Thermal Plasma Chemical Vapor Deposition (TPCVD) is an advanced variant of the Chemical Vapor Deposition (CVD) process, which leverages thermal plasma to enhance the deposition of materials onto substrates. This method is particularly effective for creating high-quality, uniform thin films and coatings with precise control over material properties. TPCVD is widely used in industries requiring high-performance materials, such as electronics, optics, and photovoltaics, due to its ability to produce materials with superior mechanical, thermal, and electrical properties.
Key Points Explained:
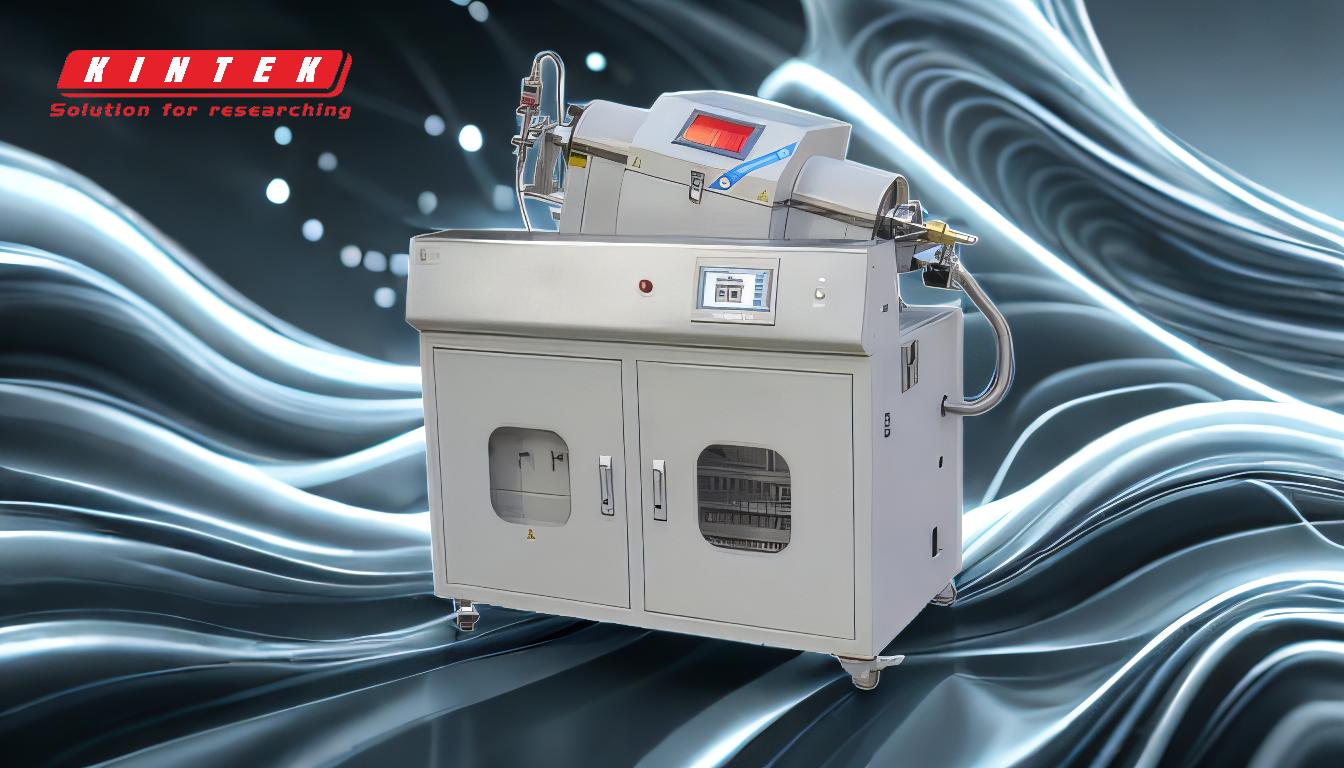
-
Fundamentals of Thermal Plasma CVD:
- Thermal Plasma Generation: In TPCVD, thermal plasma is generated by ionizing a gas using high-energy sources, such as electric arcs or radiofrequency (RF) induction. This plasma reaches extremely high temperatures, often exceeding 10,000 K, which facilitates the dissociation of precursor gases into reactive species.
- Reactive Species Formation: The high-energy environment of the thermal plasma breaks down the precursor gases into ions, radicals, and other reactive species. These species are highly reactive and can readily deposit onto the substrate to form the desired material.
-
Deposition Process:
- Transport of Reactive Species: The reactive species generated in the plasma are transported to the substrate surface, where they undergo chemical reactions to form a solid film. This process is highly controlled, allowing for precise deposition of materials with specific properties.
- Film Growth: The reactive species condense on the substrate, forming a thin film. The high energy of the plasma ensures that the deposited material has excellent adhesion and uniformity, which are critical for applications in electronics and optics.
-
Advantages of TPCVD:
- High Deposition Rates: The high energy of the thermal plasma allows for rapid deposition of materials, making TPCVD an efficient process for industrial applications.
- Enhanced Material Properties: The high temperatures and reactive environment of the plasma result in materials with superior mechanical, thermal, and electrical properties. This is particularly beneficial for applications requiring high-performance coatings and thin films.
- Versatility: TPCVD can be used to deposit a wide range of materials, including metals, ceramics, and composites, making it a versatile technique for various industrial applications.
-
Applications of TPCVD:
- Electronics: TPCVD is used in the fabrication of semiconductor devices, where it is essential to deposit high-quality thin films with precise control over material properties.
- Optics and Photovoltaics: The ability to deposit uniform, high-performance coatings makes TPCVD ideal for applications in optics and photovoltaics, where material properties such as transparency and conductivity are critical.
- Wear and Corrosion Resistance: TPCVD is also used to deposit coatings that provide enhanced wear and corrosion resistance, which are important for industrial applications in harsh environments.
-
Comparison with Other CVD Techniques:
- Plasma-Enhanced CVD (PECVD): Unlike PECVD, which uses low-temperature plasma to deposit materials, TPCVD employs high-temperature thermal plasma, resulting in higher deposition rates and better material properties.
- Thermal CVD: Traditional thermal CVD relies on thermal energy alone to dissociate precursor gases, which limits the deposition rate and the quality of the deposited material. TPCVD overcomes these limitations by using high-energy plasma.
In summary, Thermal Plasma Chemical Vapor Deposition is a powerful and versatile technique that leverages the high energy of thermal plasma to deposit high-quality materials with superior properties. Its applications span across various industries, including electronics, optics, and photovoltaics, making it a critical technology for the development of advanced materials and devices.
Summary Table:
Aspect | Details |
---|---|
Process | Uses thermal plasma to deposit materials onto substrates. |
Key Feature | High-energy plasma breaks down precursor gases into reactive species. |
Advantages | High deposition rates, enhanced material properties, and versatility. |
Applications | Electronics, optics, photovoltaics, wear and corrosion-resistant coatings. |
Comparison with PECVD | Higher deposition rates and better material properties than PECVD. |
Comparison with Thermal CVD | Overcomes limitations of traditional CVD with high-energy plasma. |
Interested in leveraging TPCVD for your high-performance materials? Contact us today to learn more!