Thermal evaporation under a vacuum is a widely used Physical Vapor Deposition (PVD) technique for coating substrates with thin films. It involves heating a solid material in a high vacuum chamber until it reaches its evaporation point, producing vapor pressure. The vaporized material then travels through the vacuum chamber and deposits onto a substrate, forming a thin, uniform film. This process is also known as resistive evaporation because the heat is often generated by electrical resistance in an evaporation source (e.g., boat, coil, or basket). The vacuum environment ensures minimal interference from air molecules, allowing precise control over the deposition process and resulting in high-quality coatings.
Key Points Explained:
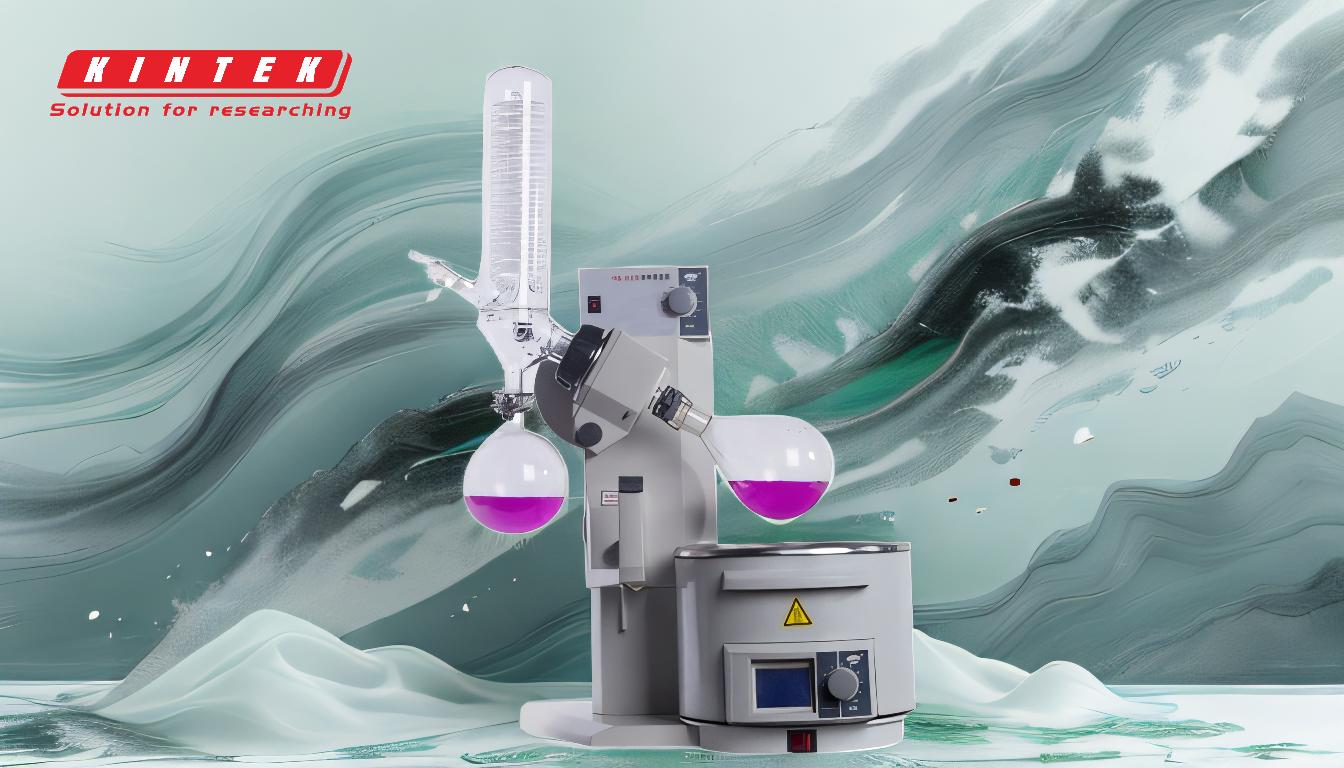
-
Definition and Purpose of Thermal Evaporation:
- Thermal evaporation is a Physical Vapor Deposition (PVD) process used to deposit thin films onto substrates.
- It is commonly employed in industries such as electronics, optics, and aerospace for applications like semiconductor fabrication, anti-reflective coatings, and protective layers.
-
Vacuum Environment:
- The process occurs in a high vacuum chamber, which is essential for several reasons:
- It minimizes contamination from air molecules, ensuring a pure deposition.
- It reduces the mean free path of the vaporized material, allowing it to travel directly to the substrate without collisions.
- It prevents oxidation or other chemical reactions that could degrade the coating material.
- The process occurs in a high vacuum chamber, which is essential for several reasons:
-
Heating Mechanism:
- The coating material is heated using an evaporation source, such as a boat, coil, or basket, which is typically made of refractory metals like tungsten or molybdenum.
- Heating is achieved by passing an electric current through the source, generating heat through electrical resistance (hence the term "resistive evaporation").
- The material is heated until it reaches its evaporation point, producing a vapor stream.
-
Vaporization and Deposition:
- Once the material reaches its evaporation point, it transitions from a solid to a vapor state.
- The vaporized atoms or molecules travel through the vacuum chamber and deposit onto the substrate.
- The substrate is positioned at a specific distance and angle to ensure uniform coating.
-
Advantages of Thermal Evaporation:
- High Purity: The vacuum environment ensures minimal contamination, resulting in high-purity films.
- Precision: The process allows for precise control over film thickness and composition.
- Versatility: A wide range of materials, including metals, alloys, and some compounds, can be deposited using this method.
- Cost-Effectiveness: It is relatively simple and cost-effective compared to other PVD techniques.
-
Limitations of Thermal Evaporation:
- Material Compatibility: Not all materials are suitable for thermal evaporation, especially those with very high melting points or complex compositions.
- Uniformity Challenges: Achieving uniform coatings on complex or three-dimensional substrates can be difficult.
- Energy Consumption: The process requires significant energy to maintain the vacuum and heat the material.
-
Applications:
- Electronics: Used for depositing conductive and insulating layers in semiconductor devices.
- Optics: Applied in the production of anti-reflective coatings, mirrors, and filters.
- Aerospace: Used for creating protective coatings on components exposed to extreme conditions.
- Decorative Coatings: Employed in the production of decorative finishes on consumer products.
-
Comparison with Other PVD Techniques:
- Unlike sputtering, which uses plasma to eject material from a target, thermal evaporation relies solely on heat to vaporize the material.
- Thermal evaporation is generally faster and more straightforward but may not achieve the same level of adhesion or uniformity as sputtering for certain materials.
-
Process Optimization:
- Key parameters to optimize include:
- Vacuum level: Higher vacuum reduces contamination and improves film quality.
- Substrate temperature: Controlled heating or cooling of the substrate can influence film adhesion and structure.
- Deposition rate: Adjusting the heating power and material quantity to achieve the desired film thickness.
- Key parameters to optimize include:
-
Future Trends:
- Advances in evaporation sources and vacuum technology are improving the efficiency and versatility of thermal evaporation.
- Integration with other deposition techniques, such as chemical vapor deposition (CVD), is expanding its applications in nanotechnology and advanced materials.
By understanding these key points, equipment and consumable purchasers can make informed decisions about selecting thermal evaporation systems and materials for their specific applications.
Summary Table:
Key Aspect | Details |
---|---|
Process | Thermal evaporation is a PVD technique using heat to vaporize materials. |
Vacuum Environment | Ensures minimal contamination and precise control over deposition. |
Heating Mechanism | Uses resistive heating sources like boats, coils, or baskets. |
Advantages | High purity, precision, versatility, and cost-effectiveness. |
Limitations | Material compatibility, uniformity challenges, and high energy consumption. |
Applications | Electronics, optics, aerospace, and decorative coatings. |
Future Trends | Advances in evaporation sources and integration with other techniques. |
Ready to explore thermal evaporation for your applications? Contact us today to learn more!