Thermal vapor deposition (TVD) is a physical vapor deposition (PVD) technique used to create thin films or coatings on substrates. It involves heating a solid material in a high vacuum chamber until it vaporizes, producing a vapor stream that deposits onto a substrate, forming a thin film. This process is widely used in industries such as optics, electronics, consumer packaging, and aerospace due to its ability to produce precise and uniform coatings. The material is typically heated to temperatures between 250°C and 350°C, and the vacuum environment ensures minimal contamination and efficient deposition. Applications range from solar cells and OLEDs to decorative coatings and functional layers in advanced materials.
Key Points Explained:
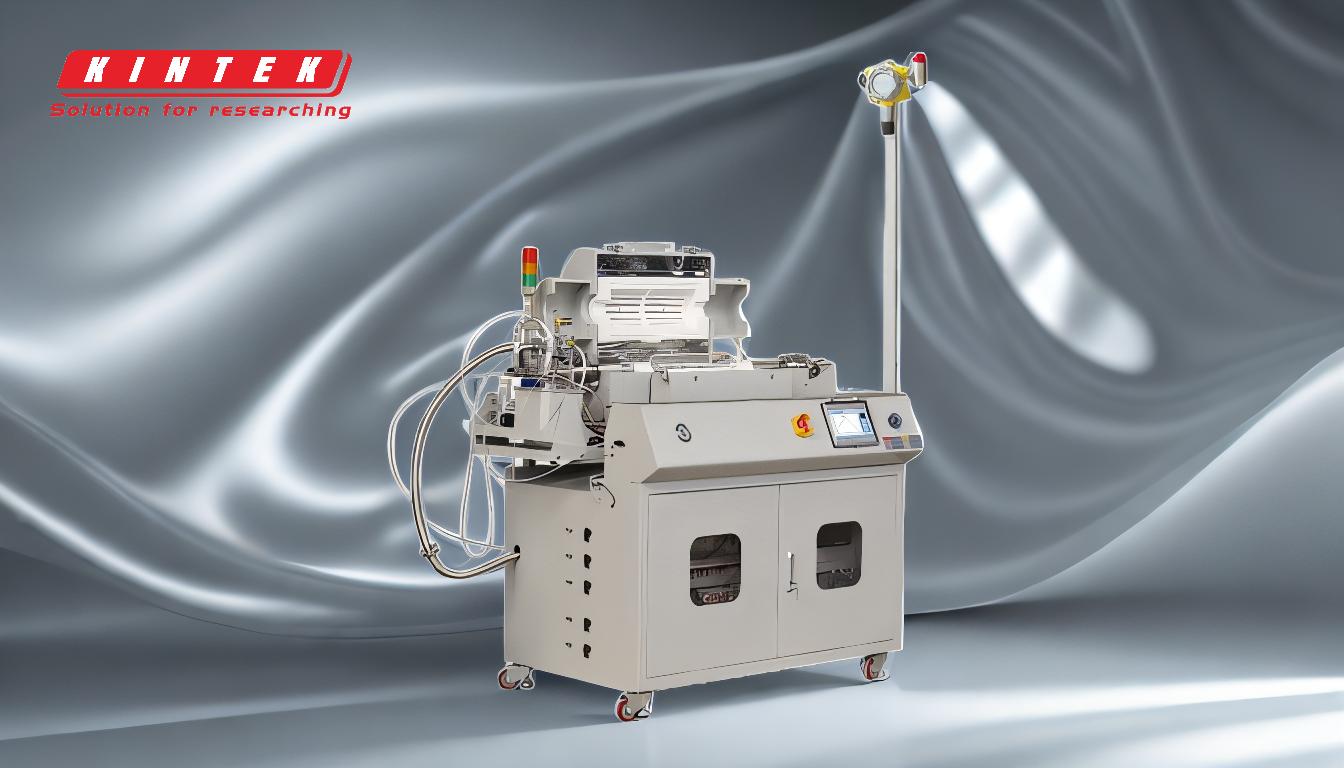
-
Definition and Process of Thermal Vapor Deposition:
- Thermal vapor deposition is a PVD method where a solid material is heated in a high vacuum chamber until it vaporizes.
- The vaporized material forms a vapor stream that travels through the chamber and deposits onto a substrate, creating a thin film.
- Heating is typically achieved using an electric heater or filament, and the process requires precise temperature control (usually between 250°C and 350°C).
-
Role of Vacuum Environment:
- The high vacuum chamber is essential for minimizing contamination and ensuring the vapor stream travels unimpeded to the substrate.
- Even low vapor pressure in the vacuum is sufficient to create a vapor cloud, which adheres to the substrate as a coating.
-
Applications of Thermal Vapor Deposition:
- Optics: Used for lens coatings, anti-reflective layers, and UV protection.
- Electronics: Deposits ultra-thin metal layers for OLEDs, solar cells, and thin-film transistors.
- Consumer Packaging: Creates aluminum films on plastic packaging for food and other products.
- Jewellery and Accessories: Provides aesthetic thin-film coatings for decorative purposes.
- Advanced Materials: Used in NASA spacesuits, firefighter uniforms, emergency blankets, and anti-static or soundproof enclosures in aircraft.
-
Advantages of Thermal Vapor Deposition:
- Produces highly uniform and precise thin films.
- Suitable for a wide range of materials, including metals and polymers.
- Operates at relatively low temperatures compared to other deposition methods.
- Versatile applications across multiple industries.
-
Key Considerations for Equipment and Consumables:
- Heat Source: An efficient and precise electric heater or filament is required to achieve the necessary vaporization temperatures.
- Vacuum Chamber: Must maintain a high vacuum to ensure clean and efficient deposition.
- Substrate Preparation: Proper cleaning and preparation of the substrate are critical for optimal adhesion of the thin film.
- Material Selection: The source material must be compatible with the heating process and capable of producing a stable vapor stream.
-
Industry-Specific Examples:
- Solar Cells: Used to deposit metal bonding layers and conductive coatings.
- OLEDs: Creates ultra-thin metal layers for improved performance and durability.
- Food Packaging: Deposits aluminum films on plastic for barrier properties and aesthetic appeal.
- Aerospace: Provides functional coatings for heat and sound insulation in aircraft and spacecraft.
By understanding these key points, equipment and consumable purchasers can make informed decisions about the materials and systems needed for thermal vapor deposition processes, ensuring high-quality results across various applications.
Summary Table:
Key Aspect | Details |
---|---|
Process | Heating solid material in a vacuum chamber to create a vapor stream. |
Temperature Range | 250°C to 350°C. |
Applications | Optics, electronics, consumer packaging, aerospace, and advanced materials. |
Advantages | Precise, uniform coatings; low-temperature operation; versatile materials. |
Key Equipment | Electric heater, high vacuum chamber, substrate preparation tools. |
Industry Examples | Solar cells, OLEDs, food packaging, aerospace coatings. |
Ready to enhance your processes with thermal vapor deposition? Contact us today to learn more!