Thermal evaporation is a widely used physical vapor deposition (PVD) technique for creating thin films. It involves heating a solid material in a high vacuum chamber until it evaporates, producing a vapor stream that travels through the vacuum and deposits onto a substrate, forming a thin film. This method is particularly useful for applications like OLEDs and thin-film transistors due to its simplicity and ability to produce uniform coatings. The process relies on two key principles: evaporation of the source material and the use of a heat source, such as a tungsten heating element or electron beam, to achieve the necessary thermal energy. The vacuum environment ensures minimal contamination and uniform deposition.
Key Points Explained:
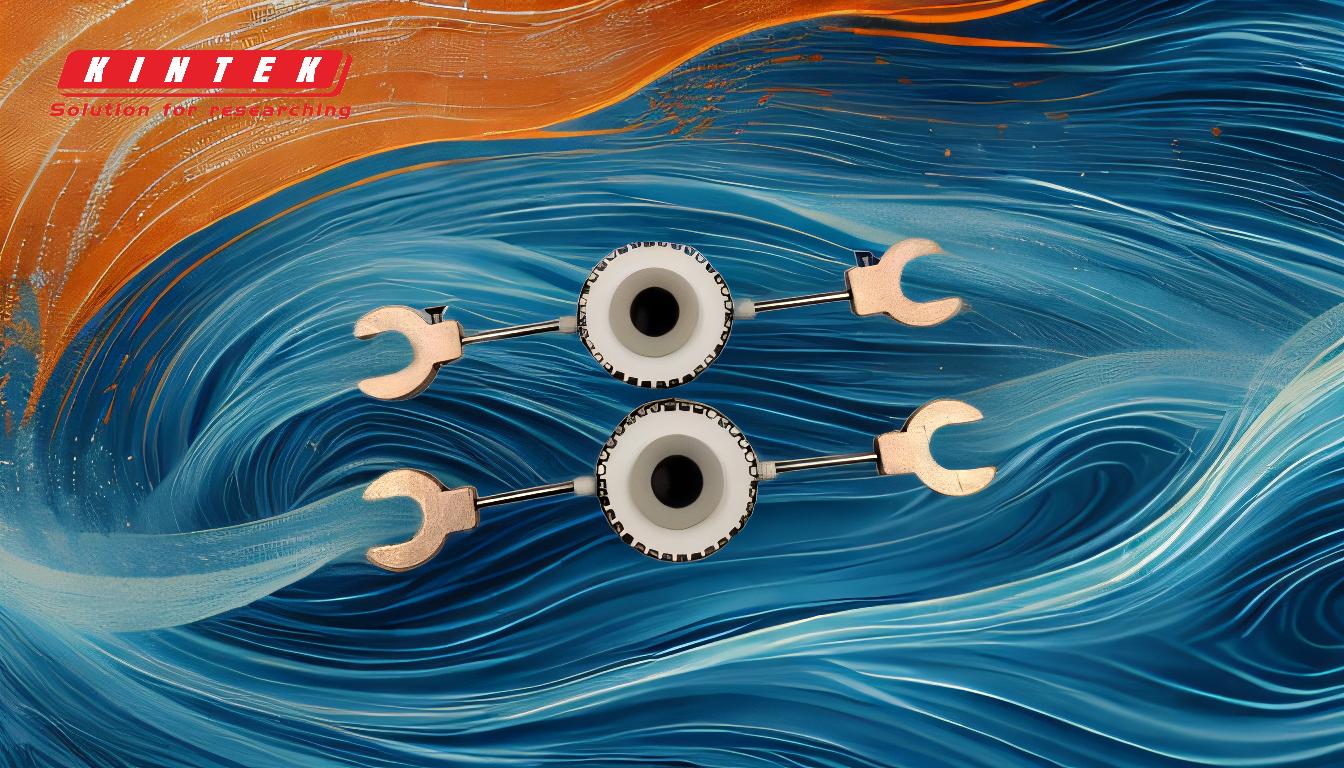
-
Definition and Purpose of Thermal Evaporation:
- Thermal evaporation is a physical vapor deposition (PVD) method used to create thin films on substrates.
- It is particularly effective for applications in electronics, such as OLEDs and thin-film transistors, due to its ability to produce uniform and high-quality coatings.
-
Process Overview:
- The process begins with placing the target material (solid) in a high vacuum chamber.
- The material is heated using a thermal energy source, such as a tungsten heating element or an electron beam, until it reaches its evaporation point.
- Once evaporated, the material forms a vapor cloud within the vacuum chamber.
-
Role of the Vacuum Environment:
- The vacuum environment is critical to the process as it prevents contamination from gases or impurities.
- It also ensures that the vaporized material travels unimpeded through the chamber, without scattering or reacting with other atoms, leading to a uniform deposition on the substrate.
-
Deposition of the Thin Film:
- The vaporized material travels through the vacuum and condenses onto the substrate, forming a solid thin film.
- The substrate can be made of various materials, depending on the application, such as glass, silicon, or polymers.
-
Heat Sources in Thermal Evaporation:
- Resistive Heating: A tungsten heating element is commonly used to provide the thermal energy needed to evaporate the target material.
- Electron Beam Evaporation: An electron beam can be used to melt and evaporate materials that require higher temperatures or are difficult to evaporate using resistive heating.
-
Advantages of Thermal Evaporation:
- Simplicity: The process is straightforward and does not require complex equipment.
- Uniform Coatings: The vacuum environment ensures that the deposited film is uniform and free from defects.
- Versatility: It can be used with a wide range of materials, including metals, semiconductors, and dielectrics.
-
Applications of Thermal Evaporation:
- OLEDs (Organic Light-Emitting Diodes): Thermal evaporation is used to deposit organic layers in OLED displays.
- Thin-Film Transistors: It is employed in the fabrication of thin-film transistors used in electronic devices.
- Optical Coatings: The technique is also used to create reflective or anti-reflective coatings for optical components.
-
Challenges and Considerations:
- Material Limitations: Some materials may not be suitable for thermal evaporation due to their high melting points or reactivity.
- Vacuum Maintenance: Maintaining a high vacuum is essential, and any leaks can compromise the quality of the thin film.
- Substrate Compatibility: The substrate must be able to withstand the deposition process without degrading.
In summary, thermal evaporation is a versatile and effective method for creating thin films, particularly in the electronics and optics industries. Its reliance on a vacuum environment and controlled heat sources ensures high-quality, uniform coatings, making it a preferred choice for many applications.
Summary Table:
Aspect | Details |
---|---|
Definition | Physical vapor deposition (PVD) method for creating thin films. |
Key Principle | Evaporation of source material in a high vacuum environment. |
Heat Sources | Tungsten heating elements or electron beams. |
Advantages | Simple process, uniform coatings, versatile material compatibility. |
Applications | OLEDs, thin-film transistors, optical coatings. |
Challenges | Material limitations, vacuum maintenance, substrate compatibility. |
Discover how thermal evaporation can enhance your thin film processes—contact us today!