Thermal effect via evaporation refers to the process where a material is heated to its evaporation point, causing it to transition from a solid or liquid state to a vapor state. This vapor then condenses onto a substrate to form a thin film. The process relies on the application of heat to achieve evaporation, and it is typically carried out in a vacuum environment to ensure the purity and quality of the deposited film. Thermal evaporation is widely used in thin-film deposition for applications in electronics, optics, and coatings due to its ability to produce films with good adhesion and purity.
Key Points Explained:
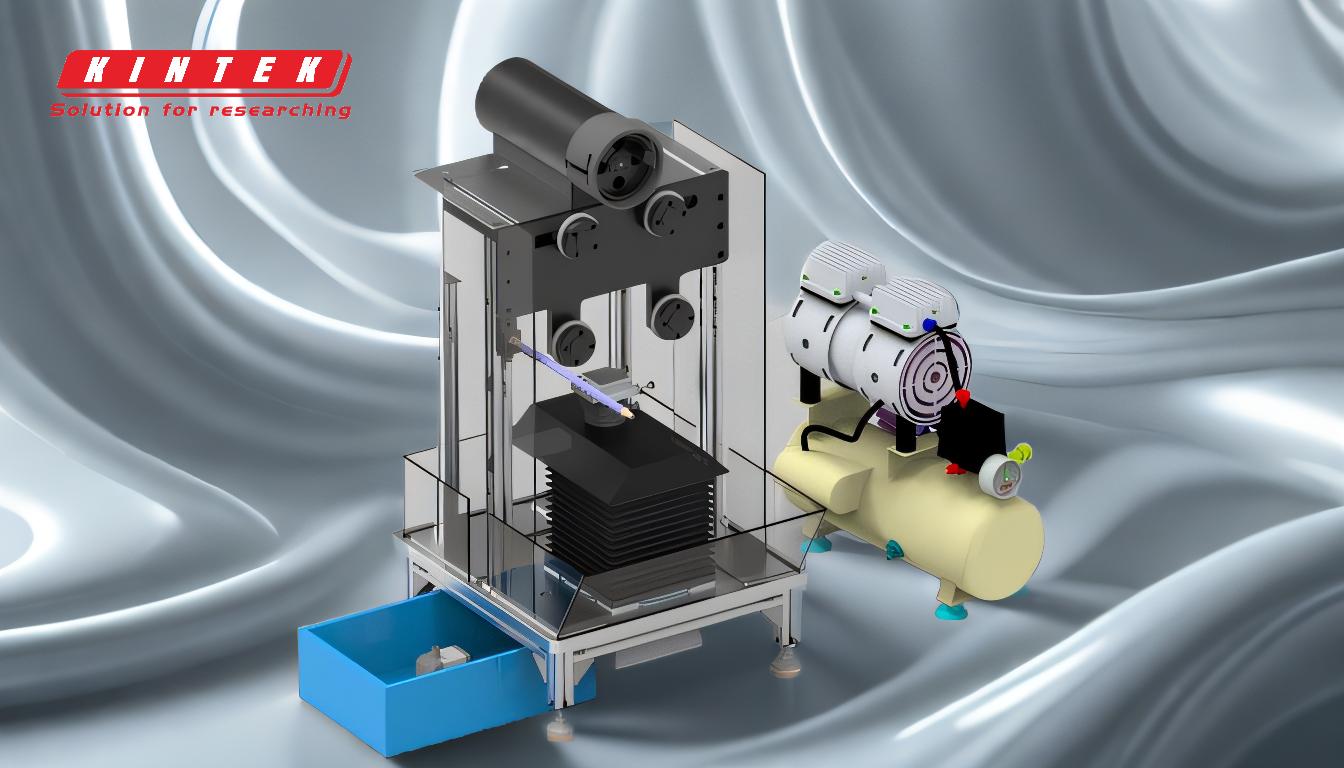
-
Definition of Thermal Evaporation:
- Thermal evaporation is a physical vapor deposition (PVD) technique where a material is heated to a high temperature until it evaporates. The vaporized material then travels through a vacuum and condenses onto a substrate, forming a thin film.
- This process is used to deposit thin films of metals, alloys, and other materials that remain stable in a vapor state.
-
Mechanism of Thermal Evaporation:
- The material to be evaporated is placed in a crucible, boat, or coil made of refractory metals like tungsten or molybdenum.
- Heat is applied to the material, either through resistive heating (Joule heating) or electron beam heating, until it reaches its evaporation temperature.
- Once evaporated, the material's atoms or molecules travel through the vacuum chamber and deposit onto the substrate, forming a thin film.
-
Heat Sources in Thermal Evaporation:
- Resistive Heating: A refractory metal element (such as a boat or coil) is heated by passing an electric current through it. The heat generated causes the material in the boat to evaporate.
- Electron Beam Heating: A focused beam of high-energy electrons is directed at the material, providing localized heating and causing evaporation. This method is particularly useful for materials with high evaporation temperatures.
-
Vacuum Environment:
- Thermal evaporation is typically performed in a high vacuum environment to minimize contamination and ensure the vaporized material travels unimpeded to the substrate.
- The vacuum also reduces the presence of reactive gases, which could otherwise react with the evaporating material and degrade the quality of the film.
-
Applications of Thermal Evaporation:
- Electronics: Used to deposit thin films of metals (e.g., aluminum, gold) for semiconductor devices, interconnects, and electrodes.
- Optics: Applied in the production of reflective coatings, anti-reflective coatings, and optical filters.
- Coatings: Used for protective and decorative coatings on various substrates, including glass, plastics, and metals.
-
Advantages of Thermal Evaporation:
- High Purity: The vacuum environment and controlled heating ensure minimal contamination, resulting in high-purity films.
- Good Adhesion: The evaporated material forms strong bonds with the substrate, leading to excellent adhesion.
- Versatility: Can be used to deposit a wide range of materials, including metals, alloys, and some compounds.
-
Limitations of Thermal Evaporation:
- Material Limitations: Not all materials can be evaporated using this method, especially those with very high melting points or those that decompose before evaporating.
- Uniformity Challenges: Achieving uniform thickness across large substrates can be difficult, particularly for complex geometries.
- Energy Consumption: The process requires significant energy input to achieve the necessary evaporation temperatures.
-
Comparison with Other PVD Techniques:
- Sputtering: Unlike thermal evaporation, sputtering involves bombarding a target material with ions to eject atoms, which then deposit onto the substrate. Sputtering can handle materials with higher melting points and provides better uniformity for large-area coatings.
- Chemical Vapor Deposition (CVD): CVD involves chemical reactions to deposit films, often at lower temperatures, but it requires reactive gases and can introduce impurities.
By understanding the thermal effect via evaporation, one can appreciate its role in modern manufacturing and research, particularly in the development of thin films for advanced technologies. The process's simplicity, combined with its ability to produce high-quality films, makes it a valuable tool in various industries.
Summary Table:
Aspect | Details |
---|---|
Definition | A PVD technique where materials are heated to evaporate and form thin films. |
Heat Sources | Resistive heating or electron beam heating. |
Vacuum Environment | Ensures high purity and minimizes contamination. |
Applications | Electronics, optics, and protective coatings. |
Advantages | High purity, good adhesion, and versatility. |
Limitations | Material constraints, uniformity challenges, and high energy consumption. |
Discover how thermal evaporation can enhance your thin-film processes—contact us today for expert advice!