The yield of plastic pyrolysis varies depending on several factors, including the type of plastic, operating conditions, and the pyrolysis technology used. Typically, plastic pyrolysis yields approximately 50-80% pyrolysis oil, 20-35% pyrolysis gas, and 3-30% pyrolysis residue. These yields are influenced by variables such as temperature, residence time, and the quality of the plastic feedstock. Higher temperatures generally favor gas production, while lower temperatures and slower heating rates may increase char or liquid yields. The cleanliness and composition of the plastic waste also play a significant role in determining the final product distribution.
Key Points Explained:
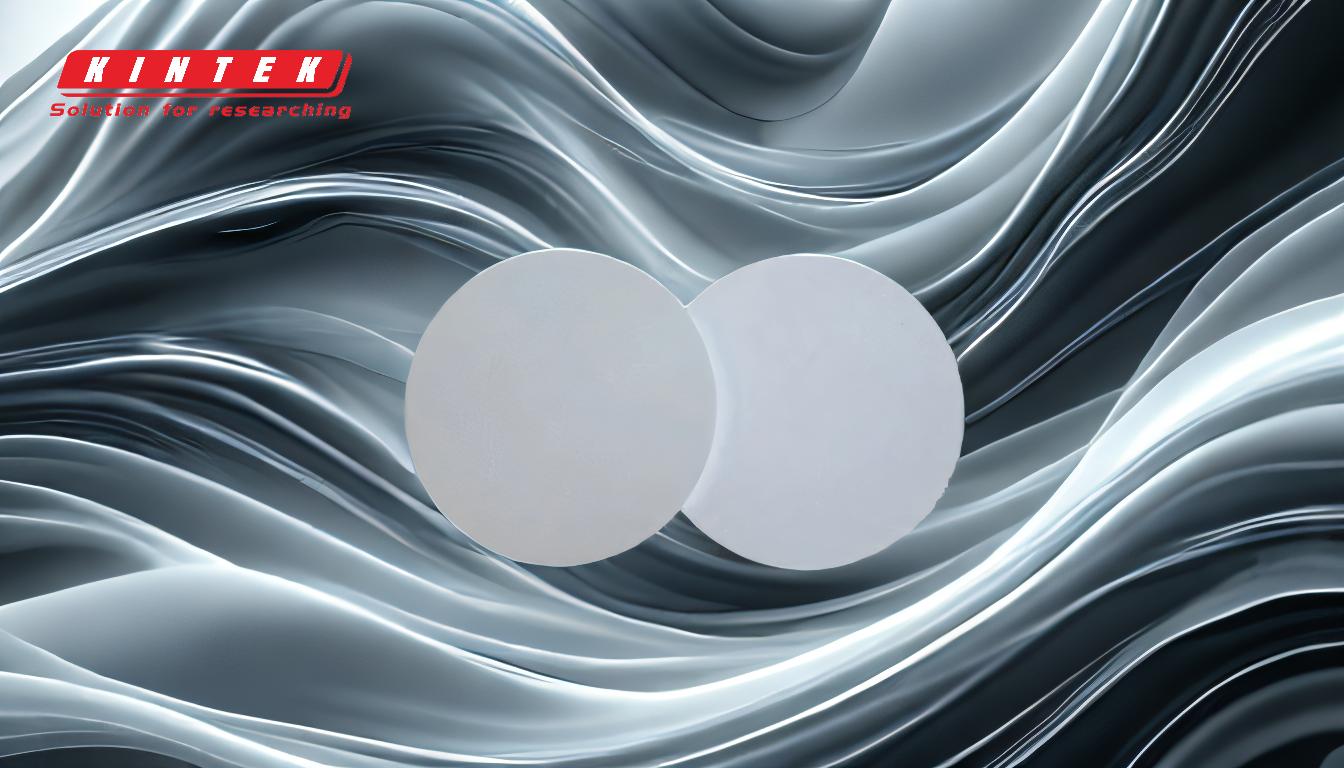
-
Typical Yields from Plastic Pyrolysis:
- Pyrolysis Oil: 50-80% yield.
- Pyrolysis Gas: 20-35% yield.
- Pyrolysis Residue (Char): 3-30% yield.
- These yields are approximate and can vary based on the specific conditions and feedstock used.
-
Factors Influencing Yield:
- Type of Plastic: Different plastics (e.g., polyethylene, polypropylene, polystyrene) have varying chemical structures, which affect their decomposition behavior and product distribution.
- Temperature: Higher pyrolysis temperatures (e.g., above 700°C) tend to favor gas production due to increased thermal cracking, while lower temperatures (e.g., 400-500°C) favor liquid and char production.
- Residence Time: Longer residence times in the reactor can lead to further cracking of liquids into gases, affecting the yield distribution.
- Feedstock Quality: Clean, dry, and homogeneous plastic waste generally results in higher yields of desirable products. Contaminants like soil or ash can reduce yields and affect product quality.
-
Operating Conditions and Their Impact:
- Low Temperature and Slow Heating Rate: Favors char production, as seen in slow pyrolysis processes, which can yield up to 50% char.
- Moderate Temperature and High Heating Rate: Optimal for maximizing liquid (oil) yields, as it promotes rapid decomposition of the plastic into condensable vapors.
- High Temperature and Long Residence Time: Enhances gas production by cracking heavier molecules into lighter gases like syngas (a mixture of hydrogen, carbon monoxide, and methane).
-
Comparison with Biomass Pyrolysis:
- While plastic pyrolysis yields are similar to biomass pyrolysis in terms of product categories (oil, gas, and char), the proportions can differ significantly. For example, biomass pyrolysis typically yields around 60% bio-oil, 20% biochar, and 20% syngas, whereas plastic pyrolysis often produces higher oil yields (50-80%) and lower char yields (3-30%).
-
Importance of Feedstock Preparation:
- Cleanliness: Removing contaminants like dirt, metals, and non-plastic materials improves yield and product quality.
- Moisture Content: Dry feedstock is preferable, as moisture can reduce the efficiency of the pyrolysis process and increase energy consumption.
- Plastic Type: Pure or single-type plastic feedstocks (e.g., only polyethylene) tend to yield more predictable and higher-quality products compared to mixed plastics.
-
Technology and Reactor Design:
- The type of pyrolysis reactor (e.g., fixed bed, fluidized bed, rotary kiln) can influence yield distribution. For instance, fluidized bed reactors often provide better heat transfer and more uniform temperature distribution, which can optimize yields.
- Advanced technologies, such as catalytic pyrolysis, can further enhance yields and product quality by promoting specific chemical reactions.
-
Environmental and Economic Considerations:
- Maximizing oil yield is often economically favorable, as pyrolysis oil can be used as a fuel or chemical feedstock.
- Gas yields, while lower, can be utilized for energy recovery within the pyrolysis plant, reducing external energy requirements.
- Char/residue yields, though minimal, can sometimes be used as a carbon-rich material or disposed of responsibly.
In summary, the yield of plastic pyrolysis is highly variable and depends on a combination of feedstock characteristics, operating conditions, and technology. By optimizing these factors, it is possible to achieve a desirable distribution of pyrolysis oil, gas, and residue, making the process both economically viable and environmentally sustainable.
Summary Table:
Factor | Impact on Yield |
---|---|
Type of Plastic | Different plastics yield varying oil, gas, and residue proportions. |
Temperature | Higher temps favor gas; lower temps favor oil and char. |
Residence Time | Longer times increase gas yield by cracking liquids. |
Feedstock Quality | Clean, dry, and homogeneous plastics improve yield and product quality. |
Reactor Technology | Advanced reactors (e.g., fluidized bed) optimize heat transfer and yield. |
Optimize your plastic pyrolysis process for maximum yield—contact our experts today!