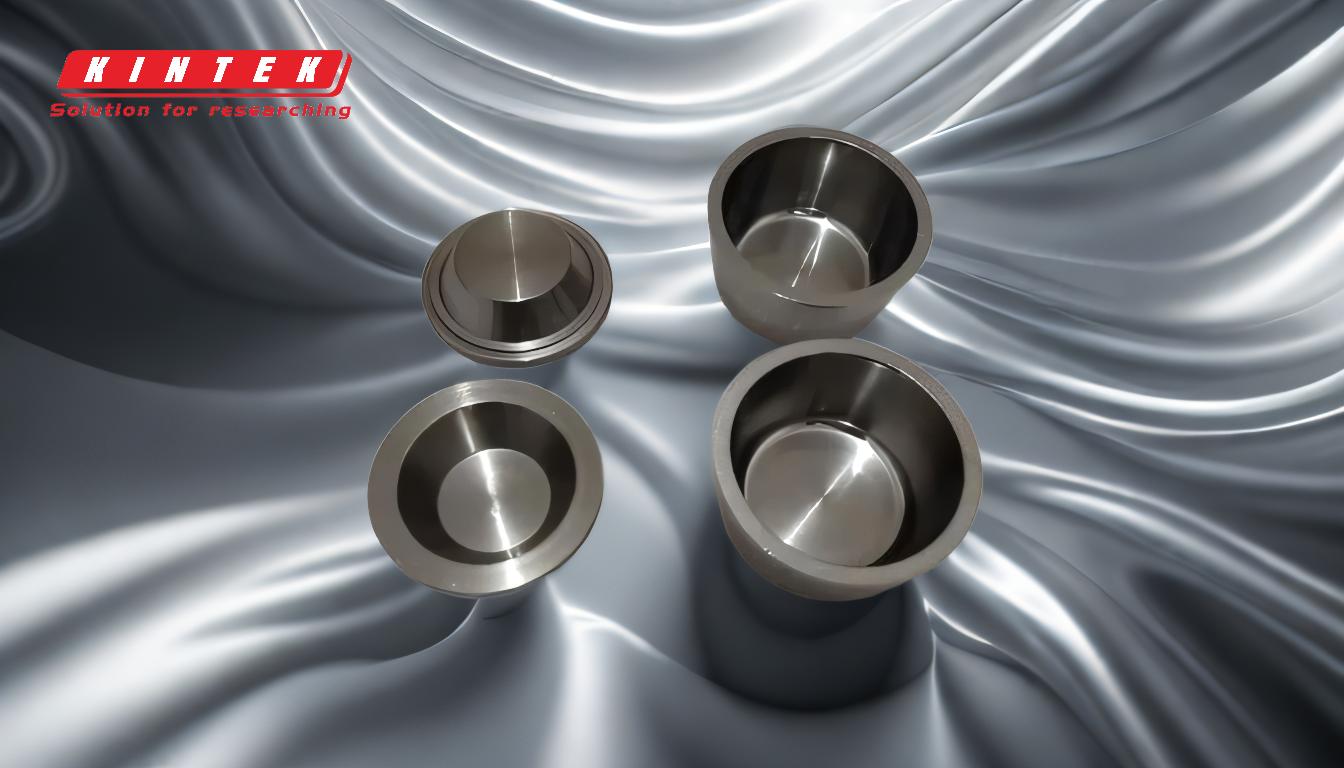
-
Introduction of Process Gases:
- The PECVD process begins by introducing process gases, such as SiH4 (silane) and NH3 (ammonia), into the reaction chamber. These gases are chosen based on the desired film composition.
- The gases are typically injected into the chamber at controlled flow rates to ensure uniformity and consistency in the deposition process.
-
Generation of Low-Temperature Plasma:
- A low-temperature plasma is generated within the chamber using an RF (radio frequency) field, typically operating at frequencies between 100 kHz and 40 MHz.
- This plasma creates a glow discharge on the cathode of the chamber, which ionizes the process gases and breaks them down into reactive species. The plasma environment is maintained at reduced gas pressures, typically between 50 mtorr and 5 torr.
-
Chemical and Plasma Reactions:
- The ionized gases undergo chemical and plasma reactions, forming reactive species that are essential for film deposition.
- These reactions occur at much lower temperatures compared to traditional CVD, thanks to the energetic discharge of the plasma, which decomposes gas molecules efficiently.
-
Film Deposition on the Substrate:
- The reactive species generated in the plasma diffuse to the substrate surface, where they adsorb and undergo surface-catalyzed reactions.
- This leads to the nucleation and growth of a thin film on the substrate. For example, in the case of silicon nitride deposition, the film forms uniformly over the silicon wafer.
-
Surface Diffusion and Film Formation:
- The adsorbed species diffuse across the substrate surface to growth sites, where they contribute to the continuous formation of the film.
- The process ensures that the film grows uniformly and adheres well to the substrate, resulting in high-quality, defect-free layers.
-
Desorption of Byproducts:
- Gaseous reaction byproducts are desorbed from the substrate surface and transported away from the reaction zone.
- This step is crucial to prevent contamination and ensure the purity of the deposited film.
-
Advantages of PECVD Over Conventional CVD:
- Lower Temperature: PECVD operates at significantly lower temperatures, making it suitable for temperature-sensitive substrates.
- Higher Efficiency: The use of plasma enhances the decomposition of gases, leading to faster deposition rates and higher efficiency.
- Uniform Films: The process produces highly uniform and high-quality films, essential for applications in semiconductor and photovoltaic industries.
-
Applications of PECVD:
- Semiconductor Manufacturing: PECVD is widely used to deposit dielectric layers, such as silicon nitride and silicon dioxide, in semiconductor devices.
- Photovoltaic Cells: The process is employed to create anti-reflective coatings and passivation layers on solar cells, enhancing their efficiency.
- Optical Coatings: PECVD is also used to deposit thin films for optical applications, such as anti-reflective coatings on lenses.
-
Process Control and Optimization:
- The PECVD process requires precise control over parameters such as gas flow rates, plasma power, pressure, and substrate temperature.
- Optimization of these parameters is essential to achieve the desired film properties, such as thickness, uniformity, and composition.
-
Challenges and Considerations:
- Equipment Complexity: PECVD systems are complex and require sophisticated facilities, which can increase production costs.
- Process Time: While PECVD is more efficient than traditional CVD, it may still require longer production times compared to other deposition methods.
- Scalability: The process may face challenges in scaling up for large-scale production, particularly in industries requiring high throughput.
In summary, the PECVD process is a highly controlled and efficient method for depositing thin films on substrates. By leveraging low-temperature plasma, it achieves high-quality, uniform films at lower temperatures than traditional CVD, making it indispensable in industries such as semiconductors and photovoltaics. However, the complexity and cost of the equipment, as well as the need for precise process control, are important considerations for its implementation.
Summary Table:
Key Aspect | Details |
---|---|
Process Gases | SiH4 (silane), NH3 (ammonia), chosen for desired film composition. |
Plasma Generation | RF field (100 kHz–40 MHz) creates low-temperature plasma at 50 mtorr–5 torr. |
Reactions | Chemical and plasma reactions form reactive species for film deposition. |
Film Deposition | Uniform thin films grow on substrates like silicon wafers. |
Advantages | Lower temperature, higher efficiency, and uniform film quality. |
Applications | Semiconductors, photovoltaic cells, optical coatings. |
Challenges | Equipment complexity, longer process times, scalability issues. |
Discover how PECVD can enhance your manufacturing process—contact our experts today!