Thermal evaporation deposition is a widely used physical vapor deposition (PVD) technique for creating thin films. It involves heating a solid material in a vacuum chamber until it evaporates, and then allowing the vapor to condense onto a substrate, forming a thin, uniform layer. This method is highly versatile and finds applications in industries such as optics, electronics, packaging, and even aerospace. It is particularly effective for depositing metals and certain polymers, making it a key technology in the production of devices like OLEDs, solar cells, and thin-film transistors. The process is conducted in a high vacuum to minimize contamination and ensure high-quality film deposition.
Key Points Explained:
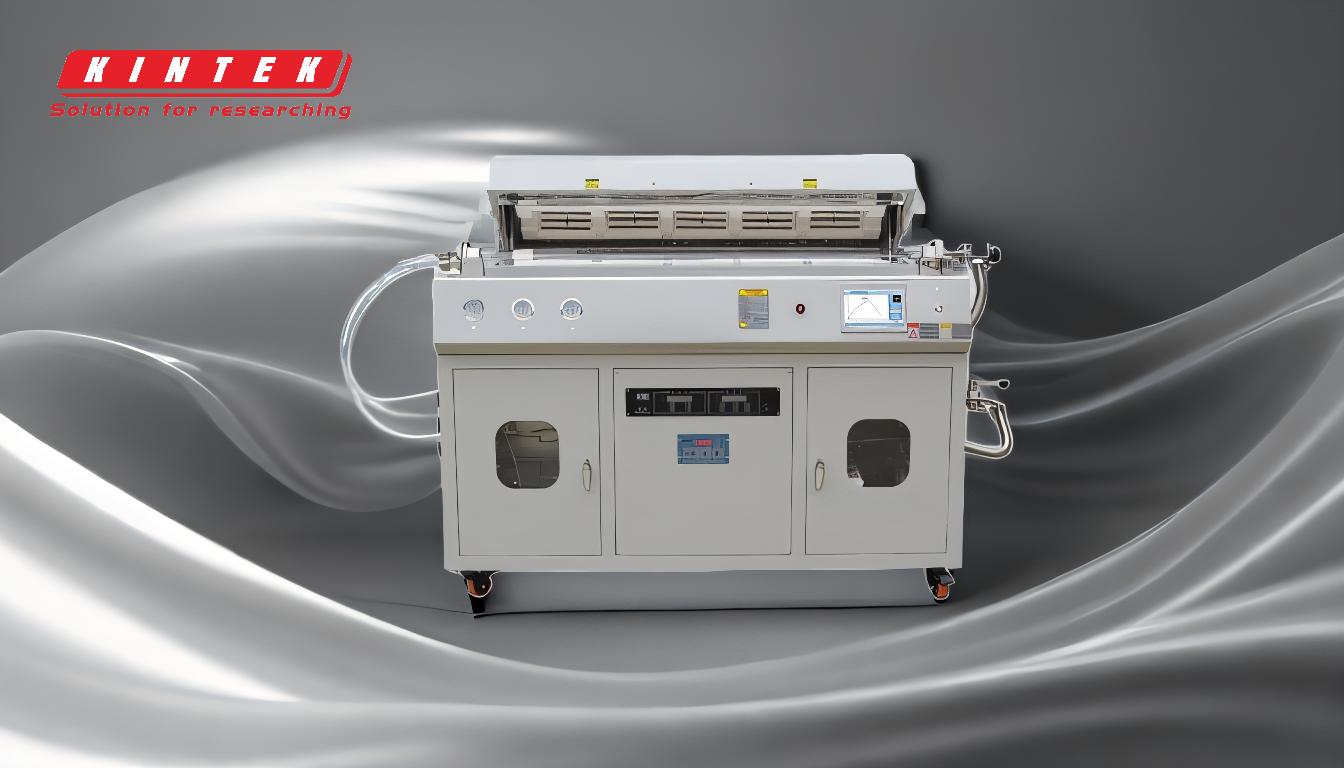
-
Definition and Process of Thermal Evaporation Deposition:
- Thermal evaporation deposition is a PVD technique where a solid material is heated in a vacuum chamber until it evaporates. The vapor then condenses onto a substrate, forming a thin film.
- The process involves two main steps: evaporation of the source material and its subsequent condensation on the substrate.
- This method is typically performed in a high vacuum to reduce gas collisions, unwanted reactions, and trapped gas layers, ensuring a clean and uniform deposition. For more details, see thermal evaporation.
-
Applications of Thermal Evaporation Deposition:
- Optics: Used for lens coatings, anti-reflective layers, and UV protection.
- Electronics: Essential for ultra-thin metal plating in OLEDs, solar cells, and thin-film transistors.
- Packaging: Applied for depositing aluminum films on plastic packaging, enhancing barrier properties and aesthetics.
- Aerospace and Safety: Utilized in NASA spacesuits, firefighter uniforms, and emergency blankets for thermal insulation and protection.
- Jewellery and Accessories: Employed for aesthetic thin-film coatings on decorative items.
-
Materials Deposited via Thermal Evaporation:
- Metals: Commonly used for depositing single metals like silver and aluminum, as well as co-depositing multiple components by controlling the temperature of individual crucibles.
- Polymers: Successful in depositing small polymers, such as PTFE and nylon, in metal-polymer nanocomposite films. This technique can handle polymers with molecular weights up to several thousand g/mol.
-
Advantages of Thermal Evaporation:
- High Purity: The vacuum environment minimizes contamination, resulting in high-quality films.
- Versatility: Suitable for a wide range of materials, including metals and certain polymers.
- Line-of-Sight Deposition: Ensures uniform coating on substrates within direct line of sight of the source material.
-
Comparison with Other Deposition Techniques:
- Unlike chemical vapor deposition (CVD), which involves chemical reactions to form thin films, thermal evaporation relies on physical processes (evaporation and condensation).
- Thermal evaporation is particularly favored for applications requiring high-purity metal films, whereas CVD is more commonly used for semiconductor materials and complex nanostructures like graphene.
-
Key Considerations for Equipment Purchasers:
- Vacuum Chamber Quality: High-quality vacuum chambers are essential to maintain the required vacuum levels and minimize contamination.
- Heat Source Precision: Resistive heat sources must provide precise temperature control to ensure consistent evaporation rates.
- Substrate Compatibility: The equipment should accommodate various substrate sizes and shapes, depending on the application.
- Scalability: For industrial applications, consider systems that can handle large-scale production while maintaining film quality.
By understanding these key points, equipment and consumable purchasers can make informed decisions when selecting thermal evaporation systems for their specific applications.
Summary Table:
Aspect | Details |
---|---|
Process | Heating a solid material in a vacuum until it evaporates and condenses. |
Applications | Optics, electronics, packaging, aerospace, and decorative coatings. |
Materials Deposited | Metals (e.g., silver, aluminum) and small polymers (e.g., PTFE, nylon). |
Advantages | High purity, versatility, and uniform line-of-sight deposition. |
Key Considerations | Vacuum chamber quality, heat source precision, substrate compatibility, scalability. |
Ready to enhance your thin film production? Contact our experts today to find the perfect thermal evaporation system for your needs!