Thermal evaporation is a fundamental technique in Physical Vapor Deposition (PVD) used to create thin films on substrates. It involves heating a material in a vacuum until it vaporizes, and then allowing the vapor to condense onto a cooler substrate, forming a thin film. This process is widely used in industries such as electronics, optics, and coatings due to its simplicity and ability to deposit high-purity materials. The method relies on precise control of temperature and vacuum conditions to ensure uniform and high-quality film deposition. Thermal evaporation can be achieved using various heating methods, including resistive heating, electron beams, or lasers, depending on the material and application requirements.
Key Points Explained:
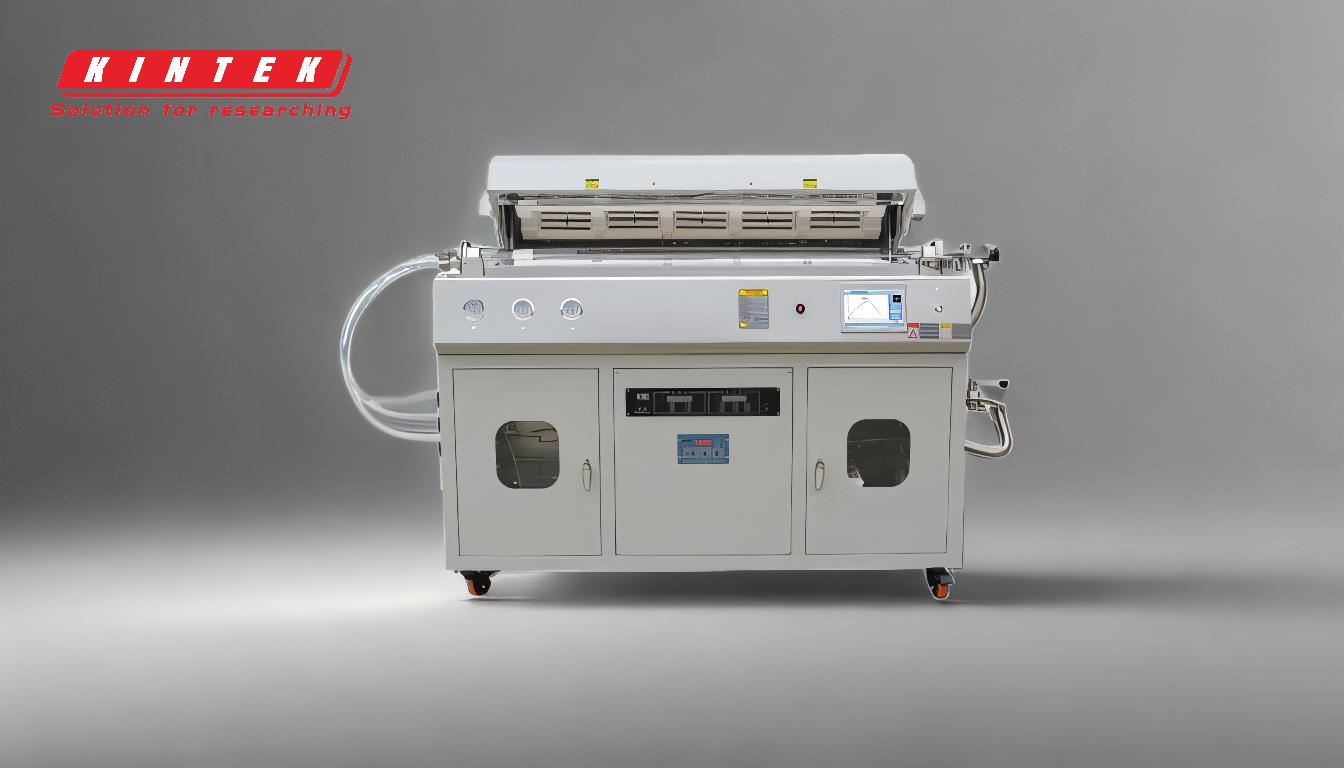
-
Definition and Purpose of Thermal Evaporation in PVD:
- Thermal evaporation is a PVD technique used to deposit thin films of materials onto substrates.
- The process involves heating a source material in a vacuum until it vaporizes, and then allowing the vapor to condense onto a cooler substrate.
- This method is commonly used to create coatings with thicknesses ranging from angstroms to microns, which can be single-layered or multi-layered.
-
Key Components of the Process:
- Source Material: The material to be deposited, which can be in solid or liquid form.
- Vacuum Chamber: A high-vacuum environment is essential to minimize contamination and ensure the vaporized material travels unimpeded to the substrate.
- Heating Mechanism: The material is heated using methods such as resistive heating, electron beams, lasers, or electric arcs, depending on the material's properties and the desired deposition rate.
- Substrate: The surface onto which the vaporized material condenses to form a thin film. The substrate is typically maintained at a lower temperature than the source material.
-
Steps in the Thermal Evaporation Process:
- Material Heating: The source material is heated until it reaches its vaporization temperature, either through sublimation (solid to vapor) or boiling (liquid to vapor).
- Vapor Transport: The vaporized material travels through the vacuum chamber to the substrate. The high vacuum ensures minimal collisions with other particles, enabling a direct and efficient deposition process.
- Condensation and Film Formation: The vapor condenses on the cooler substrate, forming a thin film. The film's properties, such as thickness and uniformity, depend on factors like deposition rate, substrate temperature, and vacuum conditions.
-
Advantages of Thermal Evaporation:
- High Purity: The vacuum environment minimizes contamination, resulting in high-purity films.
- Simplicity: The process is relatively simple and cost-effective compared to other PVD techniques.
- Versatility: It can deposit a wide range of materials, including metals, semiconductors, and insulators.
- Precision: Allows for precise control over film thickness and composition.
-
Applications of Thermal Evaporation:
- Electronics: Used to deposit conductive and insulating layers in semiconductor devices, solar cells, and displays.
- Optics: Applied in the production of reflective coatings, anti-reflective coatings, and optical filters.
- Coatings: Used for decorative, protective, and functional coatings on various materials, including metals, glass, and plastics.
-
Heating Methods in Thermal Evaporation:
- Resistive Heating: A common method where a resistive element heats the source material. Suitable for materials with lower vaporization temperatures.
- Electron Beam Evaporation: Uses a focused electron beam to heat the material, ideal for high-melting-point materials.
- Laser Evaporation: Employs a laser to vaporize the material, offering precise control and minimal contamination.
- Electric Arc Evaporation: Utilizes an electric arc to vaporize the material, often used for reactive materials.
-
Challenges and Limitations:
- Material Limitations: Some materials may decompose or react before reaching their vaporization temperature.
- Uniformity: Achieving uniform film thickness can be challenging, especially for large or complex substrates.
- Energy Efficiency: The process can be energy-intensive, particularly for high-melting-point materials.
- Scalability: Scaling up the process for industrial applications may require significant modifications and optimization.
-
Comparison with Other PVD Techniques:
- Sputtering: Unlike thermal evaporation, sputtering involves bombarding a target material with ions to eject atoms, which then deposit onto the substrate. Sputtering is better suited for materials with high melting points and offers better step coverage.
- Pulsed Laser Deposition (PLD): PLD uses a laser to ablate material from a target, providing precise control over film composition and structure but with higher equipment costs.
- Chemical Vapor Deposition (CVD): CVD involves chemical reactions to deposit films, offering better conformal coverage but requiring more complex equipment and processes.
In summary, thermal evaporation is a versatile and widely used PVD technique for depositing thin films with high purity and precision. Its simplicity and effectiveness make it a preferred choice for many applications in electronics, optics, and coatings. However, careful consideration of material properties, heating methods, and process parameters is essential to achieve optimal results.
Summary Table:
Aspect | Details |
---|---|
Definition | PVD technique for depositing thin films by vaporizing materials in a vacuum. |
Key Components | Source material, vacuum chamber, heating mechanism, substrate. |
Process Steps | Material heating, vapor transport, condensation, and film formation. |
Advantages | High purity, simplicity, versatility, and precise control. |
Applications | Electronics, optics, and coatings. |
Heating Methods | Resistive heating, electron beams, lasers, electric arcs. |
Challenges | Material limitations, uniformity, energy efficiency, scalability. |
Discover how thermal evaporation can enhance your thin film processes—contact our experts today!